The Sand Foundry Process An Overview
The sand foundry process is a critical component of the metal casting industry, utilized extensively for producing a wide range of metal components. It is particularly favored due to its versatility, cost-effectiveness, and the ability to create complex geometries with fine details. The basic principle involves pouring molten metal into a sand mold that solidifies to form the desired shape. This method has its roots in ancient practices, but modern advancements have significantly improved its efficiency and output.
The first step in the sand foundry process is pattern making. A pattern is a replica of the final product, typically made from materials like wood, metal, or plastic. The choice of material often depends on the production volume and complexity of the component. Patterns can be single-use or reusable, and they come in different types such as solid patterns, split patterns, or shell patterns. The design of the pattern must account for various factors, such as shrinkage and draft angles, to ensure dimensional accuracy in the final casting.
Once the pattern is ready, the next phase is molding. This process involves creating a mold cavity using a mixture of sand, clay, and water. The sand foundry typically employs a variety of sand types, with silica sand being the most common due to its excellent properties. The sand is compacted around the pattern, forming a mold. Various molding techniques, such as green sand molding or resin-bonded sand molding, are used depending on the requirements of the casting. Green sand is a mixture of sand, clay, and water that remains moist, while resin-bonded sand uses synthetic resin as a binding agent and hardens after application of heat.
sand foundry process
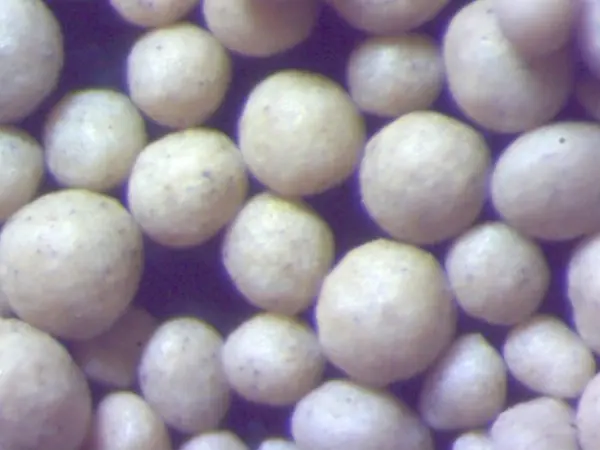
Once the mold is prepared, the next step is metal pouring. Molten metal, usually derived from sources such as scrap metal or alloys, is heated to a specific temperature to achieve a liquid state. The molten metal is then poured into the mold cavity through a pouring basin and runner system. The design of the gating system is crucial, as it affects the flow of the metal and can influence casting integrity. After pouring, the metal fills the mold cavity and starts to cool, solidifying into the desired shape.
After sufficient cooling, the mold is broken to retrieve the casting. The next stage involves various finishing processes such as cleaning, machining, and inspection. Sand is removed from the surface, and any excess material, known as flash, is trimmed off. The casting may then undergo further finishing operations to meet specific tolerances and surface roughness requirements.
In conclusion, the sand foundry process is a vital technique in the production of metal castings, combining artistry and engineering. Its ability to produce intricate parts in a cost-effective manner makes it indispensable in various industries, including automotive, aerospace, and machinery manufacturing. As technology continues to evolve, the sand foundry process will likely integrate advanced methods such as 3D printing and automation, further enhancing its capabilities and efficiency in meeting the demands of modern manufacturing.
Post time:అక్టో . 09, 2024 13:54
Next:sintered sand