Precision Sand Casting A Pathway to Superior Manufacturing
In the realm of manufacturing, precision sand casting has emerged as a vital technique that combines the age-old practices of traditional sand casting with contemporary advancements to create highly detailed and accurate metal components. This method has found applications across various industries, including automotive, aerospace, and energy, where precision and reliability are paramount.
The Basics of Sand Casting
Sand casting is one of the oldest metal casting processes, largely due to its versatility and cost-effectiveness. The method begins with the creation of a mold, formed by packing sand around a pattern that represents the shape of the desired final product. The pattern can be made from various materials, including metal or plastic, and is designed to be easily removable from the sand mold. Once the pattern is removed, molten metal is poured into the cavity created by the mold. After cooling, the sand is removed, leaving behind a sand-cast metal piece.
Advancements in Precision
While traditional sand casting is widely used, its limitations in precision have led to the development of precision sand casting techniques. Innovations in mold-making technology and computer-aided design (CAD) systems have enabled manufacturers to produce molds that are not only more accurate but also capable of capturing intricate details. This increased accuracy reduces the need for extensive post-casting machining processes, saving both time and costs.
The Role of Additives
In precision sand casting, the quality of the sand plays a crucial role. Manufacturers often use specially formulated sand mixtures with precise grain sizes and shapes to enhance the mold's strength and stability. Additives such as binders and coatings are also employed to improve the adhesion of the sand and create smoother mold surfaces. This ensures that the final cast product exhibits superior surface finishes, minimizing the need for additional surface treatments.
precision sand casting
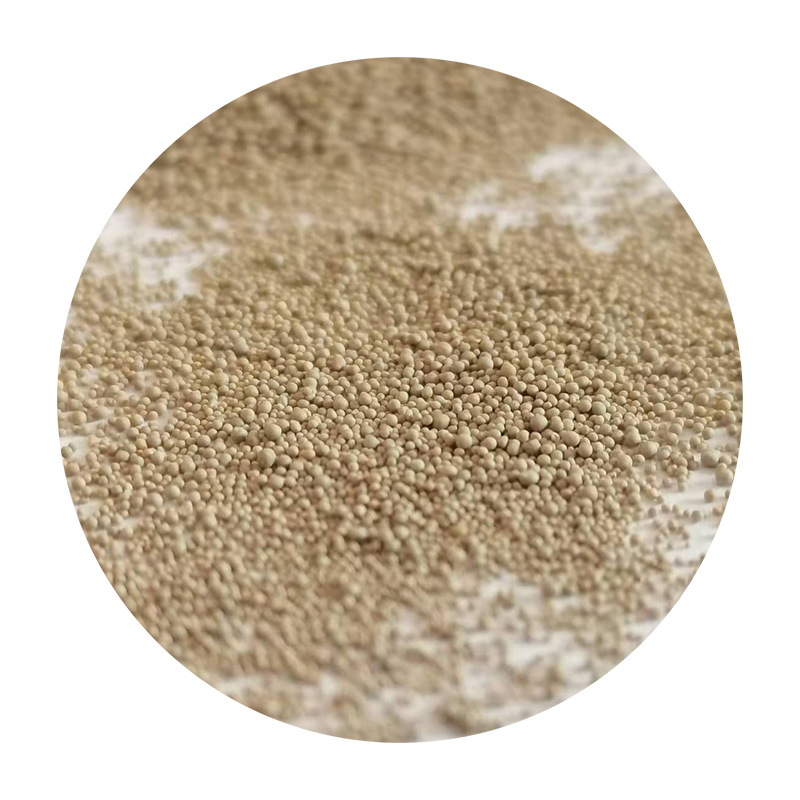
Applications Across Industries
Precision sand casting finds its niche in various sectors due to its ability to produce components that meet strict dimensional and design specifications. In the automotive industry, for example, the production of engine blocks and transmission casings often relies on this method. The aerospace sector benefits from precision sand casting when creating complex components like turbine housings, where weight reduction and strength are critical. Additionally, the energy sector utilizes precision sand-cast parts in the construction of wind turbine components and other infrastructure.
Environmental Considerations
As the manufacturing industry shifts toward more sustainable practices, precision sand casting has also evolved. Many foundries are adopting environmentally friendly practices by recycling used sand and minimizing waste. The use of synthetic sands and eco-friendly binders reduces harmful emissions and the overall environmental impact of the casting process. These advancements not only contribute to sustainability but also enhance the competitiveness of precision sand casting in the global market.
The Future of Precision Sand Casting
Looking ahead, the future of precision sand casting appears promising. The integration of advanced technologies such as 3D printing is revolutionizing mold-making processes, allowing for rapid prototyping and the production of complex geometries that were once impossible with traditional techniques. Furthermore, the increasing demand for lightweight and durable materials presents new opportunities for precision sand casting to thrive.
Conclusion
In conclusion, precision sand casting stands at the intersection of tradition and innovation, offering a method that ensures detailed accuracy while addressing the modern demands of various industries. As technology continues to advance and adapt, precision sand casting is poised to play an even more significant role in the manufacturing landscape, driving efficiency, sustainability, and superior quality in metal component production. Embracing this technique can ultimately lead to enhanced performance and innovation across numerous applications, making it a key pillar of the manufacturing industry’s future.
Post time:พ.ย. . 28, 2024 05:59
Next:3D-друк у пясчаным ліцці тэхналогіі і перавагі для сучаснай вытворчасці