Making Foundry Sand An Essential Process in Casting
Foundry sand plays a critical role in the metal casting industry, serving as a key material in the production of metal castings. The process of making foundry sand involves several steps and considerations that ensure high-quality casting outcomes. This article explores the significance of foundry sand, its composition, the production process, and its applications in casting.
The Importance of Foundry Sand
Foundry sand is primarily composed of silica, which is known for its thermal stability and ability to withstand high temperatures. This makes it an ideal medium for creating molds that hold molten metal during the casting process. The quality of foundry sand directly influences the final product, impacting its dimensional accuracy, surface finish, and overall integrity. The right type of foundry sand can reduce defects such as gas porosity and ensure smoother production cycles.
Composition of Foundry Sand
The primary component of foundry sand is high-purity silica, typically sourced from natural sand deposits or produced synthetically. The ideal grain size and shape of the sand particles play a crucial role in determining the sand’s performance as a mold material. Generally, foundry sand should have a consistent grain size and be well-rounded, which aids in the flow of the sand particles and provides better packing density. Additionally, additives such as clay, binder, and moisture may be included in the formulation to enhance the properties of the sand, such as strength and permeability.
The Production Process
Making foundry sand is a precise process that begins with the selection of the raw materials. Initially, high-purity silica sand is mined and then cleaned to remove impurities such as clay, silt, and organic materials. This purification process often involves washing, screening, and drying the sand to achieve the desired quality.
making foundry sand
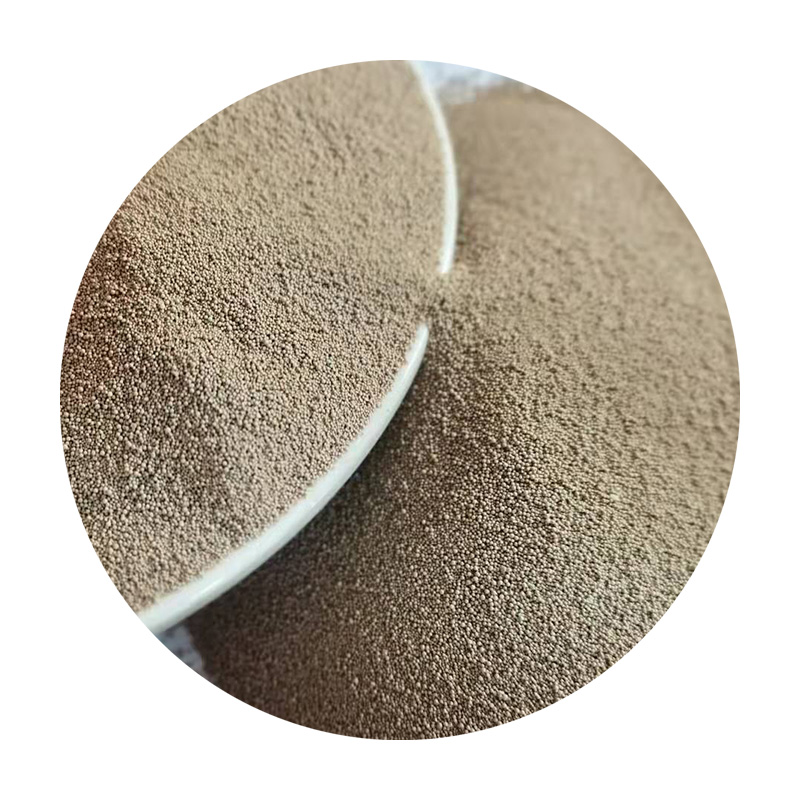
Once the sand is prepared, it may be treated with bonding agents to improve its structural integrity. Common binders include bentonite clay, which enhances the sand’s cohesion and allows it to retain its shape when creating molds. In addition, water is added in controlled amounts to activate the bonding agents, ensuring optimal performance.
After mixing, the sand is usually tested for key properties such as compressive strength, permeability, and cohesiveness. Molding sands must have an appropriate balance between strength and flexibility to ensure that they can support the weight of the metal while allowing for easy removal of the cast product once solidified.
Applications in Casting
Foundry sand is used in various casting methods, including green sand casting, where moisture-laden sand is utilized, and resin-bonded casting, which employs synthetic resins as binders. Each method has its distinct advantages and applications based on the specific requirements of the casting process.
Green sand casting is favored for its cost-effectiveness and versatility, making it suitable for a wide range of applications, from automotive parts to architectural components. On the other hand, resin-bonded sands are used for precision castings that require tighter tolerances and superior surface finishes.
Moreover, with advancements in technology, the recycling of foundry sand has gained prominence. Used foundry sand can be reclaimed and treated for reuse, offering a sustainable solution that reduces waste and minimizes the environmental impact of sand extraction.
Conclusion
In conclusion, the process of making foundry sand is fundamental to the metal casting industry. By understanding the composition, production methods, and applications of foundry sand, manufacturers can optimize their casting processes and improve the quality of their products. As sustainability becomes increasingly important, the ability to recycle foundry sand will play a vital role in shaping the future of casting operations.
Post time:అక్టో . 21, 2024 03:17
Next:Understanding the Sand Casting Foundry Process for Efficient Metal Casting