Lost Foam Casting Materials A Comprehensive Overview
Lost foam casting is an advanced metal casting process that utilizes a foam pattern to create intricate shapes and designs in metal. The method has gained popularity across various industries due to its ability to produce complex geometries with minimal waste. Understanding the materials used in lost foam casting is crucial for ensuring high-quality outcomes and optimizing the casting process.
The Basics of Lost Foam Casting
In lost foam casting, a foam model, usually made of polystyrene or polyurethane, is coated with a fine sand mixture containing a bonding agent. Once the foam pattern is formed and coated, it is placed in a mold. Upon heating, the foam evaporates, leaving behind a cavity that mirrors the foam pattern. Molten metal is then poured into this cavity, taking the exact shape of the original foam model. This innovative method allows for the production of parts that may be difficult or impossible to achieve with traditional casting techniques.
Key Materials in Lost Foam Casting
1. Foam Patterns
The first and foremost material in lost foam casting is the foam itself. Typically, polystyrene foam (EPS) is the most commonly used due to its lightweight, ease of shaping, and cost-effectiveness. Polystyrene foam can be easily cut and shaped into intricate designs, making it ideal for producing complex patterns. In some cases, polyurethane foam may be utilized, especially for patterns that require higher detail and precision. The choice of foam varies depending on the specific requirements of the casting process and the desired finish of the final product.
2. Coating Materials
After the foam pattern is created, it needs to be coated to withstand the molten metal's temperature. The coating material commonly consists of a mixture of fine aggregates, such as sand, and a binding agent like phenolic resin. This coating process creates a ceramic shell around the foam, providing the necessary strength and durability to withstand the pouring process. The thickness and composition of the coating layer can significantly impact the final part's surface finish and dimensional accuracy.
lost foam casting materials
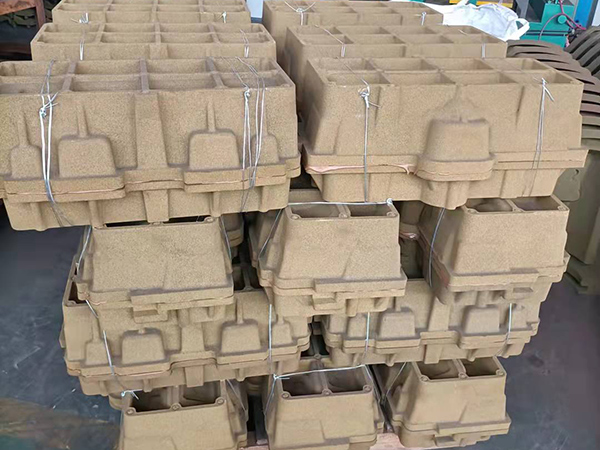
The molding sand is crucial in lost foam casting, as it supports the coating and maintains the necessary cavity shape during casting. The sand used in this process often includes silica sand with specific particle sizes to create a smooth surface and facilitate easy casting. Additionally, the sand must be dry and free of impurities to prevent defects in the final product. Proper selection and preparation of the molding material affect the thermal conductivity and overall effectiveness of the casting process.
4. Bonding Agents
Various bonding agents are employed to ensure that the coating material adheres properly to the foam pattern and maintains its integrity during the metal pouring. Common bonding agents include phenolic resins, which provide excellent heat resistance and stability. The choice of bonding agent can influence the coating's strength and adhesion properties, ultimately impacting the quality of the cast product.
5. Metal Alloys
The choice of metal for pouring also plays a significant role in the lost foam casting process. Common materials include aluminum, cast iron, and various steel alloys. Each metal has specific melting temperatures and properties that must be considered based on the application's requirements. The compatibility of the metal with the foam coating and the overall design of the casting will dictate the performance characteristics of the final product.
Advantages of Lost Foam Casting Materials
The materials used in lost foam casting present several advantages
- Complex Geometries The use of foam patterns allows for the creation of intricate shapes that would be challenging to form using conventional methods. - Reduced Waste Since the foam pattern is lost during the casting process, there is no need for additional core materials, reducing overall waste. - Cost-Effectiveness The materials used in lost foam casting, especially foam and sand, are generally lower in cost compared to traditional materials, making it economically viable for large production runs. - Improved Surface Finish The quality of the coating materials contributes to a smoother surface finish on the final product, often eliminating the need for extensive post-processing.
Conclusion
Lost foam casting is a revolutionary technique that combines innovation with efficiency, offering manufacturers an effective way to produce complex metal components. The careful selection and utilization of materials—foam patterns, coating materials, molding sand, bonding agents, and metal alloys—are paramount to achieving high-quality castings. As this technology continues to evolve, the potential for further advancements in lost foam casting materials will undoubtedly enhance its applications across various industries, from automotive to aerospace. By understanding and optimizing these materials, manufacturers can leverage the full benefits of lost foam casting, leading to improved production capabilities and innovative product designs.
Post time:พ.ย. . 20, 2024 08:24
Next:what is gold sand