Sanding Glazed Ceramics A Comprehensive Guide
Ceramics have long been celebrated for their beauty and functionality, offering a wide range of artistic and practical applications. Glazed ceramics, in particular, stand out due to their glossy finish, vibrant colors, and chemical resistance. However, there may come a time when even the most stunning glazed piece needs a little rejuvenation or modification. This is where the technique of sanding comes into play. In this article, we will delve into the process of sanding glazed ceramics, discussing its purposes, methods, and safety considerations.
The Purpose of Sanding Glazed Ceramics
Sanding glazed ceramics can serve multiple purposes, including
1. Surface Repair Over time, ceramic pieces can suffer from chips, scratches, or dullness. Sanding helps in smoothing out these imperfections, restoring the piece’s aesthetic appeal.
2. Preparation for Re-glazing If an artist wishes to change the glaze or apply a new finish, sanding is essential. The existing glaze needs to be roughed up to enable proper adhesion of the new layers.
3. Creating Texture Some artists intentionally sand specific areas of a glazed piece to achieve a unique texture, creating a contrast between glossy and matte finishes.
4. Improving Fit For functional ceramics, such as tiles or pottery lids, sanding can help achieve a better fit by removing excess glaze.
Materials Needed
Before starting the sanding process, you’ll need to gather a few essential tools and materials
- Sandpaper Choose medium to fine-grit sandpaper (around 150-400 grit) based on the level of finish you desire. Start with lower grit and progressively move to higher grit for a smoother finish.
- Sanding Sponge These are great for contoured surfaces where traditional sandpaper might be too rigid.
- Damp Cloth To wipe away dust and debris after sanding
.- Safety Gear Goggles and a mask are essential to protect yourself from dust particles.
sanding glazed ceramics
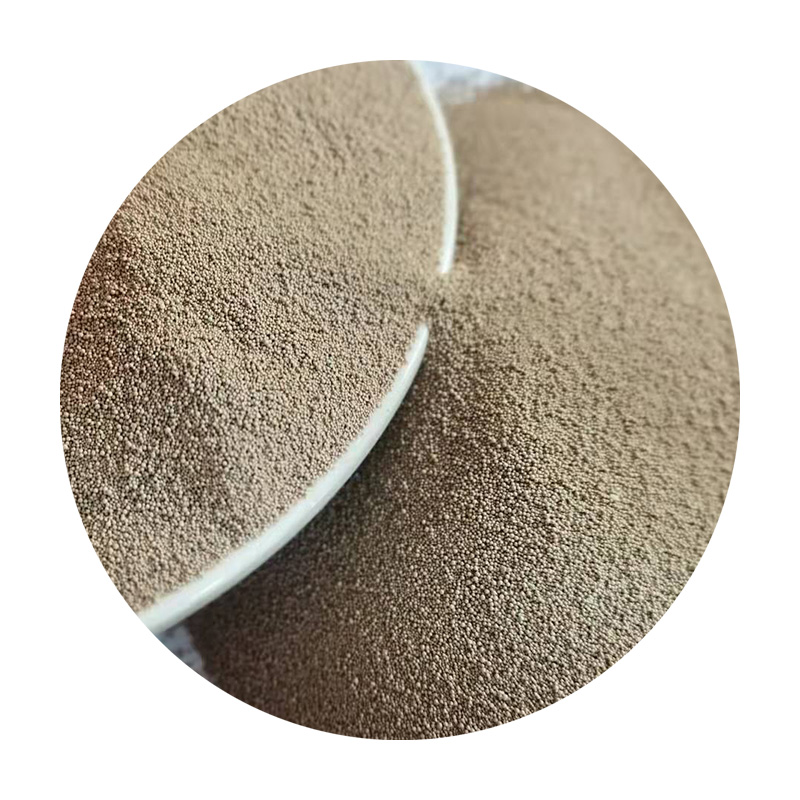
The Sanding Process
Here’s a step-by-step guide to sanding glazed ceramics
1. Clean the Surface Before sanding, make sure the ceramic piece is clean and free from any debris or dust. Use a damp cloth to wipe it down.
2. Assess the Damage Identify the areas that need sanding. If you’re repairing chips or scratches, focus on those areas.
3. Choose the Right Grit Start with medium-grit sandpaper for more substantial repairs. If you're just smoothing out minor imperfections or preparing for re-glazing, you can begin with fine-grit sandpaper.
4. Sanding Technique Gently rub the sandpaper in a circular motion or back-and-forth along the surface. Avoid applying too much pressure, as this can lead to further damage.
5. Check Progress Periodically wipe the area with a damp cloth to remove dust and assess your progress.
6. Finishing Touches Once the surface is smooth, switch to finer grit sandpaper for a polished finish. Sand lightly to avoid removing too much glaze.
7. Clean After Sanding After you are satisfied with the sanding, wipe down the entire piece with a damp cloth to remove any remaining dust particles before re-glazing or using the item.
Safety Considerations
While sanding is relatively straightforward, it’s vital to prioritize safety. Make sure to
- Work in a well-ventilated area to avoid inhaling dust. - Wear protective goggles to shield your eyes from flying particles. - Use a mask to prevent inhaling harmful dust, especially if the ceramic contains lead-based glazes.
Conclusion
Sanding glazed ceramics is an invaluable technique for artists and enthusiasts alike. Whether aiming to restore beauty, prepare for a new glaze, or enhance texture, understanding the right approach ensures that your ceramic pieces remain both functional and aesthetically pleasing. As with any craft, patience and practice will lead to success. So, gather your materials, put on your safety gear, and embrace the transformative journey of sanding glazed ceramics. With attention to detail and care, your ceramic pieces will shine bright once again.
Post time:พ.ย. . 12, 2024 13:42
Next:sand castings