Understanding the Resin Sand Casting Process
Resin sand casting is a modern and highly efficient method in the foundry industry, known for its ability to produce high-quality metal components with excellent dimensional accuracy and surface finishes. This process differs significantly from traditional sand casting methods primarily through the use of a resin binder that enhances the properties of the molding sand.
What is Resin Sand Casting?
In resin sand casting, the sand mixture comprises fine silica sand combined with a thermosetting resin as a binding agent. This combination creates a mold that is not only strong but also flexible, allowing for the production of intricate geometries that would be challenging with conventional methods. The resin hardens upon exposure to heat, creating a durable mold that can withstand the rigors of the casting process.
The Process
The resin sand casting process typically involves several key steps
1. Preparation of the Pattern A pattern, which is a replica of the item to be cast, is created, typically from metal or plastic. This pattern plays a critical role in defining the shape and dimensions of the final product.
2. Mixing Sand and Resin The silica sand is mixed with the thermosetting resin and a hardening agent in a specific ratio. This mixture is crucial as it determines the quality of the mold.
3. Mold Formation The resin-coated sand is packed around the pattern in a molding box. Once the desired thickness is achieved, heat is applied through the use of hot air, which activates the resin and hardens the mold.
resin sand casting process
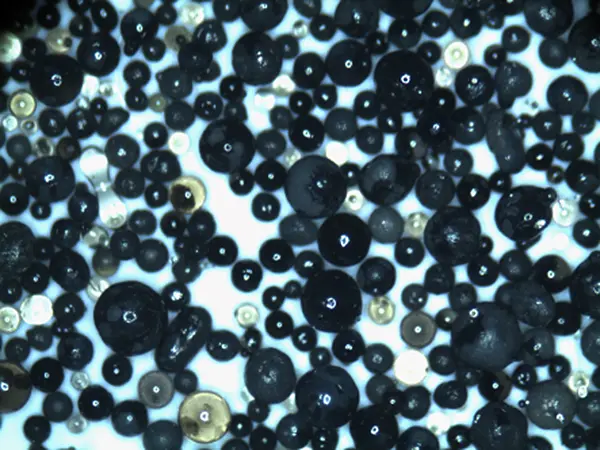
4. Cooling and Demolding After sufficient curing time, the mold is allowed to cool. Once cooled, it is carefully removed from the pattern, resulting in two halves of the mold that can be assembled for casting.
5. Pouring the Metal The mold is assembled, and molten metal is poured into the cavity. The high-strength mold can handle the thermal shock associated with the pouring of molten metal.
6. Finishing Operations Once the metal has cooled and solidified, the mold is broken apart, and the casting is retrieved. The final step often involves finishing operations such as machining, sandblasting, or polishing to achieve the desired specifications.
Advantages of Resin Sand Casting
One of the most notable advantages of resin sand casting is the reduction in defects, such as sand inclusions and surface imperfections, often found in traditional sand casting. The use of resin allows for better dimensional control and finer surface finishes, which can lead to reduced processing time and costs.
Additionally, the tooling used in resin sand casting allows for higher production rates and reusable molds, making it economical for both small-scale and large-scale production runs. This process is particularly advantageous for industries requiring high precision and complex designs, such as automotive, aerospace, and various machinery applications.
Conclusion
The resin sand casting process represents a significant advancement in foundry technology, offering a combination of flexibility, precision, and efficiency. As industries continue to demand higher quality components, understanding and leveraging the benefits of resin sand casting will play an essential role in meeting those needs, driving innovation, and maintaining a competitive edge in manufacturing.
Post time:ต.ค. . 09, 2024 04:10
Next:Exploring Sand Types for Foundry Applications and Their Impact on Casting Quality