The Components of Sand Casting An Overview
Sand casting is one of the oldest and most versatile metal casting processes, widely utilized in manufacturing for its ability to create intricate and complex shapes. This method primarily relies on sand as the primary mold material due to its excellent properties, cost-effectiveness, and availability. To understand the sand casting process thoroughly, it is essential to delve into its core components, which play pivotal roles in achieving successful outcomes.
1. Mold
The mold is arguably the most critical component of the sand casting process. Typically made from a mixture of sand and a binder, molds can be created in various ways, including green sand, dry sand, and chemically bonded sand.
- Green Sand This is a mixture of silica sand, clay, and water. It's called green because it is used in its natural, damp state. Green sand molds are reusable and exhibit good permeability, allowing gases to escape during the casting process. - Dry Sand Dry sand molds are made with a more significant amount of binder and are cured before use. This type of mold provides higher strength and is often used for larger castings.
- Chemically Bonded Sand In this type, the sand grains are bonded using chemical reactions. These molds can withstand higher temperatures and complex geometries.
2. Pattern
The pattern is a replica of the final product that is used to create the mold cavity. Patterns can be made from various materials, including wood, metal, and plastic, depending on the durability required and the production volume. Patterns may also come with allowances for shrinkage, machining, and draft angles.
- Single Patterns These are used for simple designs and are often removed from the sand mold after it is formed.
- Match Plates This method utilizes two patterns on opposite sides of a plate, allowing for high-speed production and increased efficiency.
- Split Patterns A split pattern allows for complex shapes by being split into two or more parts for easier mold removal
.3. Core
Cores are used to create internal cavities and complex features within the casting. Typically made from a hardened sand mixture, they allow for greater flexibility in design and are placed within the mold before the metal is poured. Cores can be temporary or permanent based on the requirements of the casting.
components of sand casting
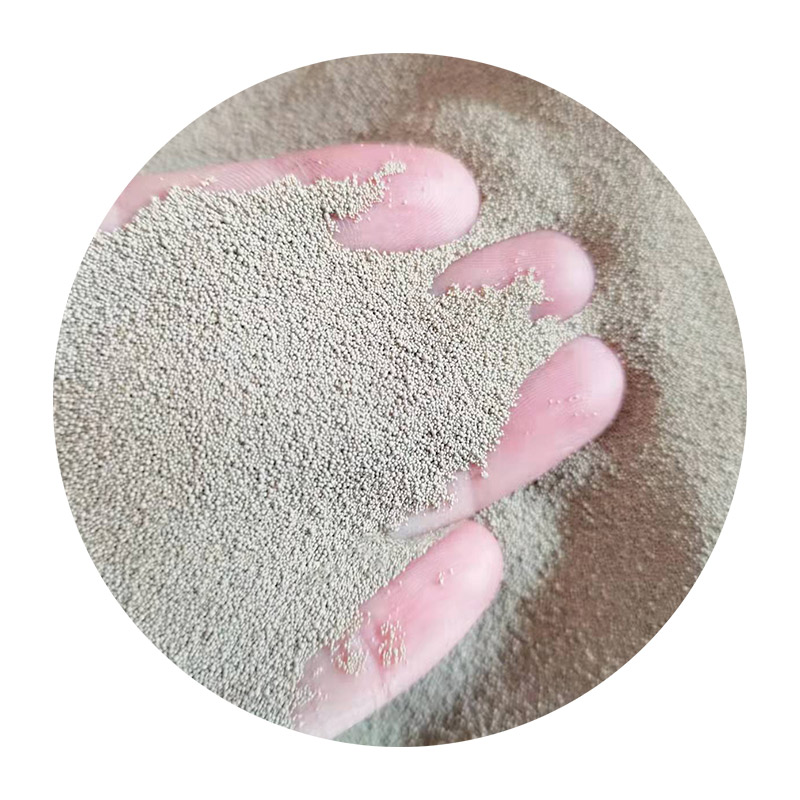
Using cores can significantly enhance the casting's integrity and reduce the overall weight by allowing hollow sections, thus opting for materials more wisely.
4. Binder
The binder is a crucial component that holds the sand grains together, providing strength to the mold. In green sand molds, bentonite clay serves this purpose, while chemically-bonded sands utilize synthetic resins that harden through a chemical reaction.
The choice of binder influences the mold's properties and the overall quality of the casting. Proper binder selection and mixing ratios ensure that molds maintain their shape during pouring and cooling processes.
5. Metal Alloy
The choice of metal alloy is critical in determining the characteristics of the final casting. Sand casting can accommodate a wide range of metals, including aluminum, iron, steel, and bronze. Each alloy comes with unique properties like melting point, fluidity, and mechanical strength, influencing the design and execution of the casting process.
6. Pouring System
The pouring system guides the molten metal into the mold cavity. This system typically includes a pouring cup, sprue, runner, and gates. The design and complexity of the pouring system can greatly affect the filling pattern and the quality of the casting. A well-designed pouring system minimizes turbulence, reduces porosity, and ensures a uniform fill.
7. Cooling and Finishing
After the molten metal is poured, it needs adequate time to cool and solidify. The cooling time depends on the metal type and the thickness of the casting. Once solidified, excess sand must be removed, and any surface imperfections can be polished or machined away. This process can involve several steps, including shot blasting, grinding, and painting, to achieve the desired finish.
Conclusion
In conclusion, the sand casting process is a multifaceted operation that depends on various components, each playing a vital role in producing high-quality castings. Understanding these components is essential for engineers, designers, and manufacturers looking to optimize the sand casting process for their specific needs. As technology continues to advance, the integration of new materials and techniques will likely enhance the capabilities of sand casting, making it an enduring choice for many industries.
Post time:డిసెం . 12, 2024 12:27
Next:components of sand casting