The Role of Sand Casting in Modern Manufacturing
Sand casting is a versatile and widely used manufacturing process that has been around for centuries. It plays a crucial role in various industries, particularly in the production of metal components. As global demand for customized and complex shapes increases, the importance of sand casting becomes ever more pronounced. This article explores the significance of sand casting, its advantages, and why one might consider investing in it for their manufacturing needs.
What is Sand Casting?
Sand casting is a metal casting process that involves creating a mold from sand, which is then used to form parts by pouring molten metal into the mold cavity. The sand mold consists of two halves the cope (top half) and the drag (bottom half). Once the molten metal is poured into the mold and allowed to cool, the sand is removed, resulting in a cast metal part.
Advantages of Sand Casting
1. Cost-Effectiveness One of the primary reasons manufacturers choose sand casting is its cost-effectiveness. The materials used to create the mold are relatively inexpensive, making it accessible for both small-scale and large-scale production. Additionally, the process requires less upfront investment compared to other casting methods.
2. Flexibility in Design Sand casting supports a wide range of designs and sizes. It is particularly suited for producing complex geometries and large parts, making it an excellent choice for industries such as automotive, aerospace, and heavy machinery. The use of sand allows for intricate details that are often challenging to achieve with other methods.
3. Material Versatility This casting process can accommodate various metals, including aluminum, iron, bronze, and magnesium. This versatility allows manufacturers to select the most suitable materials for their specific applications, which can enhance performance and longevity.
4. Scalability Sand casting is highly scalable, making it ideal for both low-volume and high-volume production runs. Manufacturers can efficiently switch between different part sizes and designs without significant downtime or retooling, giving them a competitive edge in a fast-paced market.
The Process of Sand Casting
buy sand casting
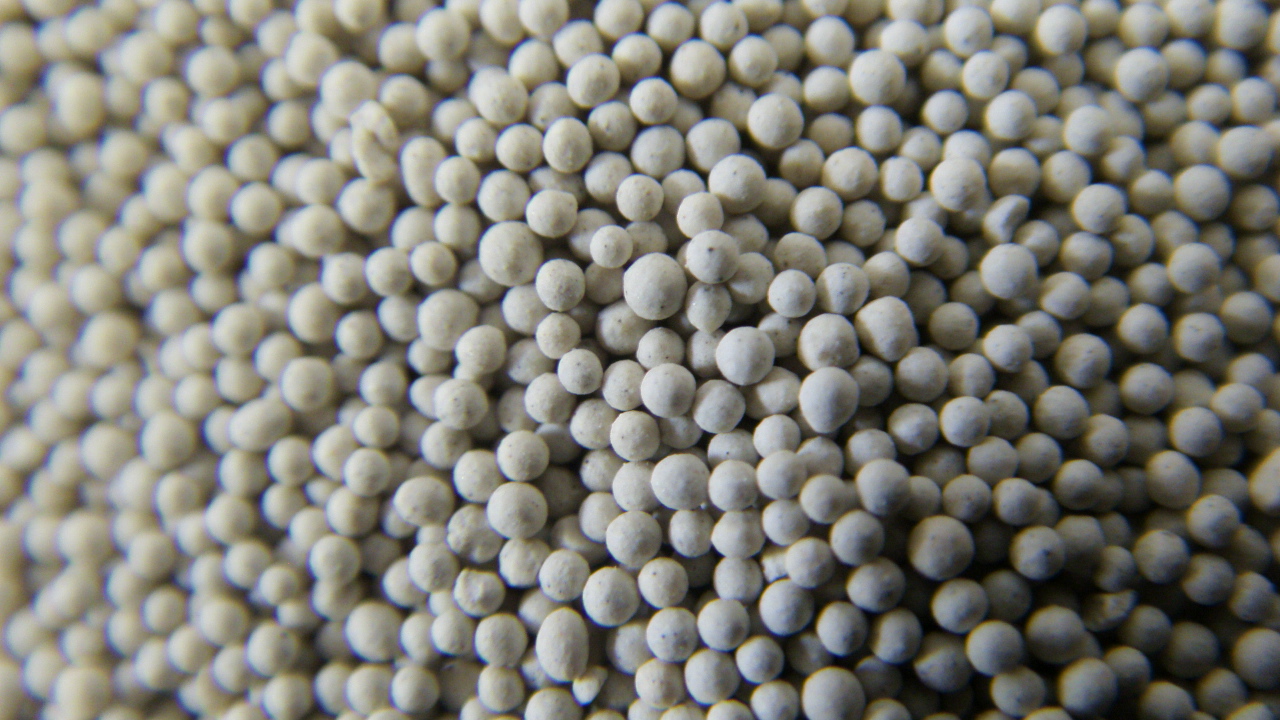
The sand casting process involves several key steps
1. Pattern Making A pattern (usually made of wood, metal, or plastic) is created based on the desired part. This pattern is used to shape the sand mold.
2. Mold Creation The pattern is pressed into specially prepared sand to form the mold halves. The sand is typically mixed with a binder to enhance its strength and shape retention.
3. Mold Assembly After the two halves of the mold are created, they are assembled and secured.
4. Melting and Pouring The chosen metal is heated until it melts and is then poured into the mold through a gating system.
5. Cooling and Removal Once the metal has cooled and solidified, the sand mold is broken apart, and the cast part is removed.
6. Finishing The final steps may involve trimming, machining, or other finishing processes to ensure that the part meets the required specifications.
Conclusion
In conclusion, sand casting is a time-tested manufacturing process that offers numerous benefits. Its cost-effectiveness, design flexibility, material versatility, and scalability make it a popular choice among manufacturers. As industries continue to evolve and demand for customized solutions rises, investing in sand casting could provide significant advantages. Whether you are looking to produce large components or intricate designs, sand casting remains a reliable and efficient option in the manufacturing landscape.
Post time:ต.ค. . 16, 2024 00:18
Next:Applications of Sand Casting in Various Industries and Product Examples