Resin coated sand is a crucial material in the foundry industry, primarily used for the production of high-quality metal castings. It involves the application of resin coatings to traditional sand, enhancing its properties to produce superior casting results. This article outlines the specification of resin coated sand, its benefits, and its applications in various industries.
The primary component of resin coated sand is silica sand, which is selected for its excellent thermal stability, high resistance to thermal shock, and ability to withstand high temperatures during the casting process. The sand grains are coated with a thermosetting resin, typically phenolic or urethane resin, which binds the grains together and provides additional strength. The coating process usually occurs in a mixing machine, where sand and resin are combined, often along with additives such as catalysts, hardeners, and plasticizers to optimize performance.
One of the key specifications of resin coated sand is its thickness of the coating. The resin layer must be uniformly applied to ensure optimal performance. Generally, a coating thickness between 1-2% by weight of the sand is considered ideal. This amount provides adequate binding without negatively affecting the sand’s ability to flow and fill molds.
The moisture content in resin coated sand is another critical specification. The sand must be dry before the resin is applied to ensure proper coating. The recommended moisture content is typically less than 0.5%. High moisture levels can lead to improper curing of the resin, resulting in weak molds and defective castings.
resin coated sand specification
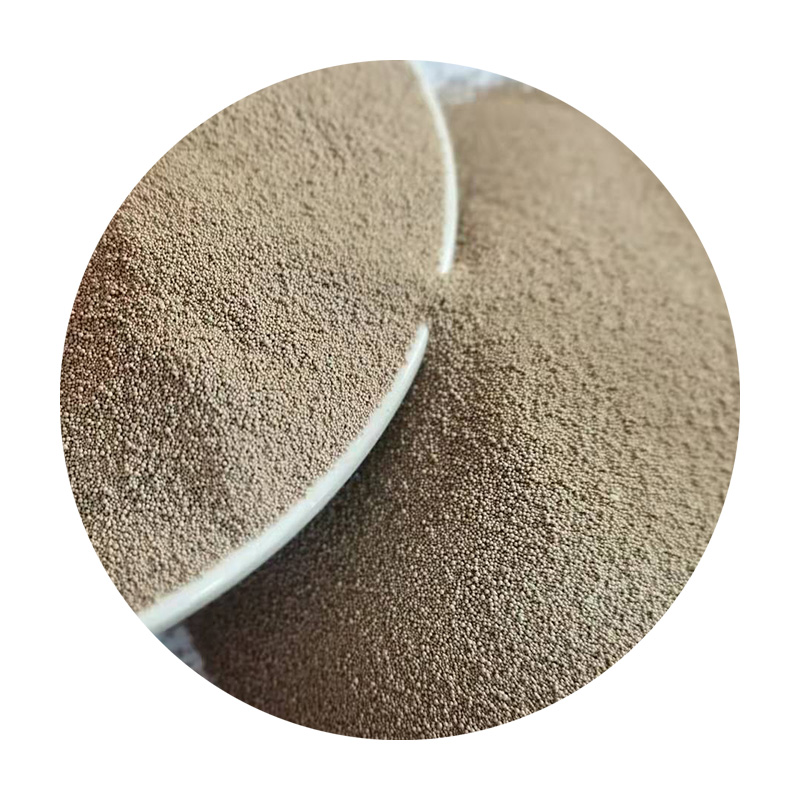
In terms of grain size, resin coated sand typically comes in various grades, allowing for flexibility in applications. Common grain sizes range from 50 to 150 mesh, which can be selected based on the specific requirements of the casting process. Finer grains provide high detail and a smooth surface finish, while coarser grains are advantageous for thicker sections and better flow.
The strength of the resin coated sand, measured in terms of its green strength (the strength of the mold before it is heated) and its baked strength (after it is cured), is an essential specification for ensuring high-quality castings. High green strength allows for easier handling of molds, while baked strength is crucial for maintaining the integrity of the mold during the metal pouring process. Specifications often require that green strength be above 4 psi and baked strength exceed 35 psi.
Temperature resistance is another vital aspect to consider. Resin coated sand can withstand pouring temperatures upwards of 2000°F (1093°C), making it suitable for various metals, including aluminum, iron, and steel. This high thermal stability minimizes defects such as burn-on and mold collapse, contributing to lower scrap rates and improved casting quality.
In summary, the specifications for resin coated sand encompass various critical properties, including coating thickness, moisture content, grain size, strength, and temperature resistance. Its enhanced properties make it a preferred choice in metal casting processes across multiple industries. As manufacturers continue to seek ways to improve casting quality and efficiency, the role of resin coated sand is set to expand further, reinforcing its significance in modern foundry practices.
Post time:నవం . 25, 2024 15:00
Next:sand casting foundries