Understanding Sand Casting Foundries A Comprehensive Overview
Sand casting is one of the oldest and most versatile metalworking processes used to create intricate and diverse shapes. This technique involves the creation of a mold from sand to cast molten metal, making it an essential method in various industries, from automotive to aerospace. In this article, we will explore the key aspects of sand casting foundries, including their processes, advantages, challenges, and applications.
The Sand Casting Process
The sand casting process consists of several steps. First, a pattern, usually made of metal or plastic, is created in the shape of the desired final product. The pattern is then placed in a mold box, which is filled with mixed sand and a binding agent. This mixture is compacted around the pattern to form a mold.
Once the mold is created, the pattern is removed, leaving a cavity in the sand that corresponds to the desired shape. The two halves of the mold are then assembled, and molten metal is poured into the cavity. After the metal has cooled and solidified, the sand mold is broken away to reveal the finished cast item. This process can produce complex shapes and is particularly suited for low to medium volume production.
Types of Sand Used in Casting
Silica sand is the most commonly used material for sand casting due to its availability and thermal properties. However, other types of sands, such as zircon sand and olivine, may be used for specific applications where different thermal properties or lower casting defects are desired. The choice of sand and its composition can greatly affect the final quality of the cast product.
Advantages of Sand Casting
Sand casting foundries possess several advantages that make them a preferred choice for manufacturing
1. Flexibility Sand casting can accommodate a wide range of sizes and shapes, from small components to large industrial parts. This adaptability allows foundries to cater to various industries and customer needs.
2. Cost-Effectiveness The materials used in sand casting are relatively inexpensive, making it a cost-effective option for producing both small and large quantities of parts.
3. Low Tooling Costs Unlike other casting methods, such as die casting or investment casting, sand casting requires less expensive tooling. This reduces initial investment costs and makes it feasible for startups and smaller companies to enter the manufacturing space.
sand casting foundries
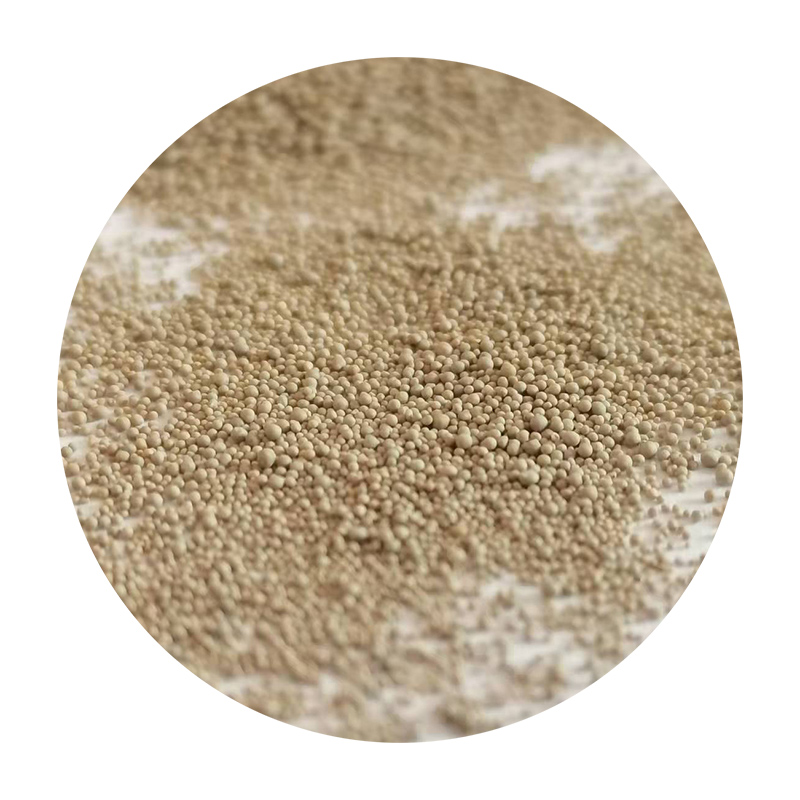
5. Large Production Capabilities Sand casting is capable of producing large components, with foundries able to create pieces weighing several tons.
Challenges Faced by Sand Casting Foundries
Despite its advantages, sand casting also comes with challenges. Some of the primary issues include
1. Surface Defects While advancements have improved surface quality, defects such as sand inclusions, blow holes, and misruns can still occur, affecting the integrity of the final product.
2. Labor Intensive The process often requires significant manual labor, from mold preparation to finishing, which can lead to variability in quality and increased production time.
3. Environmental Concerns The sand casting process generates dust and waste products, raising environmental issues regarding disposal and emissions.
Applications of Sand Casting
Sand casting is widely used in various sectors, including
- Automotive Industry Used to produce engine blocks, transmission cases, and various components that require strength and durability. - Aerospace Critical components such as turbine housings and brackets, where precision and reliability are paramount. - Construction and Heavy Machinery Heavy-duty parts like gears, housing assemblies, and specialized tools.
In conclusion, sand casting foundries play a vital role in the manufacturing landscape, combining traditional methods with modern technology to meet the demands of various industries. As advancements continue to emerge, the efficiency, quality, and applicability of sand casting will likely improve, solidifying its place as a cornerstone of metalworking processes for years to come.
Post time:พ.ย. . 27, 2024 14:24
Next:Techniques for Smoothing and Finishing 3D Printed Models for a Professional Look