Types of Sand in Foundry An Overview
Sand is a foundational material in the casting process of metallurgical foundries. It acts as a mold material that defines the shape of the final castings. The choice of sand can significantly influence the quality of the final product, the efficiency of the casting process, and the overall cost-effectiveness of production. There are various types of foundry sands, each with unique properties that cater to different casting requirements.
1. Silica Sand
Silica sand is the most commonly used sand in foundries due to its excellent properties such as high melting point, good thermal stability, and availability. It consists primarily of silicon dioxide (SiO2) and provides a low cost solution for most casting needs. Silica sand is suitable for ferrous and non-ferrous metal casting and can withstand high temperatures, making it ideal for both green sand and resin-bonded processes. However, the shape and size of the sand grains can significantly impact the surface finish and dimensional accuracy of castings.
2. Chromite Sand
Chromite sand is derived from chromite ore and offers unique benefits in the casting process. It has a high melting point and low thermal expansion, making it particularly useful for steel casting and high-performance applications. The sand's resistance to metal penetration and its ability to maintain a stable shape under high temperatures makes it an excellent choice for producing molds and cores that require enhanced dimensional accuracy and surface finish.
3. Zircon Sand
types of sand in foundry
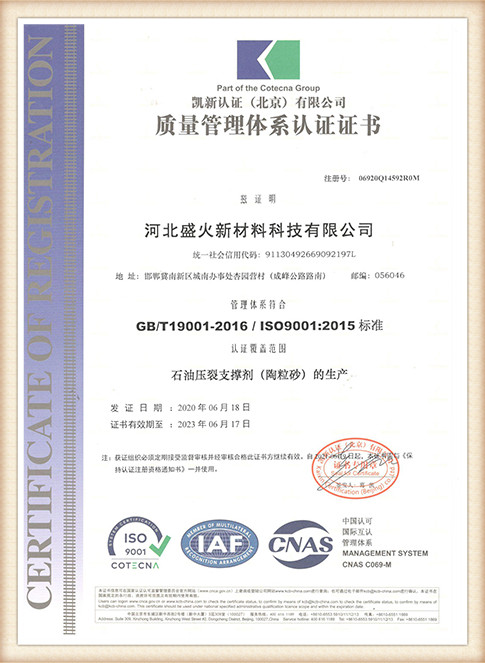
Zircon sand is another high-performance foundry sand, known for its high melting point and low thermal expansion. It is often used in the production of high-quality castings that require exceptional strength and thermal stability. Zircon sand helps achieve a superior surface finish and is resistant to wear and deformation, making it a preferred choice for investment castings and applications involving high-temperature alloys.
4. Olivine Sand
Olivine sand is composed of magnesium iron silicate and is recognized for its ability to withstand high temperatures and its low expansion rate. This type of sand is particularly useful in steel foundries and for applications where thermal stability is crucial. Olivine sand offers good flowability, which aids in creating intricate mold shapes. Its resistance to metal infiltration makes it suitable for producing high-quality castings.
5. Green Sand
Green sand is a mixture of silica sand, clay, water, and additives. It is widely used in the foundry industry due to its reusability, cost-effectiveness, and ease of preparation. Green sand molding allows for quick turnarounds and is compatible with both ferrous and non-ferrous metals. However, its quality can vary based on the type and amount of clay used, which can influence the mechanical properties of the final castings.
Conclusion
Selecting the right type of sand for foundry applications is essential for achieving desired casting qualities. Each type of sand—silica, chromite, zircon, olivine, and green sand—offers specific advantages that can be leveraged depending on the casting requirements. Understanding the properties and applications of these sands not only enhances production efficiency but also contributes to the overall quality and performance of the cast products. As the foundry industry continues to evolve, innovative sand formulations and processing techniques are likely to emerge, paving the way for enhanced casting technologies.
Post time:ต.ค. . 31, 2024 16:01
Next:The Process and Benefits of Iron Sand Casting in Modern Manufacturing