Is Sand Casting Sustainable?
Sand casting, a manufacturing process where molten metal is poured into a mold made from sand, has been a staple in the foundry industry for centuries. It is widely used for producing complex metal parts and components because of its versatility, cost-effectiveness, and ability to produce large quantities. However, in recent years, the sustainability of sand casting has come under scrutiny as industries seek to minimize their environmental impact. This article explores the sustainability of sand casting from various perspectives, including its material usage, energy consumption, and potential for waste reduction.
Material Usage
One of the most significant aspects of sustainability in any manufacturing process is the materials involved. Sand casting primarily uses silica sand, which is abundant and naturally occurring. The clay and other additives required to bind the sand are also readily available. As such, the raw materials used in sand casting have a lower environmental impact compared to processes that require rare or synthetic materials.
Moreover, sand used in casting can often be recycled. Once a casting is complete, the sand can be reused to create new molds, reducing the amount of new sand needed and minimizing waste in the process. Many foundries implement systems to reclaim sand, which not only conserves resources but also lowers operational costs. This recycling capability is a significant advantage when evaluating the sustainability of sand casting.
Energy Consumption
Energy consumption is another critical factor for assessing the sustainability of any manufacturing process. Sand casting does require substantial energy, particularly in melting the metals involved, which typically requires furnaces that consume fossil fuels or electricity. However, the energy efficiency of sand casting can be improved through technological advancements.
Some foundries are adopting electric arc furnaces powered by renewable energy sources, significantly reducing their carbon footprint. Additionally, advanced monitoring and control technologies can optimize the melting process, reducing energy waste. While sand casting may not be as energy-efficient as some modern manufacturing methods, ongoing improvements are being made to decrease its environmental impact.
is sand casting sustainable
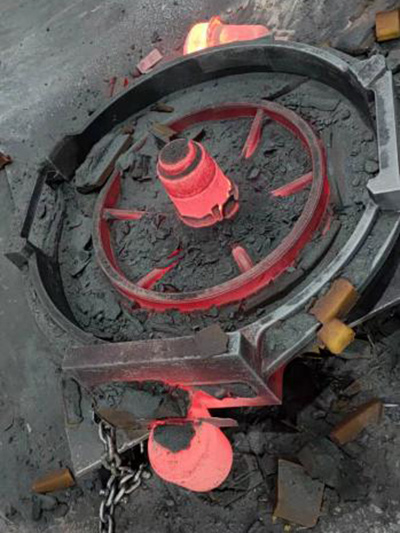
Waste Production
Manufacturing processes inherently generate waste, and sand casting is no exception. However, assessing the types of waste produced is essential for understanding the sustainability of the process. Common waste materials from sand casting include defective castings, sand that cannot be recycled, and used molding materials.
Efforts are being made to minimize these waste products by improving the design and planning stages of casting projects. Advanced simulation technologies and computer-aided design (CAD) software can help manufacturers identify potential issues before production, reducing the likelihood of defects. Additionally, innovative methods such as additive manufacturing (3D printing) of sand molds are being explored to minimize waste and enhance design flexibility.
Environmental Impact and Future Prospects
While sand casting may not be the most environmentally friendly manufacturing process, it does offer several advantages that contribute to its sustainability. The ability to recycle materials, coupled with innovations to reduce energy consumption and waste production, positions sand casting as a process that can adapt to modern sustainability demands.
Furthermore, companies are increasingly held accountable for their environmental performance. As regulatory frameworks evolve and consumers demand more sustainable products, manufacturers are likely to prioritize sustainability initiatives in their operations. This shift can drive further improvements in sand casting technologies, making the process more eco-friendly and economically viable.
Conclusion
In conclusion, sand casting possesses inherent qualities that can align with sustainable practices, despite some challenges regarding energy use and waste generation. With an emphasis on material recycling, energy efficiency improvements, and waste reduction, sand casting can evolve to meet the sustainability demands of today's industrial landscape. As foundries continue exploring and investing in innovative technologies, the future of sand casting seems poised to embrace a more sustainable path, ensuring its relevance in a world increasingly focused on reducing environmental impact.
Post time:Oct . 14, 2024 11:49
Next:sanding 3d resin prints