Rapid Sand Casting Revolutionizing the Casting Industry
Rapid sand casting is an innovative approach to traditional sand casting that aims to streamline the manufacturing process while enhancing efficiency and reducing production times. This method combines the best aspects of rapid prototyping and sand casting to create high-quality metal components faster and at a lower cost.
The traditional sand casting process involves creating a mold from a mixture of sand, clay, and water. This mixture is then packed around a pattern of the desired component, which is removed to leave a hollow cavity. Molten metal is poured into this cavity to form the final product. While effective, conventional sand casting can be time-consuming, particularly in pattern creation and mold preparation.
Rapid sand casting addresses these limitations by incorporating modern technologies such as 3D printing and computer-aided design (CAD). With 3D printing, complex patterns can be created quickly and with high precision, eliminating the need for lengthy machining processes. This rapid pattern creation not only accelerates production times but also allows for more intricate designs that may not be feasible with traditional methods.
rapid sand casting
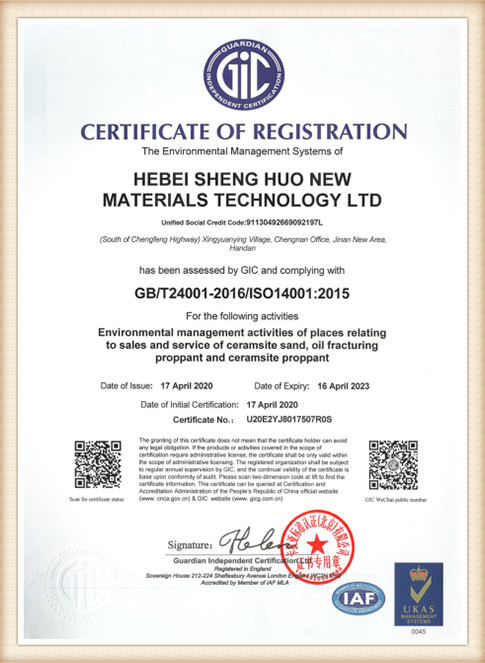
Another benefit of rapid sand casting is the reduction of material waste. Traditional casting processes often require significant amounts of sand and metal, and any imperfections or faults in the casting may lead to scrap. However, by utilizing advanced simulation software during the design phase, manufacturers can optimize their molds and minimize material usage. This enhances overall efficiency and sustainability—two critical factors in today’s manufacturing landscape.
Furthermore, rapid sand casting can be particularly advantageous for low to medium volume production runs
. Industries such as automotive, aerospace, and custom manufacturing can leverage this technique to produce high-quality components without the heavy financial burden typically associated with large-scale production. As companies seek to bring products to market faster, the agile capabilities of rapid sand casting provide a competitive edge.Collaboration plays a significant role in the success of rapid sand casting. By fostering partnerships between design engineers, foundry specialists, and technology providers, manufacturers can enhance their capabilities further. Continuous feedback loops help to refine processes, improve designs, and optimize material use, creating a dynamic environment that drives innovation.
In conclusion, rapid sand casting represents a significant advancement in the casting industry, offering numerous benefits such as reduced production times, lower costs, and improved design flexibility. As technology continues to evolve, this method is likely to become increasingly prevalent, paving the way for a more efficient and sustainable future in metal manufacturing. Embracing these modern techniques will not only transform how products are made but also help businesses meet the growing demands of a fast-paced market.
Post time:Nov . 07, 2024 06:12
Next:Composition Analysis of Foundry Sand for Casting Applications