Resin Sand Casting A Modern Approach to Precision and Quality
Resin sand casting, an innovative method of metal casting, has gained popularity in various industries due to its precision, versatility, and efficiency. This technique utilizes a mixture of sand and resin to create molds for casting metals, and it offers several advantages over traditional sand casting methods. This article aims to explore the benefits, processes, and applications of resin sand casting.
The Casting Process
The resin sand casting process begins with the preparation of the sand mixture. In this method, fine silica sand is blended with a thermosetting resin and a hardener. This mixture is then formed around a pattern to create a mold. The unique aspect of resin sand casting is that the resin is cured at room temperature, which allows for a much faster solidification of the mold compared to conventional methods. Once the mold is ready, molten metal is poured into it, and after cooling, the mold is broken apart to retrieve the casted part.
Advantages of Resin Sand Casting
1. Precision and Surface Finish One of the most significant advantages of resin sand casting is the ability to achieve high precision and excellent surface finishes. The resin binds the sand particles tightly together, resulting in a smooth mold surface that replicates the pattern accurately. This leads to reduced post-processing requirements and a better final product.
2. Complex Shapes and Thin Walls Resin sand casting allows for the production of complex geometries and thinner wall sections that would be difficult or impossible to achieve with traditional casting methods. The versatility of this technique makes it suitable for intricate designs often required in industries such as automotive, aerospace, and art.
resin sand casting
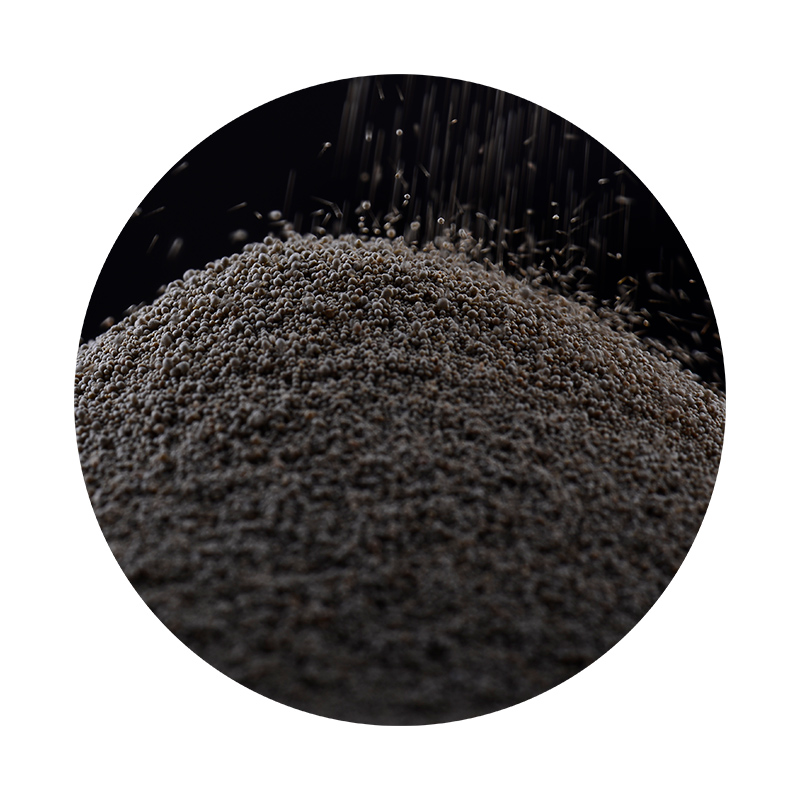
3. Faster Production Cycles Since the molds cure quickly and can be reused multiple times, resin sand casting leads to shorter production cycles. This efficiency is particularly beneficial in high-volume manufacturing, where time savings can result in significant cost reductions.
4. Reduced Defects The inherent properties of resin sand mixtures help to minimize common casting defects such as sand inclusions and mold shift. This results in a higher yield of acceptable parts, ultimately enhancing productivity and profitability for manufacturers.
Applications of Resin Sand Casting
Resin sand casting is utilized across various sectors. In the automotive industry, it is commonly used for producing engine blocks, cylinder heads, and other critical components where precision and strength are paramount. The aerospace sector also benefits from this method, as it produces lightweight but durable components essential for aircraft performance. Moreover, artistic applications such as sculptures, custom metalwork, and decorative items are increasingly being created using resin sand casting techniques, showcasing its versatility beyond industrial uses.
Conclusion
Resin sand casting represents a significant advancement in the field of metal casting, combining the traditional aspects of sand casting with the modern benefits of resin technology. With its ability to produce complex shapes with high precision and excellent surface finishes, this method is paving the way for more efficient manufacturing processes. As industries continue to evolve and demand higher quality standards, resin sand casting is likely to play an increasingly pivotal role in meeting these challenges. By embracing this innovative approach, manufacturers can achieve greater flexibility, efficiency, and quality in their production, positioning themselves for success in today’s competitive market.
Post time:ธ.ค. . 05, 2024 17:24
Next:Exploring the Cost of 3D Sand Printers for Your Projects