Iron Sand Casting A Comprehensive Overview
Iron sand casting is an integral process in the metalworking industry, harnessing the unique properties of iron sand to produce high-quality castings. This method has gained popularity due to its efficiency, cost-effectiveness, and the ability to create complex shapes that are often difficult to achieve with traditional methods.
What is Iron Sand Casting?
Iron sand casting involves the use of iron-rich sand as a primary material for creating molds. This type of sand consists primarily of magnetite, a naturally occurring iron oxide. The sand is mixed with a binding agent, typically clay, to ensure that it holds its shape during the casting process. The mixture is then shaped into molds that define the desired dimensions of the final product. Once the molds are prepared, molten iron is poured into the cavities to create the final casting.
The Process
The iron sand casting process begins with the preparation of the sand mixture. The iron sand is cleaned and graded to remove impurities and achieve the appropriate granule size for optimal mold creation. The mixture of iron sand and the binding agent is then compacted to form molds.
Once the molds are ready, molten iron is generated through a melting process, typically in a furnace. The temperature is carefully controlled to ensure that the iron is adequately liquefied. The molten iron is poured into the prepared molds, where it solidifies into the desired shapes as it cools. After the metal has cooled sufficiently, the molds are broken apart to reveal the castings. The final steps typically include cleaning, finishing, and inspecting the castings to ensure they meet quality standards.
Advantages of Iron Sand Casting
iron sand casting
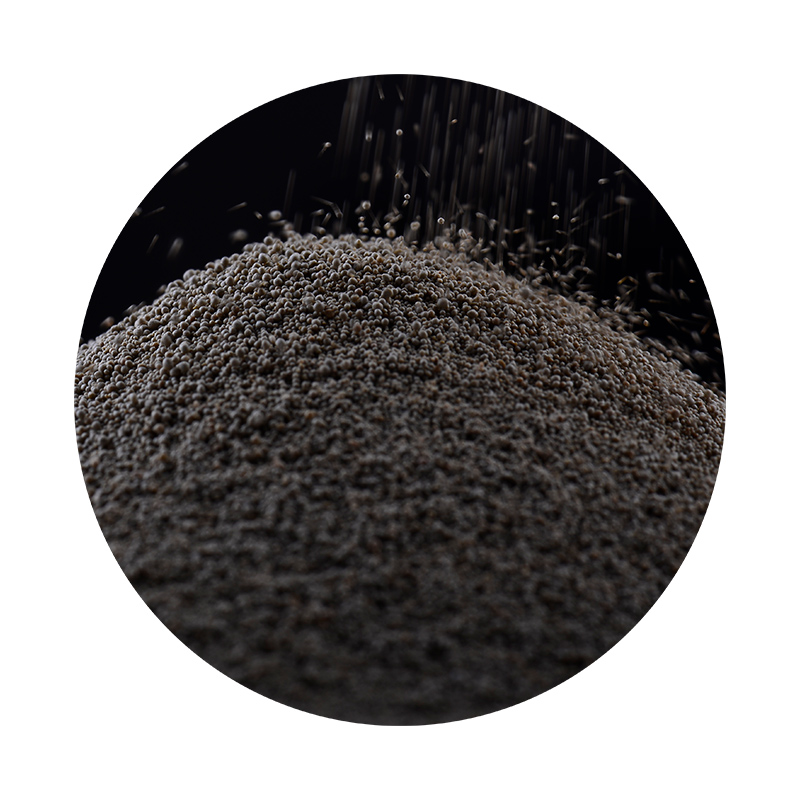
One of the primary advantages of iron sand casting is its ability to produce intricate designs with relative ease. The flexibility of the sand molds allows for detailed patterns and complex geometries, which can be crucial for many applications, including automotive parts, machinery components, and artistic sculptures.
Additionally, iron sand casting is a sustainable process. The use of local iron sand resources reduces dependence on imported metals, while the recycling of cast materials contributes to environmental sustainability. Iron sand casting is also cost-effective, often requiring less energy than other metal casting methods, leading to lower production costs.
Another significant advantage is the excellent mechanical properties of iron castings. Components produced through this method often exhibit high strength, durability, and resistance to wear, making them suitable for demanding applications.
Applications
Iron sand castings find applications across various industries, including aerospace, automotive, heavy machinery, and construction. The components produced can range from small fittings to large structural elements. The versatility of the process allows manufacturers to serve a diverse array of market needs.
Conclusion
Iron sand casting stands out as a reliable and versatile method in the foundry industry. Its combination of efficiency, cost-effectiveness, and the ability to produce detailed and durable castings has made it a preferred choice for many manufacturers. As industries continue to innovate and evolve, the significance of iron sand casting is likely to grow, cementing its place as a vital technique in modern metalworking. Whether for practical applications or artistic endeavors, iron sand casting remains a fascinating and essential process in the art of manufacturing.
Post time:Nov . 25, 2024 03:34
Next:Innovative Techniques in Steel Sand Casting for Enhanced Quality and Efficiency