Different Types of Foundry Sand
Foundry sand is a key material used in the metal casting process, where it plays a vital role in producing high-quality metal parts. It provides the necessary support for molding metal components with precision and allows for the recycling of materials, resulting in significant cost savings and environmental benefits. There are various types of foundry sands designed for specific applications and castings, each with unique properties and uses. This article will explore the different types of foundry sands and their characteristics.
1. Silica Sand
Silica sand, often termed standard foundry sand, is one of the most commonly used types. It is primarily composed of silicon dioxide (SiO2) and is known for its ability to withstand high temperatures. Silica sand has excellent flowability, which helps in forming intricate mold shapes. Additionally, it exhibits good strength and resistance to thermal shock, making it suitable for both ferrous and non-ferrous metal casting. However, it does pose a health risk if inhaled in significant amounts, leading to respiratory issues, which is why appropriate safety measures are essential when handling it.
2. Olivine Sand
Olivine sand is a naturally occurring mineral that is primarily composed of magnesium iron silicate. Its advantages over silica sand include better thermal stability and lower expansion properties, which help reduce casting defects associated with sand expansion during the cooling process. Olivine sand is often used in applications where reduced mold distortion is critical, such as in the production of large castings. Moreover, it has excellent resistance to slag, making it especially suitable for steel foundries.
3. Zircon Sand
Zircon sand is derived from the mineral zircon and is prized for its high melting point and low thermal expansion. It exhibits excellent dimensional stability, which makes it suitable for producing complex geometries with tight tolerances. Zircon sand is less prone to chemical reactions with molten metal, allowing for cleaner casting surfaces. Its high cost compared to other sands often restricts its use to applications where precision and high-quality finishes are paramount, such as aerospace and automotive industries.
different types of foundry sand
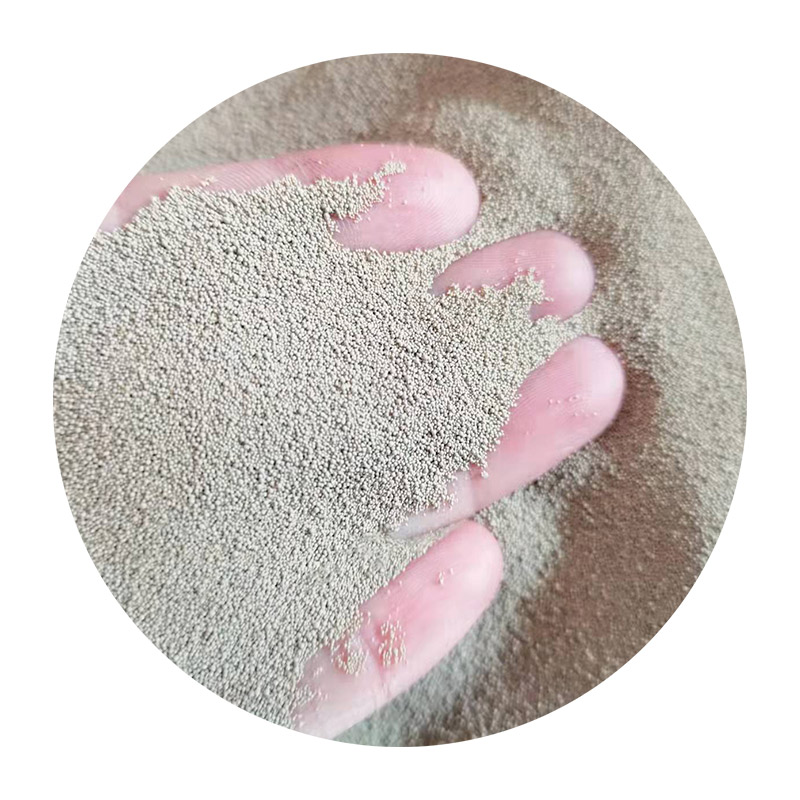
4. Chromite Sand
Chromite sand is composed primarily of chromium oxide and is used primarily for its high thermal stability and excellent resistance to metal penetration and erosion. This type of sand is particularly effective in casting high-quality steel and iron components. Chromite sand also helps to improve the strength and durability of molds and cores, reducing defects in the final product. Its unique properties make it a popular choice in industries requiring high-performance castings.
5. Resin-Coated Sand
Resin-coated sand is a special type of sand coated with a resin that hardens when heat is applied. This sand provides excellent dimensional accuracy and surface finish, making it ideal for complex geometries and intricate casting details. It is especially favored in the production of high-value components where surface quality and detail are critical. While the production process for resin-coated sand is more expensive, the resulting castings can significantly reduce finishing times and costs.
6. Green Sand
Green sand is a mixture of silica sand, clay, and water, and is the traditional molding sand used in foundries. The term green refers to the moisture content rather than the color. Green sand is known for its ability to hold shape and is relatively low-cost, making it an ideal choice for large-scale casting operations. However, its properties can vary widely depending on the specific clay and sand mixture used. While it has excellent compressive strength, it may not offer the same level of surface finish and detail as other types of foundry sands.
Conclusion
The choice of foundry sand greatly influences the quality and efficiency of the metal casting process. Each type of sand offers distinct advantages and disadvantages depending on the specific requirements of the casting project. By understanding the properties and applications of different foundry sands — from silica to chromite, olivine, zircon, and resin-coated sand — foundry operators can select the most suitable materials to enhance product quality while optimizing costs. With advancements in foundry technology, the future will likely see even more innovative solutions in sand materials, further improving the efficiency and sustainability of metal casting processes.
Post time:డిసెం . 15, 2024 10:13
Next:cerabeads sand