How Does Sand Casting Work?
Sand casting, one of the oldest and most widely used metal casting processes, involves creating metal parts by pouring molten metal into a sand mold. This technique is favored for its versatility and cost-effectiveness, making it an essential method in various industries, from automotive to aerospace.
The sand casting process begins with the creation of a mold. The mold is typically made from a mixture of sand, clay, and water, known as molding sand. The sand provides the bulk material, while clay acts as a binder to hold the particles together. The water aids in activating the clay and helps in achieving the desired consistency of the sand mixture.
How Does Sand Casting Work?
To ensure proper metal flow and minimize defects, the mold is usually constructed in two halves—known as the cope and the drag. The cope is the top half, while the drag is the bottom half of the mold. They are then assembled, ensuring that they fit tightly together to prevent the molten metal from leaking out during the pouring process.
how does sand casting work
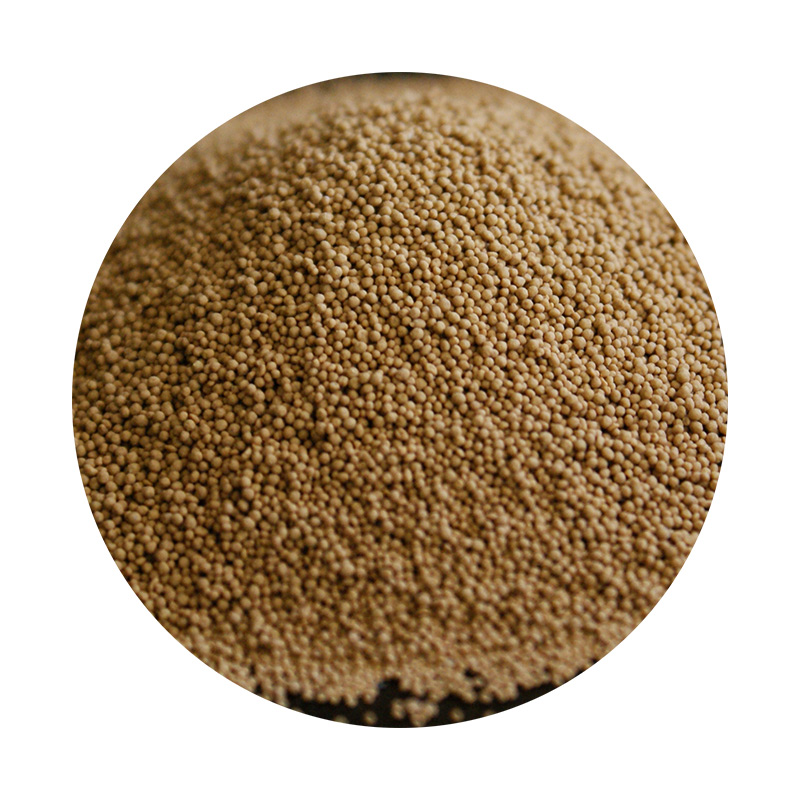
Before pouring the molten metal, several considerations are taken into account. These include the type of metal being used, the pouring temperature, and the cooling rate, all of which can significantly influence the mechanical properties of the final casting. Common metals used in sand casting include aluminum, iron, and bronze due to their favorable melting points and flow characteristics.
Once the preparations are complete, molten metal is poured into the mold cavity through a pouring basin. Gravity typically aids in this process, allowing the metal to flow into all parts of the mold. After pouring, the metal is left to cool and solidify, forming the desired shape. This cooling period can vary based on the thickness and type of metal, and it usually takes a few minutes to several hours.
Once the metal has fully cooled and solidified, the mold is broken apart, and the casting is removed. The resulting part often requires cleaning to remove excess sand and any surface imperfections that may have occurred during the casting process. Techniques such as shot blasting, grinding, or machining are commonly employed to achieve the desired surface finish and dimensions.
Finally, inspections and tests may be performed to ensure that the casting meets the required specifications and quality standards. This may involve examining the part for defects such as cracks or air pockets, which can affect its performance and longevity.
In conclusion, sand casting is a straightforward yet effective method for producing a wide range of metal parts. Its simplicity, low cost, and ability to create complex shapes make it a popular choice in various manufacturing sectors. As industries continue to evolve, sand casting remains a fundamental process that accommodates both traditional and modern engineering challenges.
Post time:సెప్టెం . 08, 2024 05:43
Next:Quality Sand Casting Supplier | Precision Sand Castings