Precision Sand Casting An Overview
Precision sand casting is a vital manufacturing process that combines the age-old technique of sand casting with modern advancements to produce high-quality metal components. This method is extensively employed in various industries, including automotive, aerospace, and engineering, due to its cost-effectiveness, versatility, and ability to create complex geometries.
What is Sand Casting?
Sand casting, also known as sand mold casting, is a metal casting process characterized by using sand as the mold material. In this process, a pattern made of metal, plastic, or wood is placed in a molding box, and sand is subsequently packed around it to create a mold. Once the pattern is removed, a cavity remains in the shape of the component desired. Molten metal is poured into this cavity to solidify and form the final product.
The Precision Aspect
While traditional sand casting methods are effective, precision sand casting takes this technique to another level. By incorporating modern technology and careful engineering, precision sand casting aims to achieve tighter tolerances and superior surface finishes. This is essential in industries where the functionality of a part is critical, and even the slightest deviation can lead to performance issues.
Advantages of Precision Sand Casting
1. Complex Geometries Precision sand casting allows for the creation of complex shapes that would be difficult or impossible to achieve with other manufacturing methods. This capability significantly expands design possibilities for engineers and designers.
2. Material Versatility This casting process can accommodate a wide range of materials, including aluminum, iron, and bronze. This flexibility makes it suitable for producing components with specific material properties tailored to their applications.
3. Cost-Effectiveness Compared to other precision machining processes, precision sand casting can be more economical, especially for high-volume production runs. The reusable nature of sand molds reduces material costs, and the process can be scaled effectively.
4. Enhanced Surface Finish Modern techniques, including the use of advanced sand types and additives, allow for improved surface finishes in precision sand casting. This is crucial for applications where aesthetics and surface quality are essential.
5. Short Lead Times The capacity to quickly create patterns and molds means that manufacturers can respond to market demands swiftly, reducing lead times and optimizing production schedules.
precision sand casting
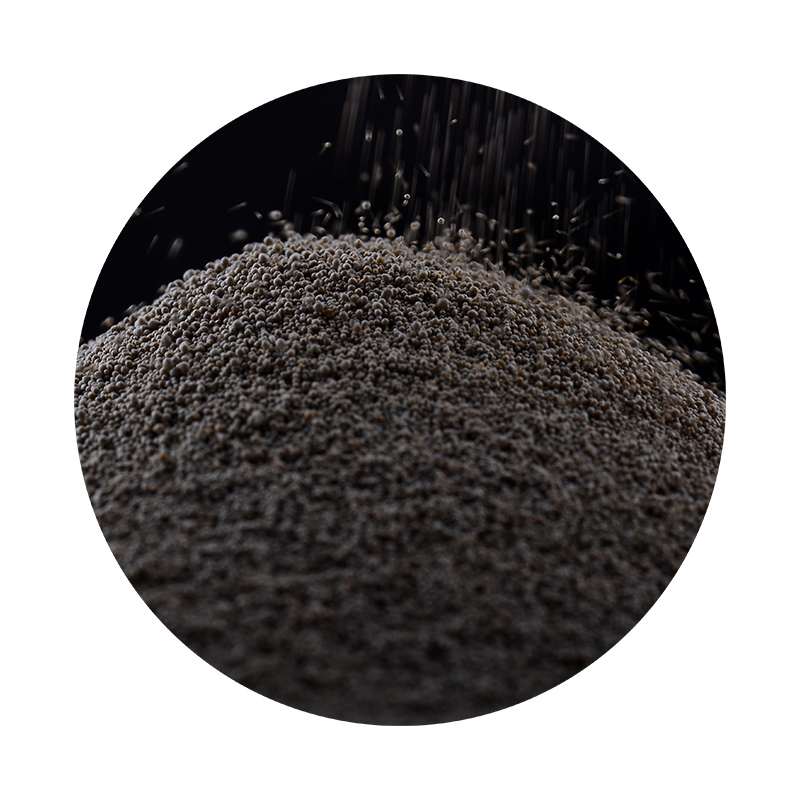
The Precision Sand Casting Process
The precision sand casting process generally involves several key stages
1. Pattern Making A precise pattern is created, often using computer-aided design (CAD) software, to ensure that it accurately represents the final product. Patterns can be made from various materials depending on the complexity and number of parts needed.
2. Mold Creation The pattern is then used to create a sand mold. This often involves high-quality silica sand mixed with clay and moisture or resin-bonded sand to enhance durability and precision.
3. Pouring Once the mold is prepared, molten metal is poured into the cavity. The temperature and composition of the metal are closely monitored to ensure the desired properties of the finished part.
4. Cooling and Removal After the metal has cooled and solidified, the sand mold is broken away to reveal the cast part.
5. Finishing Additional machining processes may be employed to achieve the exact specifications required for the application. This final finishing is crucial for achieving the needed tolerances and surface quality.
Applications of Precision Sand Casting
The applications of precision sand casting are vast. In the automotive industry, it is used to manufacture engine blocks, transmission housings, and various other components that require precise dimensions and robust performance. In aerospace, it serves critical components like turbine blades which demand high levels of precision and material integrity. Beyond these, the process is also employed in producing intricate parts for industrial machinery, consumer goods, and art.
Conclusion
In conclusion, precision sand casting represents a fusion of traditional techniques and modern technology, providing manufacturers with a versatile, cost-effective, and precise method for creating complex metal components. As industries continue to evolve and demand higher efficiency and quality, the importance of precision sand casting in meeting these challenges cannot be overstated. Whether it's for automotive, aerospace, or any other industry, precision sand casting offers the reliability and versatility required in today’s manufacturing landscape.
Post time:డిసెం . 16, 2024 02:15
Next:Tips for Sanding Resin 3D Prints for a Smooth Finish