The Lost Foam Casting Process An In-Depth Look
Lost foam casting is an advanced manufacturing process that has gained considerable attention in the foundry industry due to its unique advantages and applications. This technique is particularly valued for its efficiency, flexibility, and ability to produce complex shapes with high precision. In this article, we will explore the lost foam casting process, its benefits, applications, and key considerations for its successful implementation.
What is Lost Foam Casting?
Lost foam casting (LFC) is a process that involves creating a pattern made from foam, typically polystyrene, which is then coated with a fine layer of sand. The pattern is then placed in a mold and molten metal is poured directly into the cavity created by the foam pattern. As the molten metal enters the mold, the foam pattern evaporates or loses itself, hence the name lost foam.
This process simplifies traditional casting methods, where metal would normally be poured into a rigid mold made from metal. Instead, LFC uses a consumable foam pattern that allows for greater design freedom and more detailed outcomes. It stands out among other casting techniques because it does not require a solid mold, thus reducing production costs and lead times.
Benefits of Lost Foam Casting
1. Complex Geometries One of the significant advantages of lost foam casting is its capability to create complex geometries that would be challenging or impossible to achieve with traditional casting methods. This includes intricate designs with thin walls and internal passages.
2. Reduced Production Time Since there is no need for complex tooling or multiple setups, the process can save considerable time during production. The direct pouring of molten metal into the foam pattern streamlines the workflow.
3. Material Efficiency The lost foam method generates less scrap material compared to traditional casting processes. The foam pattern is fully consumed in the process, making it an environmentally friendly choice as well.
4. Surface Finish and Dimensional Accuracy The fine sand used in LFC allows for excellent surface finishes and tight tolerances. Components produced can often be used directly without extensive post-processing, reducing overall manufacturing costs.
lost foam castings
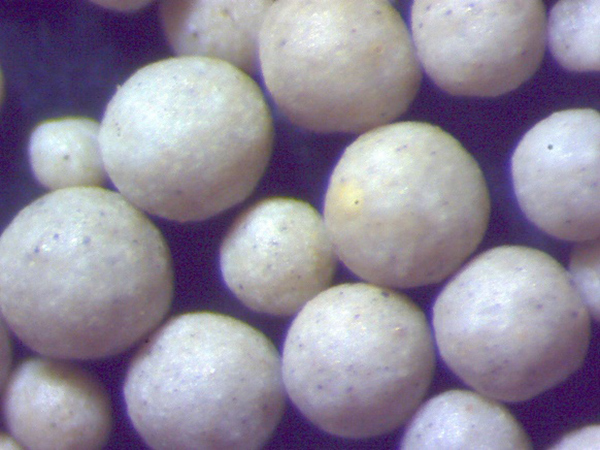
5. Versatile Applications Lost foam casting is suitable for a wide range of metals, including aluminum, cast iron, and steel. This versatility makes it an attractive option for various industries, including automotive, aerospace, and machinery manufacturing.
Applications of Lost Foam Casting
Due to its unique advantages, lost foam casting is employed in a broad array of applications. In the automotive industry, it is used to produce engine blocks, transmission cases, and complex aluminum components that require precision and a reduction in weight. Aerospace applications benefit from LFC for creating intricate parts that can withstand extreme conditions while ensuring a high strength-to-weight ratio.
Additionally, the manufacturing of industrial machinery, agricultural equipment, and high-performance sporting goods often relies on lost foam casting methods to create parts that meet stringent specifications and performance requirements.
Key Considerations for Successful Implementation
Despite its benefits, there are critical considerations to keep in mind when implementing lost foam casting. The quality of the foam pattern is paramount; it must be made from high-density materials that can withstand the pour of molten metal without collapsing. Moreover, the sand coating must be appropriately applied to ensure adequate support during the casting process.
Temperature control is also crucial, as any fluctuations can lead to defects in the final product. Operators need to maintain precise pouring temperatures and conditions to achieve the desired outcome.
Lastly, while lost foam casting can reduce tooling costs, initial investment in machinery and pattern making can be significant. Manufacturers should weigh these upfront costs against the long-term savings and impact on production efficiency.
Conclusion
Lost foam casting is a revolutionary process that continues to transform the way complex components are manufactured across various industries. Its ability to produce intricate designs, combined with the advantages of reduced production time and improved material efficiency, makes it a compelling choice for modern manufacturing. As technology advances, the applications of lost foam casting are likely to expand, further solidifying its role in the future of manufacturing.
Post time:ต.ค. . 16, 2024 21:58
Next:steel sand casting suppliers