Foundry Sands Essential Material in Metal Casting
Foundry sands are an integral component in the metal casting industry, providing a crucial medium for the creation of metal parts and components. These sands, primarily composed of silica, serve as a mold material that allows molten metal to take the shape of intricate designs and specifications. The quality and characteristics of foundry sands directly impact the efficiency and effectiveness of the casting process.
Types of Foundry Sands
There are various types of foundry sands used in the industry, each tailored to specific casting methods. The most common type is silica sand, known for its high melting point and thermal stability. Silica sand is usually mixed with resin or clay to improve binding properties and enhance mold strength. Other types include chromite sand, used for casting high-quality steel and iron products, and zircon sand, which is valued for its low thermal expansion and excellent dimensional accuracy.
The Role of Foundry Sands in Metal Casting
The primary function of foundry sand is to create molds that can withstand the exceptionally high temperatures of molten metal. In the sand casting process, a mold is formed by compacting sand around a pattern, which represents the final shape of the metal part. Once the mold is assembled, it is ready to receive the molten metal, which flows in and takes the shape of the cavity. After the metal cools, the sand mold is broken away to reveal the finished casting.
This process offers several advantages, including the ability to produce complex shapes and sizes with relative ease. Foundry sands also allow for efficient heat transfer, ensuring that the metal solidifies evenly, thus avoiding defects such as warping and shrinkage. Additionally, the reuse of sand from previous castings can contribute to cost savings and sustainability within the industry.
foundry sands
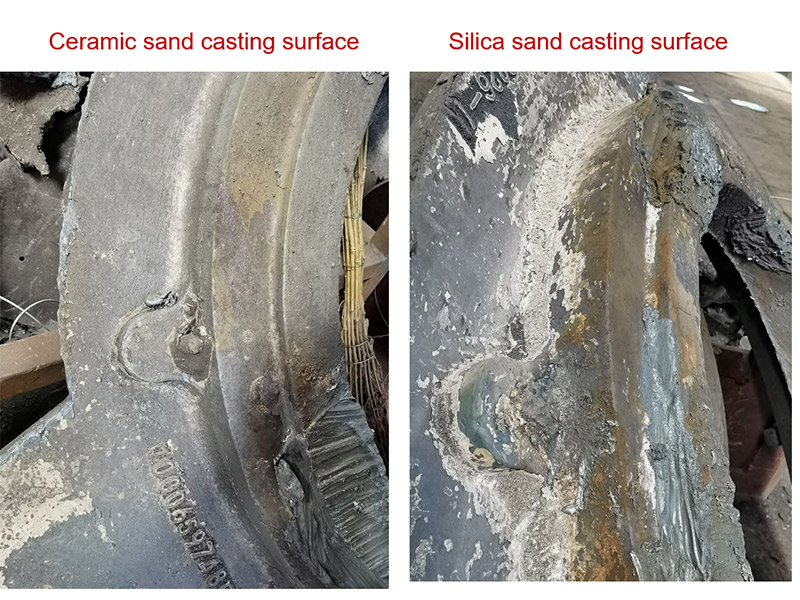
Environmental Considerations
With increasing awareness of environmental issues, the foundry industry has also been exploring more sustainable practices related to sand usage. Traditional foundry sands can be recycled, but the process can involve significant energy consumption and waste. Therefore, the development of synthetic sands has emerged as a viable alternative. These sands are engineered to provide improved performance, greater durability, and reduced environmental impact.
Furthermore, initiatives are underway to reclaim and recycle silica sand from used foundry molds. This not only alleviates the need for new sand extraction but also minimizes waste sent to landfills. Such practices help to create a more circular economy within the foundry sector.
Future Trends in Foundry Sands
The future of foundry sands is closely tied to advancements in technology. Innovations in 3D printing, for instance, are revolutionizing mold-making processes by allowing for the on-demand creation of molds without the need for traditional sand casting methods. This technology not only speeds up production times but also enables the creation of highly complex shapes that were previously difficult or impossible to achieve.
Moreover, ongoing research into alternative materials and sand composites may lead to the development of foundry sands that require less energy to produce and are more eco-friendly. As the industry continues to evolve, the need for effective, efficient, and sustainable materials will remain a priority.
In conclusion, foundry sands are a vital element of the metal casting process. Their unique properties and versatility make them indispensable for producing high-quality metal components. As environmental concerns grow and technology advances, the foundry industry will continue to adapt and innovate, ensuring that foundry sands remain relevant and effective in the years to come.
Post time:అక్టో . 09, 2024 05:09
Next:Understanding the Role of Sand in the Sand Casting Process