How to Sand Cast A Beginner's Guide
Sand casting, also known as sand mold casting, is a versatile and widely used metal casting process that involves the use of sand to create molds. This age-old technique allows for the production of intricate metal parts, and it is particularly favored for its cost-effectiveness and ability to produce complex shapes. In this article, we will explore the basic steps of sand casting and provide essential tips for beginners.
Understanding the Basics of Sand Casting
Before diving into the process, it's important to understand the key components involved in sand casting. The primary materials include
1. Sand The main material used to create molds, typically a mixture of silica sand and clay. 2. Binder A substance that helps hold the sand together, usually clay or a synthetic binder. 3. Metal The material to be cast, which can include aluminum, bronze, iron, or other metals. 4. Pattern A replica of the item you wish to create; it is made from materials like wood or metal.
Step 1 Creating the Pattern
The first step in sand casting is creating a pattern that represents the final product. Patterns are often made from wood or metal and should be slightly larger than the final casting to accommodate for shrinkage during cooling. The design should also include any necessary features, such as draft angles and parting lines, to facilitate easy removal from the mold.
Step 2 Preparing the Sand Mold
Once the pattern is ready, the next step is to create the mold. This involves packing sand around the pattern to form a mold cavity. Here are the sub-steps to follow
1. Mixing the Sand Combine the sand with an appropriate binder to ensure that it holds its shape when packed. The typical mix consists of about 90% sand to 10% clay. 2. Creating the Molding Box Place the pattern in a molding box, securing it in place.
3. Packing the Sand Carefully pack the sand mixture around the pattern, pressing firmly to create an accurate impression. It is essential to eliminate any air pockets that could compromise the mold's integrity.
4. Forming the Mold Cavity After the pattern is covered, remove it gently to leave behind a mold cavity.
Step 3 Pouring the Metal
how to sand cast
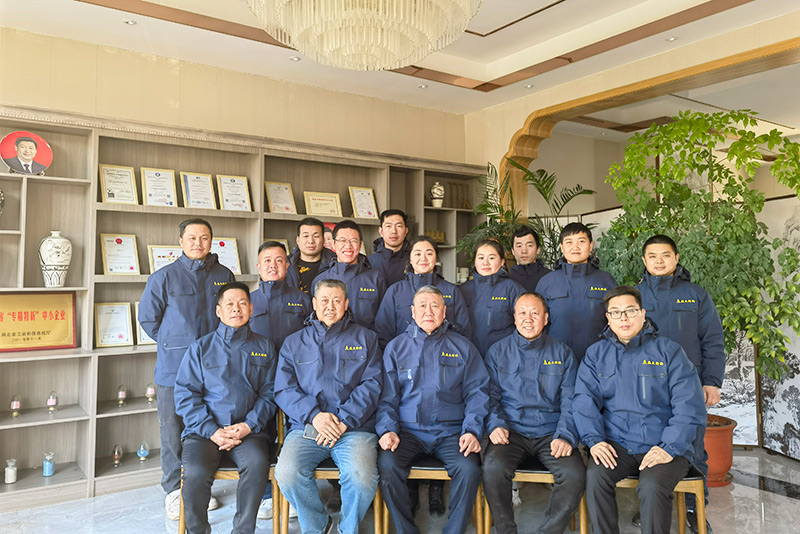
Now that you have your mold, it's time to pour in the molten metal. This step requires careful attention to safety
1. Melting the Metal Use a furnace to melt the desired metal until it reaches a liquid state. Always use suitable safety gear, including gloves and protective eyewear.
2. Pouring Pour the molten metal into the mold cavity slowly, avoiding spills and splashes.
3. Cooling Allow the metal to cool and solidify, which can take several minutes to hours depending on the size of the cast.
Step 4 Finishing the Cast
Once the metal has cooled and solidified, the final step is to remove the sand mold and finish the cast piece
1. Breaking the Mold Carefully break apart the sand mold to free the cast metal component.
2. Cleaning the Cast Remove any excess sand and inspect the cast for any imperfections. This may involve sanding or grinding to achieve a smooth finish.
3. Final Touches Depending on the intended use, you may need to further process the cast by drilling holes or adding surface finishes.
Tips for Success
- Experiment with Patterns Try different materials for patterns to see what produces the best results. - Control the Environment Work in a dry area since moisture can adversely affect the sand mixture. - Use Proper Safety Gear Always prioritize safety when handling molten metal. - Practice As with any craft, practice is key to mastering sand casting. Don't be discouraged by initial failures; learn from them.
Conclusion
Sand casting is an accessible and rewarding technique that can yield beautiful and functional metal pieces. Whether you are a hobbyist or aspiring metalworker, understanding the basics of sand casting sets the foundation for creating unique designs. With practice, patience, and attention to detail, you can refine your skills and produce quality castings that reflect your creativity and craftsmanship.
Post time:Dec . 13, 2024 20:12
Next:Understanding Tolerances in Sand Casting Processes for Enhanced Precision and Quality