Industrial Sand Casting A Versatile Manufacturing Process
Industrial sand casting is a widely used manufacturing process that involves pouring molten metal into a mold made of sand to create complex and geometrically intricate components. This method has been employed for centuries and continues to be a fundamental technique in various industries due to its versatility, cost-effectiveness, and ability to produce large quantities of parts.
The Basics of Sand Casting
The sand casting process begins with the creation of a mold, typically composed of fine silica sand, which is mixed with a binding agent to help hold the shape. The mold consists of two halves, known as the cope and the drag. The pattern, usually made of metal, plastic, or wood, is placed in the sand to create a cavity that will form the desired shape. Once the pattern is removed, the two halves of the mold are assembled, and molten metal is poured into the cavity.
After the metal has cooled and solidified, the mold is broken apart to reveal the cast part. The sand used in this process can often be reused, making sand casting an environmentally friendly option. The ability to produce a wide range of shapes and sizes makes sand casting a preferred choice for industries such as automotive, aerospace, and construction.
Advantages of Sand Casting
One of the primary advantages of sand casting is its adaptability to various metal types. Whether it’s aluminum, bronze, iron, or steel, sand casting can accommodate different materials, allowing manufacturers to select the best metal for the specific application. Moreover, it can produce parts of considerable size, ranging from small components to large industrial pieces weighing hundreds of pounds.
The process of sand casting also allows for intricate designs and complex geometries. Because the molds can be tailored to specific requirements, engineers and designers have the flexibility to create innovative components without the constraints often associated with other manufacturing methods. This capability is particularly advantageous in industries where specialized parts are required.
industrial sand casting
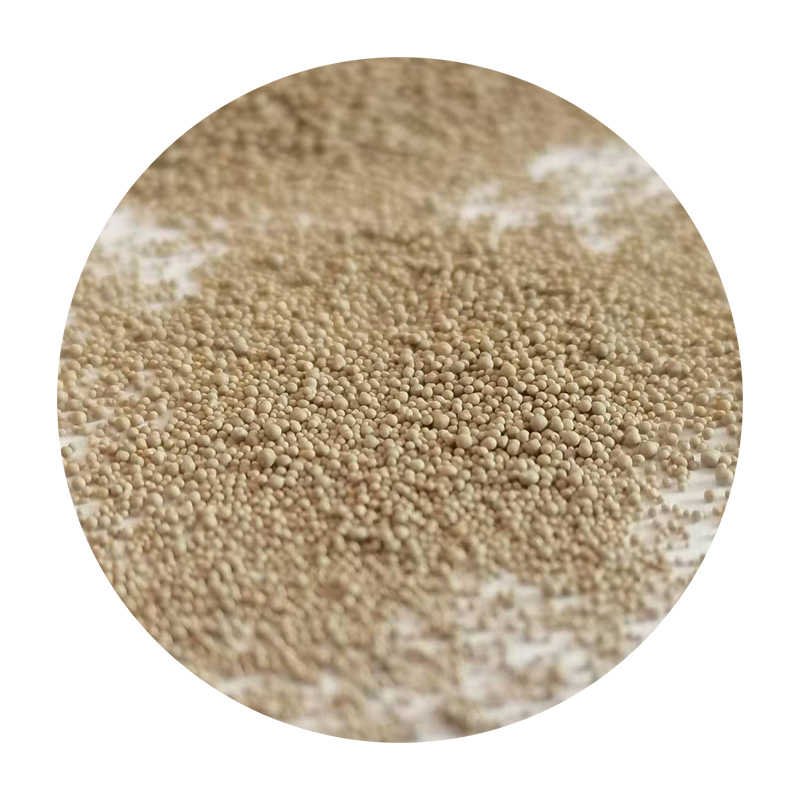
Cost-Effectiveness and Efficiency
Sand casting is often more cost-effective than other manufacturing processes, especially for small to medium production runs. The tooling costs for sand casting are generally lower than for other methods, such as precision casting or machining, making it an ideal option for startups and companies looking to minimize initial investments. Additionally, the materials needed for creating molds are relatively inexpensive, further contributing to cost savings.
In terms of efficiency, modern industrial sand casting techniques have benefitted from advancements in technology. Automated processes and computer numerical control (CNC) machines have streamlined the mold-making process, reducing production times and increasing consistency. Additionally, using 3D printing technology for patterns and cores has transformed sand casting, allowing for rapid prototyping and the possibility of highly customized solutions.
Environmental Considerations
As industries become more eco-conscious, sand casting holds its own regarding sustainability. The sand used in the process is abundant and can be recycled multiple times, minimizing waste. The ability to melt and reuse scrap metal also contributes to a decrease in material consumption and energy use.
However, it is essential for foundries to implement best practices to manage other environmental impacts, such as emissions and waste generation. Many companies are adopting environmentally friendly practices, including the use of green sand, which uses organic binders instead of traditional chemical binders, reducing harmful emissions.
Conclusion
Industrial sand casting remains a cornerstone of manufacturing across various sectors due to its versatility, cost-effectiveness, and ability to produce high-quality parts. With continued advancements in technology and a growing focus on sustainability, sand casting is well-positioned to remain relevant in the ever-evolving industrial landscape. As manufacturers seek innovative solutions to meet the demands of modern production, sand casting will undoubtedly adapt and continue to play a significant role in shaping the future of manufacturing. Whether for small components or large industrial applications, the sand casting process offers a reliable and efficient pathway for producing durable and intricate metal parts.
Post time:నవం . 20, 2024 15:39
Next:sand used for sand casting