The Importance of Sand Casting in Modern Manufacturing
Sand casting, one of the oldest and most versatile metal casting processes, has been a cornerstone in the manufacturing industry for centuries. This method involves creating a mold from sand to pour molten metal, which solidifies into the desired shape. Despite the advent of advanced techniques, sand casting remains critically important due to its unique advantages, broad applicability, and cost-effectiveness.
Versatility Across Industries
One of the most significant advantages of sand casting is its versatility. It can be used to manufacture a wide variety of metal components, from small intricate parts to large heavy-duty casings. Various industries rely on sand casting, including automotive, aerospace, construction, and consumer goods. For instance, in the automotive sector, sand casting is essential for producing engine blocks, transmission housings, and structural components.
Furthermore, sand casting accommodates a range of metals, including aluminum, iron, bronze, and steel. This flexibility allows manufacturers to select the most suitable material for the intended application, ensuring that the end product meets specific performance and durability requirements.
Cost-Effectiveness
The cost-effectiveness of sand casting is another critical factor contributing to its widespread use. The materials required for sand molds are relatively inexpensive, and the process itself does not necessitate complex machinery. As a result, manufacturers can produce components economically, especially in small to medium production runs. This makes sand casting particularly attractive for industries that require prototyping or producing limited quantities of specific parts.
Moreover, the simplicity of the sand casting process allows for reduced labor costs. Skilled workers can create molds efficiently, and the need for elaborate tooling is minimized compared to other casting methods. This factor becomes especially pertinent for startups and small businesses that may have limited budgets yet require high-quality components.
Design Flexibility
In addition to economic advantages, sand casting provides significant design flexibility. This process allows for the forging of complex geometries that might be challenging or impossible to achieve with other methods. The ability to create intricate designs, along with the potential for larger dimensions, enables engineers and designers to innovate freely, pushing the boundaries of product design and functionality.
importance of sand casting
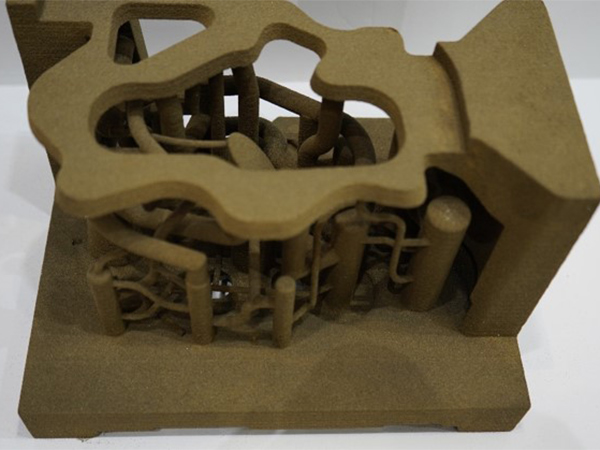
Furthermore, sand molds can be reused multiple times, provided they are maintained properly. This reusability not only contributes to cost savings but also aligns with sustainable manufacturing practices. By reducing waste and promoting recycling, sand casting supports the growing emphasis on environmentally friendly production methods.
Applications in Prototyping and Customization
Sand casting is particularly advantageous for prototyping and customizations. Many industries require rapid prototyping of new designs to test functionality before mass production. Sand casting enables manufacturers to create prototypes quickly and cost-effectively, allowing for iterative design changes without substantial financial risk.
Additionally, the method's flexibility allows for custom orders. Customers often demand unique parts tailored to specific requirements. Sand casting can easily accommodate these specialized requests, providing manufacturers with the ability to cater to niche markets and diverse customer needs.
Challenges and Innovations
Despite its many advantages, sand casting does face certain challenges, including limitations on surface finish quality and dimensional accuracy compared to other casting processes. However, ongoing innovations and technological advancements are continually improving the sand casting process. The integration of computer-aided design (CAD) and computer-aided manufacturing (CAM) systems has enhanced precision and efficiency significantly. These advancements are enabling faster production times and better quality control, thereby addressing some of the traditional drawbacks associated with sand casting.
Moreover, the innovation of new binder materials and sand formulations is evolving, which enhances the mechanical properties of the molds and improves the overall casting quality. These developments ensure that sand casting remains a competitive option in the modern manufacturing landscape.
Conclusion
In conclusion, sand casting plays a vital role in contemporary manufacturing due to its versatility, cost-effectiveness, design flexibility, and ability to accommodate prototyping and customizations. While it faces challenges, ongoing innovations promise to enhance its application and efficiency. As industries continue to evolve, sand casting will undoubtedly remain an essential manufacturing process, laying the groundwork for creativity, sustainability, and economic production in the metalworking sector.
Post time:ต.ค. . 04, 2024 21:21
Next:Comparing Investment Casting and Sand Casting Techniques for Optimal Manufacturing Solutions