What is Sand Casting?
Sand casting is one of the oldest and most widely used metalworking processes, employed for creating a wide variety of objects and components ranging from simple toys to intricate industrial parts. This versatile casting technique utilizes a mold formed from sand to shape molten metal as it cools and solidifies, resulting in a final product that mirrors the mold's design.
The Sand Casting Process
The sand casting process begins with creating a mold. This mold is made from a mixture of sand, clay, and water, which gives it the necessary properties to hold its shape when the molten metal is poured in. The sand is packed around a pattern—which is a replica of the final object—to form two halves of the mold. Once the pattern is removed, the two halves are joined together, leaving a cavity in the shape of the desired part.
Next, metal is heat-processed until it becomes molten. Common metals used in sand casting include aluminum, iron, brass, and bronze. The choice of metal often depends on the application's requirements, such as strength, weight, and corrosion resistance. Once the metal reaches the appropriate temperature, it is poured into the mold through a sprue—a vertical channel that allows the molten metal to flow into the mold cavity.
After the metal has cooled and solidified, the mold is broken away to reveal the cast part. The casting might require cleaning to remove any sand residues as well as additional finishing processes, such as machining, painting, or surface treatment, to enhance its quality and appearance.
Advantages of Sand Casting
what is a sand casting
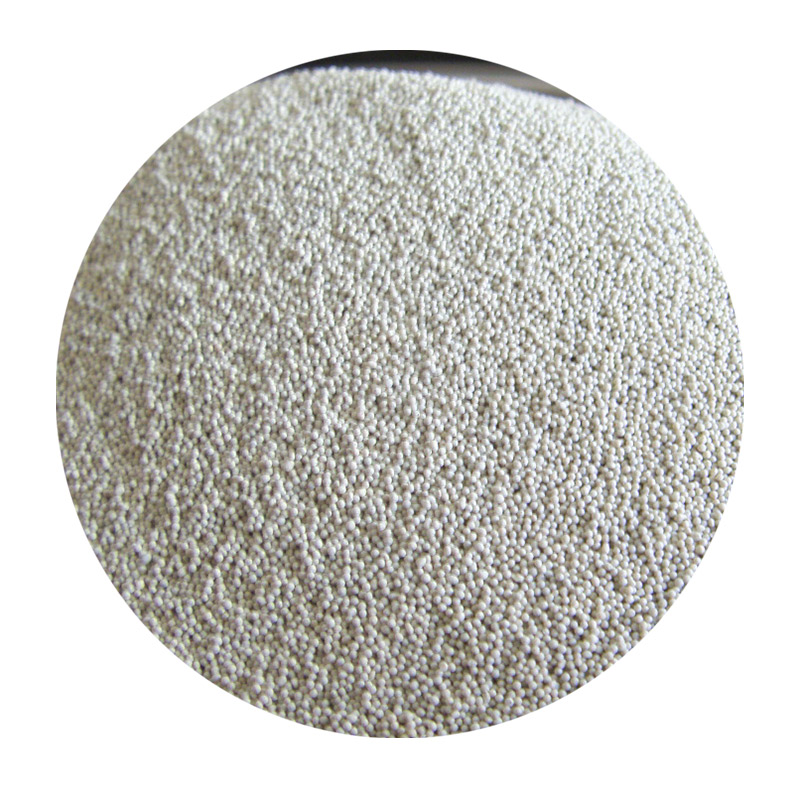
One of the primary advantages of sand casting is its cost-effectiveness, especially for small to medium-sized production runs. The materials for sand molds are relatively inexpensive, and the process allows for the creation of complex shapes and large components that might be difficult or impossible to produce using other methods.
Sand casting is also highly adaptable. It can accommodate a wide variety of metals and alloys, making it suitable for a diverse range of applications across different industries, including automotive, aerospace, and art. Furthermore, because the sand molds can be easily reshaped, it supports both prototyping and large-scale production without significant investments in tooling.
Limitations of Sand Casting
Despite its advantages, there are limitations to the sand casting process. One key drawback is the surface finish of the cast components, which is generally rough and may require significant post-processing to achieve a smoother finish. Additionally, the precision of sand casting may not match that of other methods like investment casting or die casting, which can result in tighter tolerances and finer details.
Furthermore, the process can be labor-intensive, requiring skilled workers to prepare, manage, and monitor various steps of the process, especially when producing complex parts.
Conclusion
In summary, sand casting remains a fundamental and versatile manufacturing technique that plays a crucial role in various sectors. Its simplicity, cost-efficiency, and adaptability make it a preferred choice for many engineers and manufacturers worldwide. Understanding the intricacies of sand casting can help businesses leverage it effectively to produce high-quality metal components that meet their operational needs.
Post time:నవం . 06, 2024 04:47
Next:Exploring Various Materials Used in Sand Casting Processes and Techniques