Custom Sand Casting A Key to Precise Manufacturing
Custom sand casting is a manufacturing process that has been employed for centuries, yet remains one of the most versatile methods for producing intricate metal parts and components. This technique involves creating a mold from sand, then pouring molten metal into that mold to form a desired shape. Its adaptability makes it applicable across various industries, including automotive, aerospace, and art.
One of the primary advantages of custom sand casting is its ability to produce complex shapes that would be challenging or impossible to achieve through other manufacturing processes. The sand used in this method can easily be shaped and packed into molds with fine details, allowing for high levels of precision in the final product. This is particularly valuable in industries where intricate designs and reliable functionality are paramount.
The custom aspect of sand casting sets it apart from traditional methods. Manufacturers can collaborate closely with clients to design tailored molds that meet specific specifications. This flexibility enables businesses to create unique components optimized for their particular applications. The process can accommodate various metals, including aluminum, iron, and bronze, making it suitable for a wide range of projects.
In the initial stage of custom sand casting, a pattern is created, which replicates the final product. This pattern is typically made from materials such as wood or metal and is used to form the sand mold. The sand itself is mixed with a binding agent, such as clay or resin, to enhance cohesion. Once the mold is prepared, it is subjected to heat and pressure to ensure durability.
custom sand casting
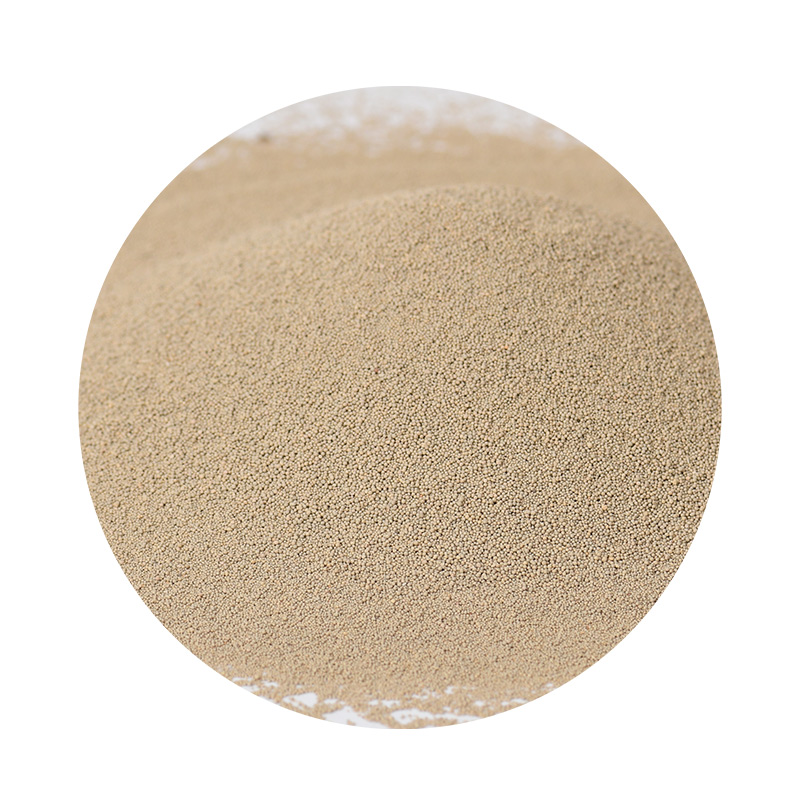
After constructing the mold, the molten metal is poured into the cavity created by the pattern. The cooling process is crucial, as it allows the metal to solidify and take on the shape of the mold. Once cooled, the sand mold is broken away, revealing the cast part. This entire procedure can be relatively quick, especially when compared to other manufacturing methods, allowing for faster production cycles and reduced lead times.
Despite its many advantages, custom sand casting does have limitations. Surface finish and dimensional accuracy may not be as high as with other methods like injection molding. However, these issues can often be mitigated through post-processing techniques such as machining or finishing.
The environmental impact of sand casting has gained attention in recent years. Efforts to utilize sustainable practices, like recycling sand and reducing waste, have become more prevalent as the industry adapts to modern eco-conscious demands. Additionally, the process often requires less energy compared to other metal forming techniques, further enhancing its sustainability credentials.
As industries continue to innovate and expand, the demand for custom sand casting is likely to grow. Its unique ability to create tailor-made solutions for metal parts ensures that it remains a cornerstone of manufacturing. By leveraging the benefits of this traditional method while embracing advancements in technology and sustainability, manufacturers can meet the evolving needs of their clients and contribute to a more efficient future.
In conclusion, custom sand casting stands out as a time-honored but ever-relevant manufacturing process. Its capabilities for creating unique, complex metal components, coupled with its adaptability, make it an essential option for many industries today. As sustainability becomes increasingly important, the evolution of sand casting will likely play a key role in the future landscape of manufacturing.
Post time:Nov . 05, 2024 19:12
Next:golden sanda