An Overview of Rapid Sand Casting
Rapid sand casting is an innovative approach in the field of manufacturing that enhances the efficiency and speed of the traditional sand casting process. This method integrates advanced technologies, such as 3D printing and computer-aided design (CAD), to create molds with remarkable precision and speed. As industries face increasing demands for quicker production times and lower costs, rapid sand casting has emerged as a solution that meets these challenges effectively.
The Traditional Sand Casting Process
To understand rapid sand casting, it's essential to first comprehend traditional sand casting. This age-old technique involves creating a mold from sand, which is then filled with molten metal to form a desired part. Typically, the process includes creating a pattern, generating a mold, and pouring metal into the mold cavity, followed by cooling and finishing. While traditional sand casting is versatile and cost-effective for many applications, its reliance on manual labor and extensive setup time can be significant drawbacks, particularly for short production runs or custom parts.
The Evolution to Rapid Sand Casting
Rapid sand casting addresses the limitations of traditional methods by utilizing modern technologies to streamline various stages of production. One of the key innovations in this approach is the use of 3D printing to create sand molds directly from digital designs. This allows manufacturers to bypass the lengthy pattern-making phase, reducing lead times from weeks to mere hours. The 3D printing process enables intricate designs that may be difficult or impossible to achieve with conventional methods, which can lead to enhanced part performance and reduced weight.
Additionally, rapid sand casting can accommodate a wide range of materials, including aluminum, iron, and magnesium alloys. The ability to work with diverse alloys means that industries can customize the material properties of their cast parts to meet specific requirements, catering to the needs of various applications, from automotive components to aerospace parts.
rapid sand casting
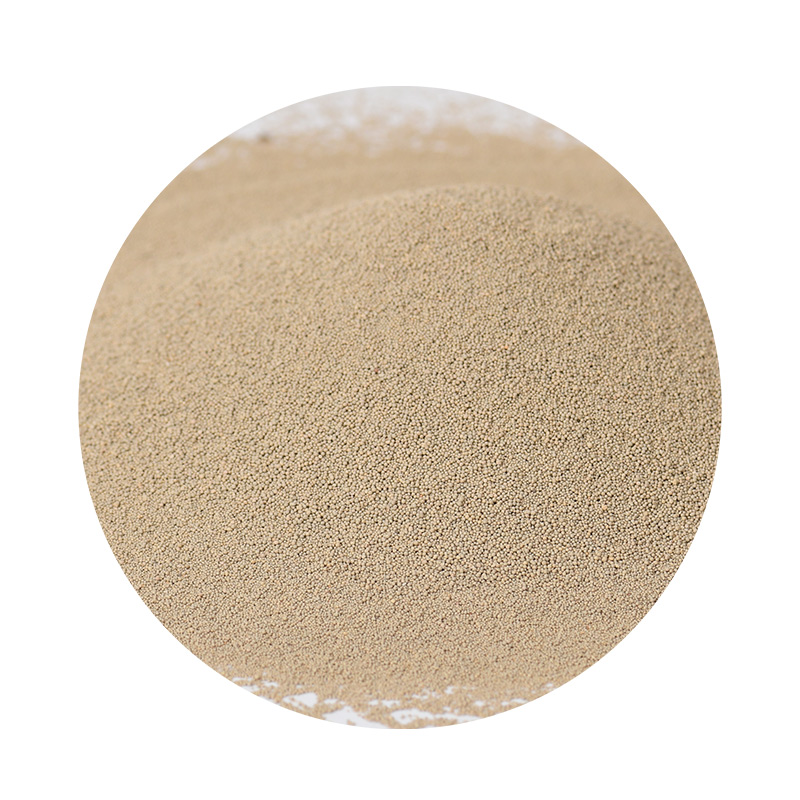
Benefits of Rapid Sand Casting
The benefits of rapid sand casting are manifold. Firstly, the reduced lead time significantly enhances a company’s ability to respond to market demands. In industries where product life cycles are short or customization is crucial, rapid sand casting allows for quick iterations and faster time-to-market. Secondly, the precision offered by 3D printed molds leads to fewer defects, which translates to lower scrap rates and reduced production costs.
Moreover, rapid sand casting supports sustainable manufacturing practices. The method inherently produces less waste compared to traditional processes, as 3D printing optimizes the material usage in mold creation. Additionally, the ability to produce small batches effectively encourages local manufacturing, reducing transportation emissions and supporting regional economies.
Challenges and Future Prospects
Despite its numerous advantages, rapid sand casting is not without challenges. The initial investment in 3D printing technology and training can be substantial, and the technology is continually evolving, requiring manufacturers to stay updated with advancements. Furthermore, while rapid sand casting excels in producing complex geometries, it may still face limitations in the scale of production compared to traditional casting methods.
Looking ahead, the future of rapid sand casting is promising. As technology continues to improve, integrating artificial intelligence (AI) and machine learning into design and production processes could further optimize efficiency and customization. The expansion of materials used in rapid sand casting will likely enable even more applications across various industries, reinforcing its place as a modern manufacturing solution.
In conclusion, rapid sand casting represents a significant evolution in the field of manufacturing, combining the time-tested method of sand casting with cutting-edge technology. By reducing lead times, enhancing design possibilities, and promoting sustainable practices, it stands as a vital approach for businesses striving to keep pace in a fast-evolving market landscape. As this technology continues to develop, it will undoubtedly shape the future of casting and manufacturing for years to come.
Post time:నవం . 28, 2024 00:23
Next:A Comprehensive Guide to Sand Casting Techniques and Best Practices