Understanding the Parts of Sand Casting
Sand casting is one of the oldest and most widely used metal casting processes. It involves creating a mold from a mixture of sand and a bonding agent to form the desired shape of the final product. Sand casting has several advantages, including its ability to produce complex shapes and its suitability for both small and large production runs. This article provides a detailed overview of the key components and processes involved in sand casting.
1. Patterns
The first and foremost part of sand casting is the pattern. The pattern is a replica of the final product that is made from materials such as wood, metal, or plastic. Patterns are typically created with slight enlargements to accommodate the shrinkage that occurs in metals as they cool and solidify. There are various types of patterns, including solid patterns, skeleton patterns, and split patterns, each serving different purposes and designs. The pattern is essential as it determines the shape and dimensions of the mold that will be created in the sand.
2. Molding Sand
Molding sand is a mixture that forms the mold cavity. The composition of sand is crucial, as it must provide the right balance of strength and permeability. The primary component is silica sand, which is mixed with clay and water to create a cohesive yet workable layer. The sand must be capable of retaining its shape under the weight of the molten metal while also allowing gases to escape during pouring. Different types of molding sands, such as green sand, dry sand, and no-bake sand, are used depending on the requirements of the casting process.
3. Core
In many sand casting applications, cores are used to create internal cavities or holes in the final product. Cores are typically made from a similar sand mixture and are inserted into the mold before pouring the metal. They help define the shape internally and can also be used to increase structural integrity in the finished casting. Core boxes are employed to shape the core material before it is placed in the mold.
parts of sand casting
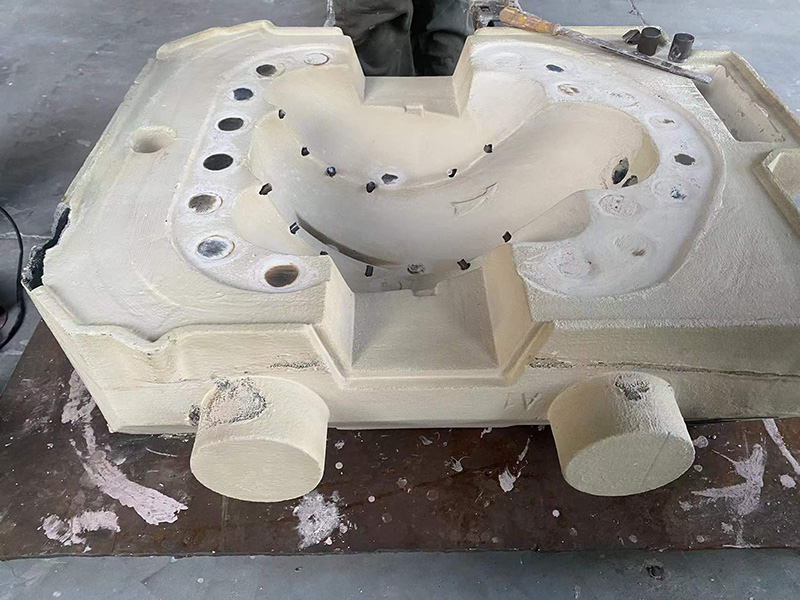
4. Mold
The mold is created by packing the molding sand around the pattern, after which the pattern is removed, leaving behind a cavity in the shape of the desired part. The two halves of the mold, often known as the cope (top) and drag (bottom), are secured together to ensure they do not separate during the pouring process. The mold design must take into account aspects such as gating (the channels through which the molten metal enters the mold), risers (which allow for extra metal to fill the cavity as it cools), and vents (which lets gases escape).
5. Pouring
Pouring is the next critical step in sand casting. The molten metal, which is prepared in a furnace, is carefully poured into the mold cavity. The pouring temperature must be high enough to allow the metal to flow smoothly but not so high that it causes defects in the final casting. Controlling the pouring speed and technique is vital as it helps prevent turbulence and ensures that the metal fills the mold completely.
6. Cooling and Finishing
Once poured, the molten metal is left to cool and solidify. The cooling time varies based on the material and thickness of the casting. After the metal has cooled sufficiently, the mold is broken away to reveal the casting. The casting may require further finishing processes, such as grinding, machining, or sandblasting, to achieve the desired surface finish and dimensional accuracy.
In conclusion, sand casting is a versatile and efficient method for producing metal parts. Understanding its key components—patterns, molding sand, cores, molds, pouring techniques, and post-casting operations—is essential for achieving high-quality results. With its widespread application across various industries, mastery of the sand casting process is invaluable for manufacturing and engineering professionals.
Post time:డిసెం . 12, 2024 12:51
Next:Essential Components of the Sand Casting Process Explained in Detail