Understanding the Cost of Sand Casting A Comprehensive Overview
Sand casting is a widely used manufacturing process in which molten metal is poured into a sand mold to create a desired shape. This technique is favored for its versatility and cost-effectiveness, making it an essential method in industries ranging from automotive to aerospace. However, understanding the overall costs associated with sand casting can be complex as several factors come into play.
Initial Setup Costs
The first major expense in sand casting is the initial setup costs, which include the creation of molds, patterns, and cores. The cost of producing patterns can vary significantly based on the complexity of the part and the type of material used for the pattern. For example, wooden patterns are generally less expensive than metal ones, but they may not withstand the same number of uses. Depending on the intricacy, pattern costs can range from a few hundred to several thousand dollars.
Material Costs
The next significant expense is the raw materials. Sand itself is not particularly expensive, but other additives used to improve the quality of the mold can increase costs. Furthermore, the type of metal being cast—such as aluminum, iron, or steel—will also impact the overall price. Specialty alloys will generally command higher prices due to their unique properties and lower availability, adding to the final cost of the casting process.
how much does sand casting cost
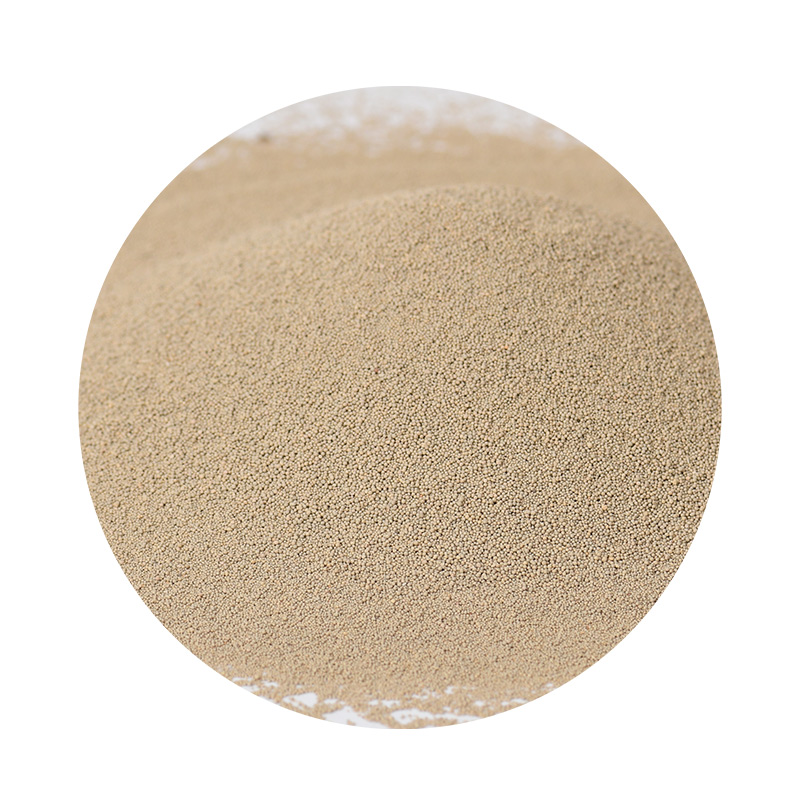
Production Costs
Production costs encompass labor, operation of machinery, and other overhead expenses associated with running a foundry. Labor costs can vary greatly depending on the geographical location and the skill level required for your workforce. Additionally, energy consumption (for melting and pouring metal) represents a significant portion of the operating costs, especially considering fluctuating energy prices.
Volume and Economies of Scale
Another crucial factor influencing the overall cost of sand casting is the volume of production. Higher production runs can significantly reduce the per-unit cost due to economies of scale, making sand casting an attractive option for large production volumes. Conversely, low-volume productions may not benefit from these cost advantages, leading to higher per-unit costs.
Final Considerations
Ultimately, the total cost of sand casting can vary widely based on factors such as design complexity, material selection, and production volume. Businesses considering this manufacturing method should perform a detailed cost analysis that accounts for all variables, including potential wastage and post-processing requirements. By understanding these aspects, manufacturers can make informed decisions that align with their budget and production needs, ensuring that sand casting remains a viable and economical choice for their projects.
Post time:ก.ย. . 10, 2024 10:10
Next:metal sand casting