Understanding Sand Casting Costs Key Factors and Considerations
Sand casting is one of the oldest and most widely used metal casting processes, known for its versatility and cost-effectiveness. However, understanding the costs associated with sand casting is crucial for manufacturers and clients alike, as it can significantly impact overall project budgets. In this article, we will explore the various factors that contribute to sand casting costs and how they can be managed to achieve efficiency.
Material Costs
The primary component of sand casting is the sand itself, typically silica sand. The quality and type of sand used can influence the cost significantly. High-quality, fine-grain sand is essential for producing smooth, detailed castings, but it comes at a higher price. In addition to sand, metal costs also play a crucial role. The price of aluminum, iron, and bronze can fluctuate based on market conditions, affecting the overall cost of the casting process.
Tooling and Equipment
Tooling costs are another critical factor in sand casting expenses. Patterns, which are used to mold the sand, can be made from various materials like wood, metal, or plastic, each with different costs and durability. The complexity of the pattern also influences the cost; intricate designs may require more labor and expensive materials. Additionally, the machinery used for mixing and molding the sand, as well as for melting and pouring the metal, contributes to the overall expenses. Investment in efficient equipment can help reduce operating costs over time.
Labor Costs
Labor is a significant portion of the sand casting cost structure. Skilled labor is required for various stages of the casting process, including pattern making, molding, pouring, and finishing. Labor costs can fluctuate based on regional wage rates and the availability of skilled workers. Additionally, companies may incur overtime costs if production deadlines are tight. Finding a balance between quality labor and cost efficiency is essential for managing expenses effectively.
sand casting cost
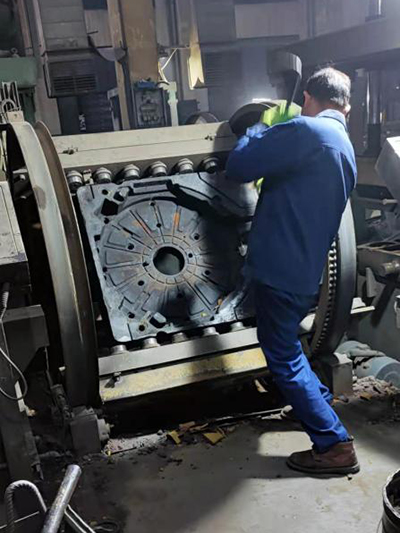
Production Volume
The scale of production is a vital consideration when evaluating sand casting costs. For small-scale production, initial setup and tooling costs can be relatively high per unit, making it less economical. However, as production volume increases, these costs can be spread out, leading to lower costs per unit. Businesses must assess their production needs carefully to determine the most cost-effective approach, whether it involves batch production or larger runs.
Waste Management
Efficient waste management also affects overall costs in sand casting. The sand used in the casting process can be recycled and reused, reducing material costs significantly. However, the quality of recycled sand must be maintained, which may require additional processing. Managing other waste materials, such as metal scrap, is also essential; recycling or reusing scrap metal can help offset some material costs.
Quality Control and Finishing
Quality control is imperative to ensure the final product meets specifications, but it can add to the overall costs. Thorough inspections and testing require additional time and resources. Furthermore, finishing processes such as machining, grinding, or surface treatment can increase the overall cost. While some manufacturers may seek to reduce finishing expenses, it's critical to find a balance that does not compromise quality.
Conclusion
In conclusion, the costs associated with sand casting encompass a wide range of factors, including materials, tooling, labor, production volume, and waste management. By understanding these elements, manufacturers can make informed decisions that balance quality and cost efficiency. Investing in quality materials and equipment while managing labor effectively can lead to successful outcomes in sand casting projects. Whether for small-scale prototypes or large-scale production, careful attention to these cost factors can ensure that businesses remain competitive while delivering high-quality castings.
Post time:సెప్టెం . 29, 2024 04:48
Next:Understanding Sand Casting Manufacturers for Quality Production and Innovation in Metal Components