Understanding Sand Casting Costs An Overview
Sand casting is a versatile and widely used manufacturing process in various industries, including automotive, aerospace, and art. Despite its simplicity, the cost associated with sand casting can vary significantly based on several factors. Understanding these costs is essential for manufacturers and businesses to optimize their production processes and achieve cost-effectiveness.
One of the primary components of sand casting costs is the material. The type of sand used, typically silica sand, plays a crucial role in determining expenses. High-quality sand may be more expensive, but it can lead to better mold strength and surface finish, potentially reducing the need for secondary operations. Other material costs include the metal being cast, which can fluctuate based on market prices. For example, aluminum and iron are commonly used metals, and their prices can vary due to global supply and demand dynamics.
Labor costs also factor significantly into the total cost of sand casting. Skilled labor is required for the preparation of molds, melting metals, and ensuring quality control throughout the casting process. The complexity of the casting design impacts labor costs; intricate designs may demand more time and skilled workers, raising overall expenses. Additionally, geographical location can affect labor costs, with some regions having higher wages than others.
sand casting cost
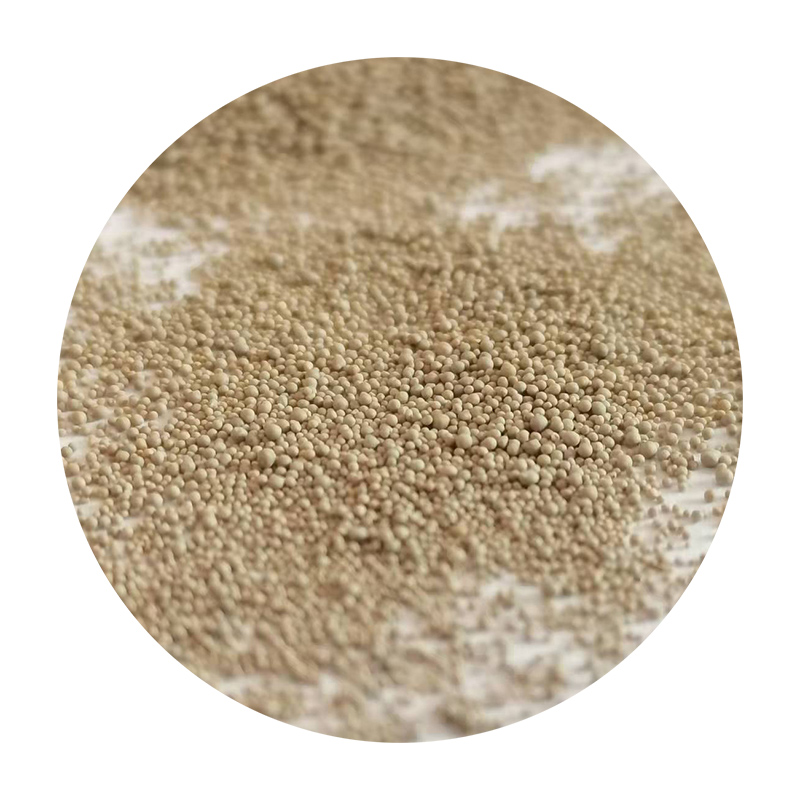
Another important aspect is the initial setup and tooling costs. Creating molds for sand casting often involves significant upfront investment. The design of the mold must be precise to ensure that the final casting meets specifications. Companies may also need to invest in equipment for melting metals and sand preparation, contributing to the overall capital expenditure.
Production volume is another critical consideration. Sand casting is particularly cost-effective for large production runs, as the initial setup costs can be spread across numerous units. Conversely, for small production runs, the high setup costs may make sand casting less economical compared to alternative methods like CNC machining or 3D printing, which may offer lower setup costs for smaller batches.
Moreover, recycling sand can help reduce costs in the long run. Sand casting produces a significant amount of waste material, but by properly managing and recycling used sand, manufacturers can cut down on material expenses while also promoting sustainability.
In conclusion, understanding the various elements that influence sand casting costs—such as materials, labor, tooling, production volume, and waste management—is crucial for manufacturers aiming to maintain competitiveness. By carefully managing these factors, businesses can optimize their sand casting processes, reducing overall expenses while ensuring high-quality production. As technology continues to advance, the future of sand casting may also bring innovations that further enhance efficiency and cost-effectiveness, keeping this traditional manufacturing method relevant in a constantly evolving industry.
Post time:ก.ย. . 25, 2024 10:04
Next:Materials Utilized in Sand Casting Processes and Their Impact on Quality