Lost Foam Casting Coating An Overview
Lost foam casting (LFC) is an innovative manufacturing process that has gained popularity in various industries for its ability to create complex shapes with high precision. This method offers several advantages over traditional casting techniques, notably the reduction of weight loss during the casting process and elimination of the need for conventional molds. However, one critical aspect that significantly impacts the quality of final products in lost foam casting is the coating used during the process.
The coating in lost foam casting is essential for several reasons. Primarily, it serves as a barrier between the foam pattern and the molten metal, which helps to ensure that the surface of the final casting remains smooth and free of defects. Properly applied coatings can minimize the risk of fusion between the foam and the metal, which can lead to surface irregularities. The coating also acts to protect the foam during the heating process, preventing it from burning too quickly and allowing more time for the molten metal to flow properly.
Typically, the coating material is composed of a mixture of fine sand and a binding agent. This mix is applied to the foam pattern in order to create a shell that will withstand the molten metal's temperature. The type of sand used can vary, but it usually consists of silica sand due to its high melting point and excellent thermal stability. The binding agents can include various compounds such as phenolic resins or other thermosetting polymers that help in forming a robust mold.
lost foam casting coating
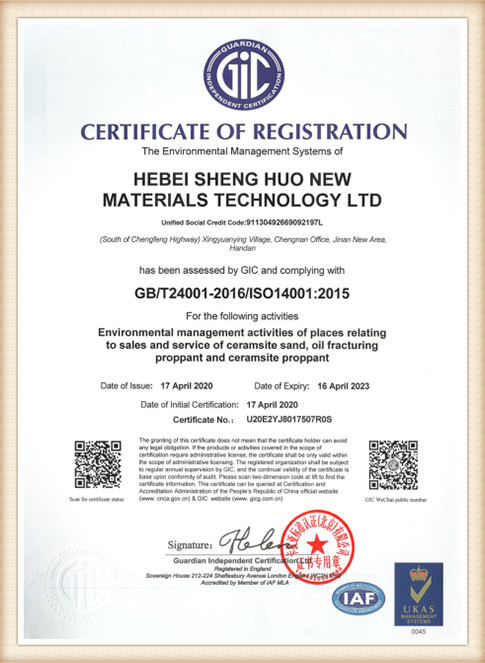
One significant advantage of using coatings in lost foam casting is the reduction of material waste and increased overall yield. Because the foam pattern is consumed in the process, the precision provided by the coating allows manufacturers to achieve tighter tolerances, thereby reducing the need for excessive machining after casting. This translates into cost savings and shorter lead times for production, making lost foam casting an attractive option for industries requiring intricate designs and rapid turnaround.
Moreover, advancements in coating technology have further enhanced the capabilities of the lost foam casting process. Engineers and manufacturers continually experiment with different materials and methods to improve the coating's performance. For example, the application of advanced ceramic coatings can provide superior resistance to thermal shock and increased durability during the casting process. These innovative approaches not only improve the quality of the final product but also expand the range of materials that can be effectively used in lost foam casting.
It is also important to consider environmental aspects of lost foam casting coatings. With increasing regulations regarding emissions and hazardous materials, many manufacturers are now focused on developing eco-friendly coatings. Water-based binders are being explored as alternatives to traditional solvent-based systems, reducing the environmental impact of the casting process. These efforts align with global sustainability goals and emphasize the importance of responsible manufacturing practices.
In conclusion, the role of coating in lost foam casting cannot be overstated. It significantly influences the quality, precision, and efficiency of the casting process. With ongoing research and advancements in coating materials and techniques, the lost foam casting method is poised to improve even further, offering manufacturers enhanced capabilities and more sustainable options. As industries continue to embrace innovative manufacturing processes, the importance of effective coatings in lost foam casting will only grow, making it a vital area of focus for engineers and production specialists alike. Whether for automotive, aerospace, or other applications, the evolution of lost foam casting coatings will undoubtedly play a key role in shaping the future of efficient and precise manufacturing.
Post time:Nov . 19, 2024 17:33
Next:what is sand casting used for