The Art and Science of Sand Casting Metal
Sand casting is one of the oldest and most versatile metal casting processes still in use today. This method involves creating a mold using sand and then pouring molten metal into that mold to produce a final product. Its popularity stems from its simplicity, cost-effectiveness, and ability to produce complex shapes, making it an essential technique in various industries, including automotive, aerospace, and art.
At the heart of sand casting lies the mold-making process, which typically begins with the creation of a pattern. This pattern is usually made from materials like wood, metal, or plastic and is a replica of the final product. It is essential that the pattern is designed to account for the shrinkage of metal as it cools, as well as any draft angles needed for easy removal from the mold. Once the pattern is ready, a mixture of sand and bonding agent is formed around it to create the mold.
The Art and Science of Sand Casting Metal
After the mold is prepared, it is closed again, and molten metal is poured into the cavity. This metal is usually heated to a temperature well above its melting point, ensuring a fluid form that can fill intricate details of the mold. Once poured, the metal begins to cool and solidify within the mold, taking on its shape. The cooling process is critical, as it affects not only the dimensions but also the properties of the finished metal object.
sand cast metal
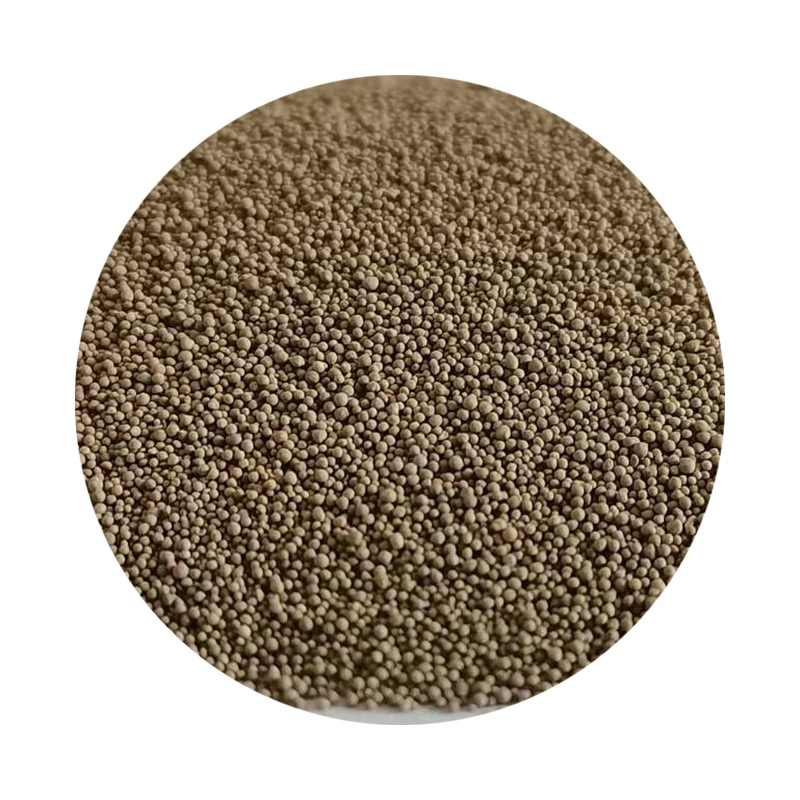
After sufficient cooling, the mold is broken away to reveal the cast part. Depending on the design and its complexity, additional finishing work may be required, such as grinding, sanding, or machining, to achieve the desired surface finish and tolerances. This post-processing is vital to ensure that the final piece meets the specifications required for its intended application.
The advantages of sand casting are numerous. It allows for the production of large and heavy parts, which might be difficult to achieve with other casting techniques. Additionally, the process can accommodate a variety of metals — from iron and aluminum to zinc and magnesium. Sand casting also produces minimal waste, making it a more sustainable option in metal manufacturing. Furthermore, because molds can be made relatively quickly and inexpensively, this technique is ideal for both prototype development and high-volume production runs.
Despite its many advantages, sand casting does come with some limitations. The surface finish of sand-cast parts is typically rougher compared to those produced by other methods such as die casting or investment casting. Additionally, while it can produce intricate designs, certain features may still be challenging or impossible to cast directly, necessitating additional machining.
In recent years, advancements in technology have further enhanced the sand casting process. Innovations in computer-aided design (CAD) and computer-aided manufacturing (CAM) have allowed for more precise patterns and molds, improving overall accuracy. The introduction of 3D printing in mold creation has also been a game-changer, facilitating rapid prototyping and reducing lead times significantly.
In conclusion, sand casting remains a fundamental and adaptable method for producing metal parts. Its balance between cost, versatility, and effectiveness ensures its continued relevance in modern manufacturing. As industries evolve, so too will the techniques and technologies that underpin sand casting, ensuring that this ancient art form continues to thrive in the contemporary world.
Post time:అక్టో . 11, 2024 14:13
Next:Golden Shores Enterprises Innovative Solutions for a Brighter Future