Why Sand Casting is Used An Overview
Sand casting is a manufacturing process that has stood the test of time, dating back thousands of years. It remains one of the most widely utilized methods for producing metal parts, largely due to its numerous advantages and versatility. This article explores the reasons why sand casting is a popular choice in various industries.
1. Cost-Effectiveness
One of the primary reasons sand casting is favored in the metalworking industry is its cost-effectiveness. The materials used in sand casting, primarily sand and metal, are relatively inexpensive. Furthermore, the process does not require expensive tools or machinery, making it accessible for both large-scale manufacturers and smaller operations. This economic efficiency makes sand casting an ideal choice for producing components in high volumes or with specific, one-off requirements.
2. Design Flexibility
Sand casting offers unparalleled design flexibility. This process allows for the creation of complex shapes and intricate details that may be difficult or impossible to achieve with other manufacturing techniques. The molding sand can be easily shaped, enabling manufacturers to produce precise patterns that replicate the desired final product. This flexibility accommodates a wide range of sizes—from small components to large structural elements—thus serving diverse industrial applications like automotive, aerospace, and consumer products.
Another significant advantage of sand casting is its compatibility with various metals. The process works well with ferrous metals like cast iron and steel, as well as non-ferrous metals such as aluminum, bronze, and copper. This versatility allows manufacturers to choose the most appropriate materials based on the specific requirements of their products, whether it be strength, weight, or corrosion resistance.
why is sand casting used
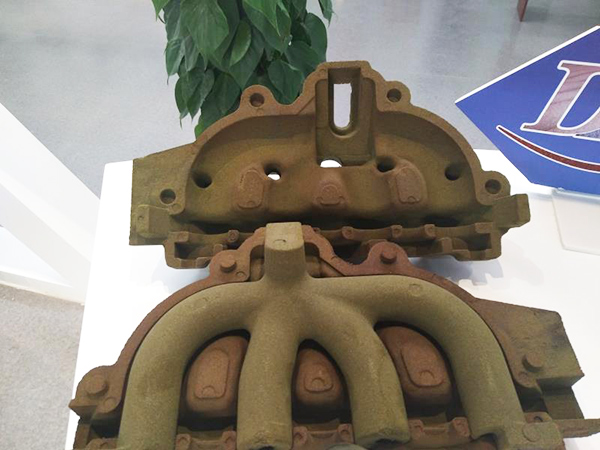
4. Scalability
Sand casting is easily scalable to meet production demands. Whether a company needs to produce a small batch of parts or a large quantity, the process can be adjusted accordingly. It is particularly useful in prototype development, where a few units may be required for testing purposes. As the design is finalized, production can quickly ramp up to meet higher demands, making sand casting a reliable option for evolving project requirements.
5. Low Energy Consumption
Compared to other casting methods, sand casting generally requires lower energy input, especially in terms of heating and cooling. This results in not only reduced operational costs but also a smaller environmental footprint. With growing concerns about sustainability, industries are increasingly looking for methods that minimize energy consumption, and sand casting fits this bill.
6. Simplified Tooling
The tooling for sand casting is generally simpler than that for other types of casting or manufacturing processes. Patterns are made from materials such as wood or plastic, which can be produced quickly and affordably. This simplicity leads to shorter lead times and allows for faster adjustments to designs, which is critical in an ever-evolving market.
In conclusion, sand casting remains a vital manufacturing process for numerous industries due to its cost-effectiveness, design flexibility, material versatility, scalability, low energy consumption, and simplified tooling. As technology advances, this age-old technique continues to adapt, meeting contemporary manufacturing demands while providing an efficient solution for producing quality metal components.
Post time:సెప్టెం . 28, 2024 09:47
Next:3d printing with sand