Understanding the Sand Casting Process A Comprehensive Overview
Sand casting, often referred to as sand mold casting, is one of the oldest and most versatile metal casting processes used in various industries today. It involves creating a mold from sand and using it to shape molten metal into desired objects. This technique has endured through centuries of evolution due to its simplicity, cost-effectiveness, and adaptability to a wide range of metals.
The Basics of Sand Casting
The sand casting process begins with the preparation of a pattern, which is a replica of the object to be cast. Patterns can be made from various materials, including wood, metal, or plastic, and are crafted to approximate the final dimensions of the desired product. The pattern is typically designed to be slightly larger than the final piece to account for metal shrinkage during cooling.
Once the pattern is ready, it is placed in a mixture of sand and a bonding agent, typically clay. This mixture is packed around the pattern to form a mold. The sand is usually coarse and can resist high temperatures, making it suitable for casting a variety of metals including aluminum, iron, and bronze. After the sand is compacted around the pattern, the mold is opened, and the pattern is removed, leaving a cavity that reflects the shape of the desired part.
Mold Creation
The mold construction process can vary depending on the design's complexity. The simplest method involves creating two halves of a mold, known as a cope (top half) and a drag (bottom half). Together they form a complete mold cavity. For complicated designs, additional cores made of sand may be required to create internal features or hollow sections in the final cast.
Once the mold is finalized, various features such as runners, risers, and gates are added. Runners provide a pathway for the molten metal to flow into the mold, while risers act as reservoirs to compensate for shrinkage. Gates are points where the molten metal enters the mold, and their design plays a critical role in controlling flow and preventing defects.
Melting and Pouring
sand casting processes
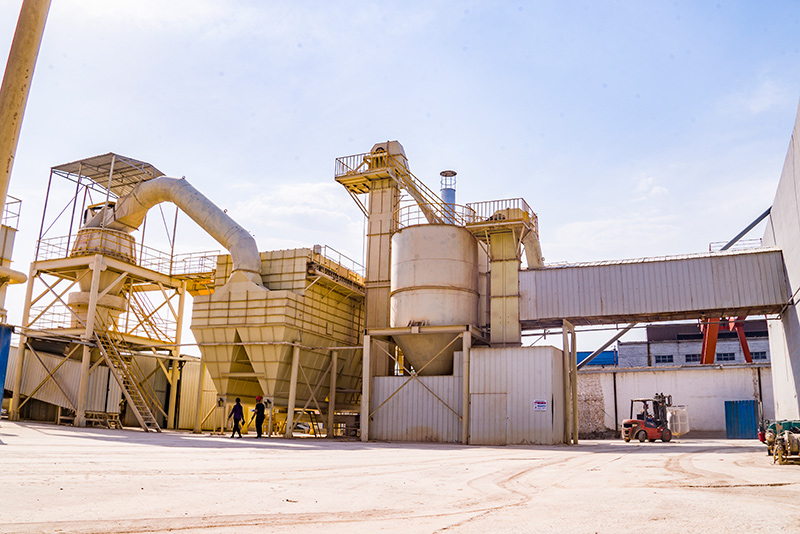
After the mold is prepared, the next step in the sand casting process is melting the metal. This is typically conducted in furnaces that can reach extremely high temperatures sufficient to melt various types of metals such as cast iron or aluminum. Once the metal has reached its melting point, it is poured into the mold cavity through the gates.
One of the advantages of sand casting is its ability to accommodate large metal pours, making it suitable for both small and large scale production runs. The metal is left to cool and solidify, forming a solid object that matches the mold's shape and dimensions.
Cooling and Finishing
After pouring, the cooling phase is crucial. The cooling time can vary depending on the thickness of the casting and the metal used. Once the metal has cooled and solidified, the mold is broken apart to reveal the raw cast part. This part typically requires additional finishing processes, which may include grinding, machining, or surface treatment to achieve the desired final specifications.
Advantages and Applications
Sand casting offers numerous advantages, including low production costs, the ability to work with a wide variety of alloys, and the flexibility to produce intricate shapes. These benefits make it a favored choice in various industries such as automotive, aerospace, and heavy machinery.
Despite the advent of modern casting techniques, sand casting remains highly relevant. Its enduring presence in industrial applications can be attributed to its ability to produce high-quality castings in diverse shapes and sizes, making it an invaluable process in the manufacturing landscape.
In conclusion, sand casting is a time-tested process that continues to play a significant role in metal fabrication. Its simplicity, versatility, and cost-effectiveness contribute to its continued popularity and relevance in various industrial applications. Understanding the sand casting process not only highlights the ingenuity of this age-old technique but also sheds light on its critical role in producing essential components across a wide range of sectors.
Post time:พ.ย. . 10, 2024 15:21
Next:3D Printing with Sand for Creative and Innovative Designs in Construction