Is Sand Casting Expensive?
Sand casting is one of the oldest and most widely used metal casting processes in manufacturing today. The technique involves creating a mold from sand and then pouring molten metal into that mold to create a desired shape. While sand casting is known for its versatility and ability to produce complex shapes, many potential users often wonder if it is an expensive process.
Cost Factors in Sand Casting
The cost associated with sand casting can depend on various factors, including the complexity of the part, the type of metal used, and the scale of the production run. Generally, sand casting has lower initial tooling costs compared to other casting methods such as investment casting or die casting. This makes it an attractive option for small to medium production runs or prototyping.
1. Tooling Costs Creating a sand mold requires a pattern, which can be made of wood, metal, or other materials. The cost of creating this pattern is a significant upfront investment. However, since patterns can be reused for multiple casts, this initial cost can be amortized over a larger number of units.
2. Material Costs The type of metal chosen for the casting also plays a crucial role in overall expenses. Common casting metals like aluminum, iron, and bronze vary in price. While aluminum is relatively inexpensive, specialty alloys can significantly increase material costs.
is sand casting expensive
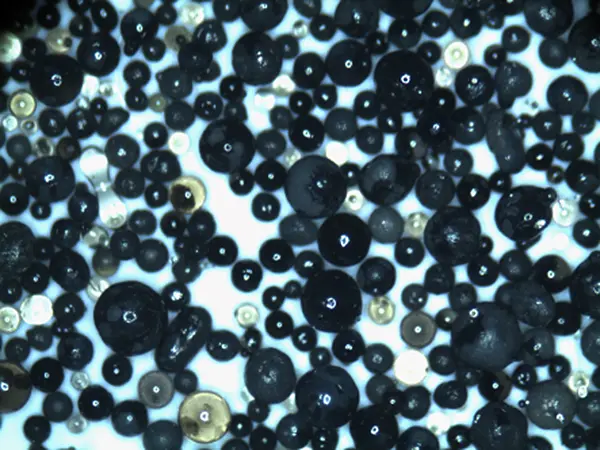
3. Labor Costs Labor costs can also affect the overall expense of sand casting. Skilled workers are required to manage the pouring process and ensure quality control, which can contribute to higher operational costs, especially in regions where labor rates are elevated.
4. Production Scale The volume of production greatly influences the per-unit cost. For larger production runs, the cost per unit decreases because the initial setup costs are spread over more units. Conversely, for small batches, these costs can be more pronounced.
Advantages of Sand Casting
Despite some of the inherent costs, sand casting offers several advantages that can offset these expenses. For example, the ability to create intricate designs without the need for expensive tooling changes makes sand casting particularly beneficial for prototypes. Additionally, it is a very adaptable process. Manufacturers can easily modify designs between runs without incurring high costs, which is a significant benefit in industries that require frequent updates to designs.
Conclusion
In conclusion, whether sand casting is considered expensive depends on various factors such as volume, design complexity, and material choice. While there may be initial costs associated with tooling and labor, the long-term benefits and flexibility offered by sand casting often make it a cost-effective solution for many manufacturing needs. For businesses looking for a reliable casting method that balances cost and quality, sand casting remains a strong contender in the metallurgy landscape.
Post time:Oct . 31, 2024 14:44
Next:Resin-Coated Silica Sand for Enhanced Performance in Construction and Industrial Applications