An Overview of Foundry Sand Types
Foundry sand plays a crucial role in the metal casting industry, serving as a key material in the production of molds and cores. The right choice of sand can significantly impact the quality, efficiency, and cost-effectiveness of the casting process. There are several types of foundry sand, each with unique properties and applications. This article aims to explore the most commonly used foundry sand types, their characteristics, and their uses in the metal casting process.
1. Silica Sand
Silica sand, primarily composed of silicon dioxide, is the most widely used foundry sand. Its properties, such as high melting point, good thermal conductivity, and low expansion rate, make it highly suitable for metal casting. Silica sand is typically used in the production of molds for ferrous and non-ferrous metals. The effectiveness of silica sand can be enhanced with the use of bonding agents, which help improve the sand's adherence and strength. However, it is essential to control the silica content to ensure safety and compliance with health regulations.
2. Green Sand
Green sand is a mixture of silica sand, clay, and water. The clay acts as a binder to hold the sand grains together while water adds moisture to the mix. This type of sand is called green due to its moisture content and is primarily used for producing molds in a process known as green sand molding. Green sand offers excellent collapsibility, allowing for easy removal of castings, and provides good mechanical strength to withstand the pressure of molten metal. Its cost-effectiveness and versatility make it a popular choice among foundries.
3. Resin Sand
foundry sand types
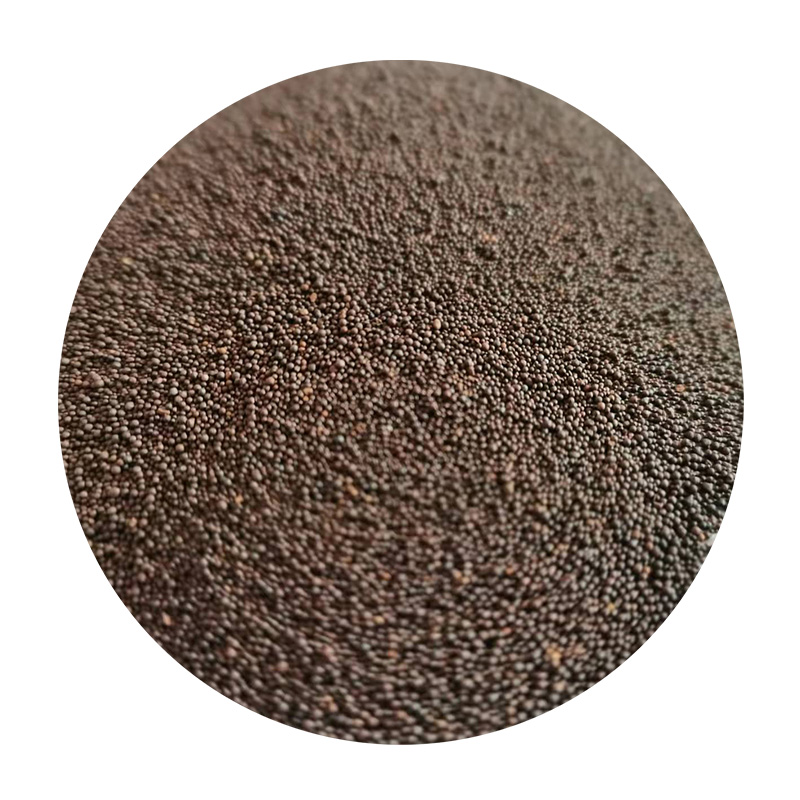
Resin sand, also known as synthetic sand, utilizes a resin binder instead of clay. This type of sand is typically more expensive than green sand but offers superior performance characteristics. Resin sand molds have a higher strength, allowing for finer details and smoother surface finishes in cast products. They also exhibit better dimensional stability and can withstand higher temperatures, making them suitable for applications that require precision and high-performance castings. Additionally, resin sand can be reused multiple times, adding to its cost-effectiveness in the long run.
4. Chromite Sand
Chromite sand is a naturally occurring sand that contains chromite ore. Its unique properties, such as high thermal stability and low thermal expansion, make it ideal for applications that require excellent dimensional accuracy and surface finish. Chromite sand is often used in high-temperature castings, such as those in the aerospace and automotive industries, where performance is critical. While more expensive than silica sand, its ability to withstand high temperatures makes it a valuable choice in specific applications.
5. Zircon Sand
Zircon sand is derived from zirconium silicate. It possesses remarkable thermal properties and is highly resistant to thermal shock, making it suitable for a wide range of metal casting applications. Zircon sand is often used in high-performance scenarios, particularly in casting non-ferrous metals. It provides excellent mold stability and durability, contributing to the overall improvement of casting quality by minimizing defects and enhancing surface finishes.
Conclusion
Choosing the right type of foundry sand is paramount for optimizing the casting process. Each type of sand offers its unique benefits and drawbacks, depending on the specific requirements of the casting operation. From silica and green sand to more advanced options like resin, chromite, and zircon sands, understanding these materials allows foundries to select the most appropriate sand for their needs, thereby improving product quality, reducing costs, and enhancing operational efficiency. As technology evolves, so too may the properties and applications of foundry sands, paving the way for even greater innovations in the casting industry.
Post time:พ.ย. . 08, 2024 10:11
Next:Properties and Characteristics of Foundry Sand for Optimal Casting Performance