An Overview of Steel Sand Casting
Steel sand casting is a prevalent manufacturing process utilized in various industries to produce intricate components and products. This procedure, characterized by its versatility and cost-effectiveness, involves casting molten steel into a sand mold that holds the desired shape of the final product. This article will provide an in-depth exploration of the steel sand casting process, its advantages, applications, and recent innovations in the field.
The Casting Process
The steel sand casting process begins with the creation of a mold. A pattern, typically made of metal or plastic, is crafted to represent the final product. This pattern is placed in a box filled with a mixture of sand and a binding agent, typically clay or resin. The sand is compacted around the pattern to form a mold. Once the pattern is removed, the mold cavity remains, ready for molten steel.
Molten steel, heated to temperatures exceeding 1,500 degrees Celsius, is then poured into the mold cavity. As the steel fills the mold, it takes on the shape of the cavity. After sufficient cooling time, the solidified casting is removed from the sand mold, often requiring some finishing processes such as grinding or machining to achieve the desired surface finish and dimensional accuracy.
Advantages of Steel Sand Casting
One of the primary advantages of steel sand casting is its ability to create complex geometries that are often challenging to achieve with other manufacturing methods. The flexibility of sand allows for the production of intricate designs with varied wall thicknesses, which is critical in industries such as automotive, aerospace, and machinery.
Additionally, steel sand casting is highly cost-effective for low to mid-volume production runs. The materials used in sand casting, particularly the sand itself, are relatively inexpensive and readily available. Furthermore, the sand molds can be reused multiple times, making the process economically viable over a series of production cycles.
Another key benefit of steel sand casting is its excellent material properties
. Steel castings exhibit enhanced strength, durability, and resistance to wear and tear, which are essential for components subjected to harsh operating conditions.steel sand casting
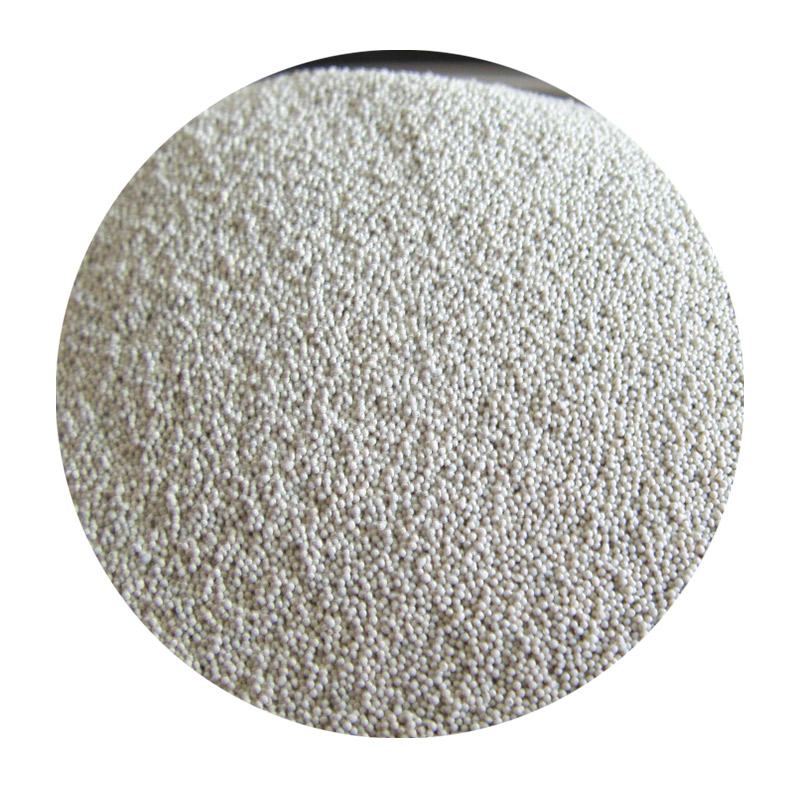
Applications
Steel sand casting finds its application across a wide range of industries. In the automotive sector, components such as engine blocks, transmission housings, and suspension parts are commonly produced using this technique. In the aerospace industry, cast steel parts are utilized for their strength-to-weight ratios in critical components.
Additionally, machinery and equipment manufacturers also rely on steel sand casting for producing gears, brackets, and other structural components that require a high level of resilience and performance.
Innovations in Steel Sand Casting
Recent technological advancements have significantly enhanced the steel sand casting process. Innovations such as 3D printing have been integrated into mold production, allowing for more efficient and precise mold creation. This technology enables the rapid prototyping of complex designs, facilitating quicker turnaround times for production.
Furthermore, advancements in computer-aided design (CAD) and simulation software have improved the ability to predict how molten steel behaves during casting. These tools allow engineers and designers to identify potential defects and optimize designs before the actual casting begins, reducing waste and improving quality.
Conclusion
In summary, steel sand casting is a critical manufacturing process that combines versatility, cost-effectiveness, and material strength to produce high-quality components across various industries. With ongoing innovations driving advancements in the process, steel sand casting will continue to play a significant role in the future of manufacturing, meeting the demands of evolving technologies and increasingly complex product designs. As industries seek efficient production methods while maintaining high standards, steel sand casting stands out as an enduring solution in the manufacturing landscape.
Post time:ธ.ค. . 26, 2024 02:33
Next:sand and polish resin