The Process and Benefits of Sand Casting in Foundries
Sand casting is one of the most traditional and commonly used metal fabrication techniques in foundries around the world. This method involves the creation of metal parts by pouring molten metal into a mold made from sand. While it may seem rudimentary, sand casting possesses a range of advantages that make it a go-to choice for producing a wide variety of metal components.
The Sand Casting Process
The sand casting process begins with the preparation of a mold. It typically consists of a mixture of sand, a binding agent, and water. The sand is shaped into two halves of a mold, known as the cope (the top half) and the drag (the bottom half). The design of the mold is created based on the desired shape of the final product. This often involves the use of patterns, which are replicas of the object to be cast. Patterns can be made from materials such as wood, plastic, or metal, and they are crucial for ensuring the accuracy of the final piece.
Once the sand mold is ready, it is packed tightly to ensure that it can withstand the pressure of the molten metal. The next step involves creating a pouring cup and channels to allow the molten metal to flow into the mold cavity. After the mold is prepared, the metal—commonly aluminum, iron, or steel—is heated until it becomes molten, and then poured into the mold through the pouring cup. The casting is left to cool and solidify for a predetermined period, after which the mold is removed, and the new metal part is extracted.
Advantages of Sand Casting
One of the primary advantages of sand casting is its versatility. This method can be used to produce a wide array of metal shapes and sizes, ranging from small components to massive parts. The process is adaptable and can handle different materials, making it suitable for various applications, including automotive, aerospace, and machinery parts.
sand cast foundry
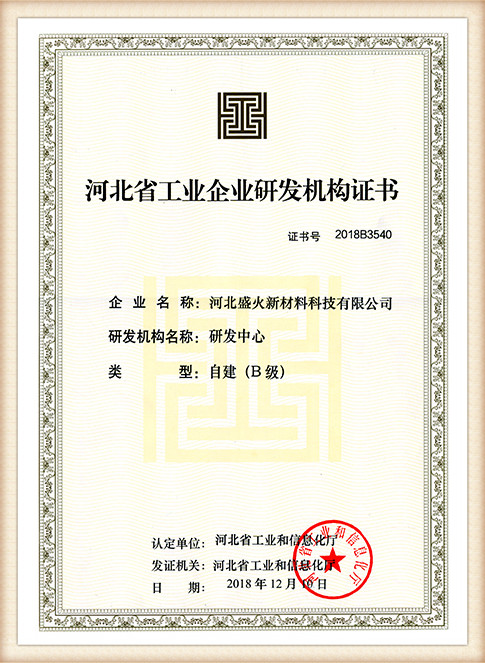
Another significant benefit of sand casting is its cost-effectiveness, especially for small production runs. The materials used in sand casting, primarily sand and a binder, are relatively inexpensive compared to those used in other casting methods. The molds can be reused multiple times, which further reduces production costs. For high-volume production, while the initial costs might be higher for creating permanent molds, the long-term savings can be substantial, as the manufacturing process becomes more streamlined.
Furthermore, sand casting allows for the production of complex geometries that might be challenging or impossible to achieve with other manufacturing techniques. The flexibility in design means that engineers and designers can innovate without being hindered by processing limitations, enabling the creation of intricate features that enhance the functionality of the final product.
Environmental Considerations
In addition to its economic benefits, sand casting has some environmental advantages. Modern foundries have implemented sustainable practices, such as recycling sand and reducing waste. The sand used in molds can be reclaimed and reused, significantly lowering the demand for new sand. Moreover, advances in technology, such as the use of computer-aided design (CAD) and 3D printing for creating patterns, are optimizing the sand casting process, reducing emissions, and minimizing material waste.
Conclusion
In conclusion, sand casting remains a fundamental technique in the metal fabrication industry due to its adaptability, cost efficiency, and capacity to produce intricate designs. With continuous advancements in technology and sustainability practices, the sand casting process is poised to remain relevant and competitive. Foundries leveraging this time-tested method are likely to lead the way in innovation while maintaining a commitment to environmental stewardship, making sand casting a cornerstone of modern manufacturing. As industries continue to grow and evolve, the importance of sand casting will endure, reinforcing its status as an indispensable tool for engineers and manufacturers alike.
Post time:พ.ย. . 17, 2024 09:36
Next:Kosten van zandgieten en factoren die de prijs beïnvloeden