Understanding Foundry Casting Sand An Essential Component in Metal Casting
Foundry casting sand plays a pivotal role in the metal casting industry, serving as one of the core materials used to create molds for various metal products. This versatile medium is crucial for the successful execution of the casting process, providing the necessary properties and characteristics that enable manufacturers to produce high-quality components effectively and efficiently.
The Composition and Types of Foundry Sand
Foundry sand is primarily composed of silica, which is a high-purity form of silica sand that possesses excellent thermal properties. This quality allows it to withstand the high temperatures generated during the metal casting process. However, not all foundry sands are created equal. Different types of foundry sands are employed, each with specific properties tailored for distinct applications.
One of the most common types is green sand, a mixture of silica, clay, and moisture that is compactable and reusable. It is renowned for its mold-making ability and provides a better surface finish compared to other types. Another popular option is resin-coated sand, which has been treated with resin bonding agents. This type boasts superior dimensional accuracy and is often used for producing intricate designs. Other specialties include olivine sand, which is more costly but provides excellent thermal conductivity and less mold gas emissions.
The Importance of Sand Quality
The quality of the foundry sand used directly influences the success of the casting process. Key factors such as grain size, shape, and distribution play critical roles in determining how well the sand can form molds and how it behaves under extreme heat. Fine grains tend to have better moldability but can lead to casting defects if used excessively. Conversely, coarser sands are less prone to defects but may not capture fine details as effectively. Therefore, finding the right balance in sand characteristics is crucial.
Environmental Considerations
foundry casting sand
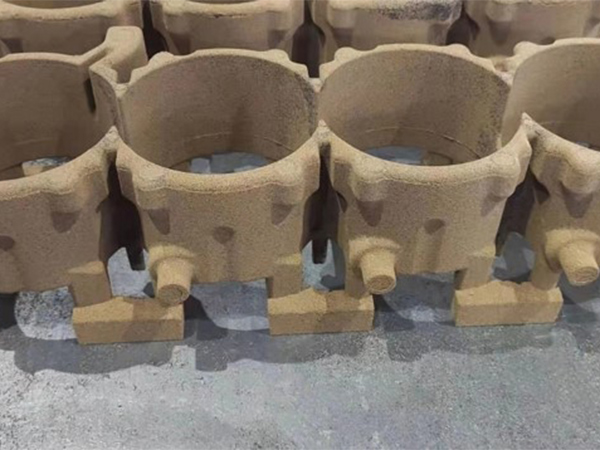
The foundry industry faces increasing scrutiny regarding environmental impact. Traditional sand casting methods often result in significant waste, primarily due to sand being discarded after a single use. This issue has spurred the development of sustainable practices within foundries. For instance, many facilities now emphasize sand reclamation techniques that allow for the recycling and reconditioning of spent sand, thus reducing landfill waste and conserving resources.
Moreover, advancements in synthetic sands have been developed to enhance the environmental performance of the foundry casting process. These materials are engineered to offer specific mechanical and thermal properties while also minimizing environmental concerns related to silica dust and waste management.
Applications of Foundry Casting Sand
Foundry casting sand is an integral component across various industries. The automotive sector relies on it extensively for producing engine blocks, transmission cases, and other critical components. Similarly, the aerospace industry utilizes casting sand for manufacturing parts that require high precision and durability, such as turbine blades and structural components.
The construction and tooling industries also benefit from foundry sand applications, where patterns and molds for concrete products and metal components are created. As demand for both production efficiency and product quality rises, the significance of foundry casting sand in meeting these industry needs continues to grow.
Conclusion
In conclusion, foundry casting sand is more than just a medium for mold-making; it is an essential component that directly affects the efficiency, quality, and environmental sustainability of metal casting processes. As the industry evolves, innovations in sand types and recycling methods demonstrate the growing awareness of both performance and ecological impact. As manufacturers strive to enhance their casting capabilities, foundry casting sand will undoubtedly remain at the forefront of these developments, helping to shape the future of metal casting. Whether it’s automotive parts or aerospace components, the role of foundry casting sand in producing reliable and high-quality products cannot be overstated.
Post time:Dec . 31, 2024 05:00
Next:Exploring Innovative Uses of 3D Printing with Sand-Based Materials and Techniques