Resin Sand Casting Revolutionizing the Foundry Industry
In the world of metallurgy and manufacturing, the quest for efficient and high-quality casting processes has led to the development of various techniques. One such technique that has gained significant popularity is resin sand casting. This innovative method combines the traditional techniques of sand casting with the advantages of resin binders, resulting in precision and improved casting quality.
What is Resin Sand Casting?
Resin sand casting is a process that employs sand as a molding material, but instead of using water as a binder (as in traditional green sand casting), it utilizes a synthetic resin. This pliable and robust resin binds the sand particles together, allowing for the creation of molds that can withstand higher temperatures and provide better dimensional accuracy. The process begins with the preparation of a sand mixture that includes resin and a hardener. When the two components are mixed, a chemical reaction occurs that solidifies the sand grains into a strong and stable mold.
Advantages of Resin Sand Casting
One of the primary advantages of resin sand casting is its ability to produce intricate and complex shapes with exceptional surface finish. The fine granulation of resin-bonded sand allows for a more detailed reproduction of the original pattern, which is crucial when creating components with high aesthetic or functional requirements. Moreover, the surface roughness of the castings is greatly reduced compared to traditional sand casting methods, often eliminating the need for extensive machining and finishing processes.
Another significant advantage is the thermal stability of resin sand molds. These molds can endure higher temperatures, which is particularly beneficial for casting metals with higher melting points, such as steel and certain alloys. The improved dimensional stability of the molds minimizes the risk of defects such as warping or shrinking, which can occur in traditional casting methods.
Additionally, resin sand casting permits a faster turnaround time. The quick setting time of resin allows for expedited production, reducing overall cycle times. This leads to enhanced productivity and efficiency in a manufacturing environment, which is critical in today's fast-paced industrial landscape.
resin sand casting
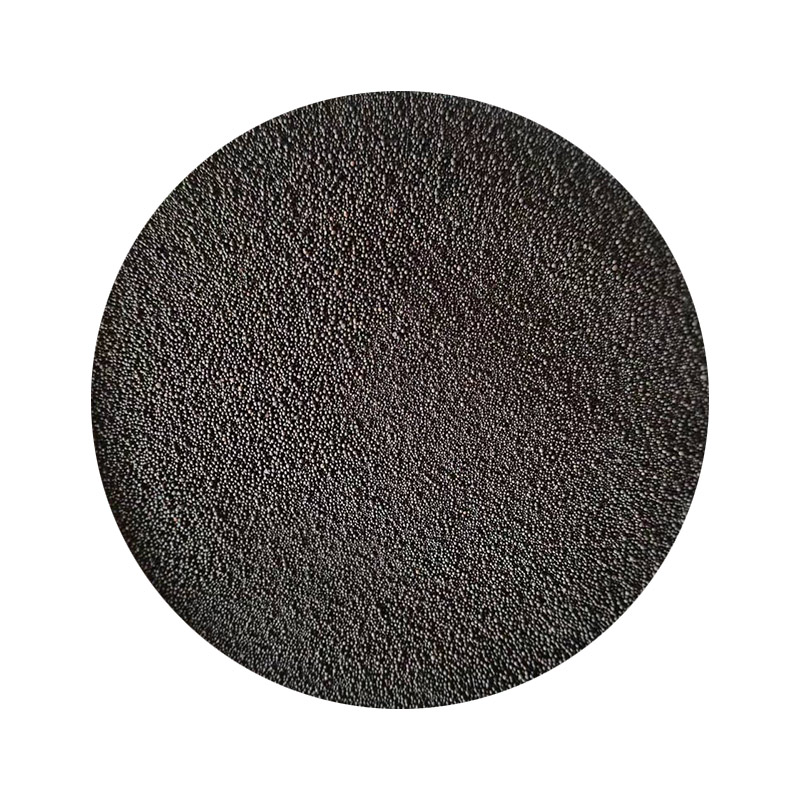
Applications of Resin Sand Casting
Resin sand casting has found a niche in various industries, including automotive, aerospace, and general engineering. In the automotive sector, it is commonly used to manufacture engine components, housings, and intricate parts that require both strength and precision. The aerospace industry also benefits from resin sand casting, where lightweight yet robust components are essential for performance and safety.
Furthermore, the method is used for producing artistic sculptures and architectural elements due to its ability to capture fine details and textures. The versatility of resin sand casting makes it a favored choice for both high-volume production runs and custom one-off applications.
Environmental Considerations
With the growing emphasis on sustainability, resin sand casting also offers an advantage in terms of environmental impact. Many modern resins are developed to be less harmful and more eco-friendly, and the use of such materials aligns with the global trend towards sustainable manufacturing practices. Additionally, the casting process can generate less waste compared to traditional methods, as sand can often be reused multiple times in the casting cycle, further promoting resource conservation.
Conclusion
In conclusion, resin sand casting represents a significant advancement in the field of foundry technology. Its ability to produce high-quality castings with intricate details and improved surface finishes has made it a preferred method for various industries. As manufacturers continue to seek methods that enhance efficiency and reduce costs, resin sand casting is poised to play an integral role in shaping the future of metal casting. As technology evolves and environmental standards rise, this process will likely continue to adapt, offering even more benefits to manufacturers and consumers alike.
Post time:డిసెం . 02, 2024 04:56
Next:Understanding the Process and Benefits of Sand Casting in Metal Manufacturing