3D Sand Printing Casting A Revolutionary Approach to Metal Casting
In recent years, the manufacturing landscape has witnessed significant advancements, one of which is the emergence of 3D sand printing casting technology. This innovative method has revolutionized traditional sand casting processes, enabling manufacturers to produce intricate and high-quality metal castings with greater efficiency and precision. As industries strive for better productivity and reduced costs, 3D sand printing is becoming an increasingly viable solution for various applications in automotive, aerospace, and art.
Understanding 3D Sand Printing
3D sand printing is a layer-by-layer additive manufacturing process that uses sand to produce molds for metal casting. Unlike traditional methods that often involve labor-intensive and time-consuming pattern making, 3D sand printing offers a more streamlined approach. The process begins with a computer-aided design (CAD) model of the desired part, which is then sliced into layers by specialized software. A printer then deposits a binder onto the sand in the desired pattern, creating a mold layer by layer. Once completed, the mold is cured, and metal is poured into it to create the final casting.
Advantages of 3D Sand Printing Casting
1. Complex Geometries One of the standout benefits of 3D sand printing is its ability to produce complex geometries that are often impossible or prohibitively expensive to achieve with traditional methods. This capability allows engineers and designers to explore new designs, improve product functionality, and reduce weight without compromising performance.
2. Reduced Lead Times Traditional sand casting requires the creation of a physical pattern, which can take weeks or even months, especially for large or intricate parts. In contrast, 3D sand printing eliminates the need for these patterns and significantly reduces lead times. Manufacturers can go from design to production in a fraction of the time, giving them a competitive edge in fast-paced markets.
3. Material Efficiency 3D sand printing is inherently more material-efficient than traditional methods. It minimizes waste by using only the amount of sand needed to create the mold. Additionally, leftover sand can be reused in subsequent prints, promoting sustainability and reducing overall material costs.
3d sand printing casting
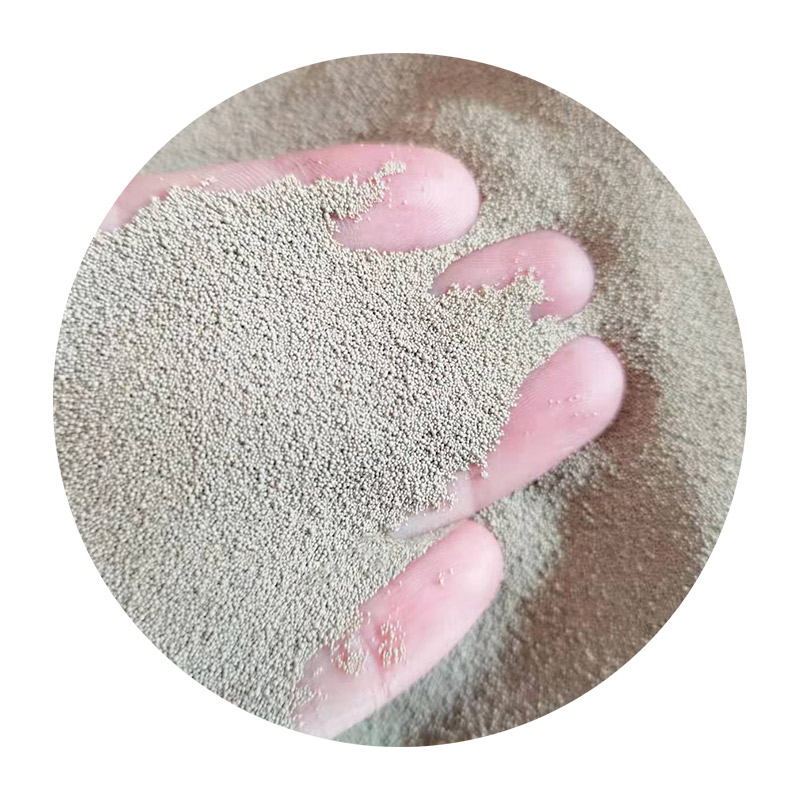
4. Customization The versatility of 3D sand printing allows for easy customization. Manufacturers can make quick adjustments to designs without the need for new tooling or molds. This flexibility is particularly beneficial for low-volume production runs or when producing specialized components tailored to specific customer requirements.
5. Cost Savings While the initial investment in 3D sand printing technology can be significant, the long-term cost savings are undeniable. Reduced lead times, material efficiency, and the elimination of complex pattern-making processes all contribute to lower overall production costs, making it a financially attractive option for many businesses.
Applications and Future Perspectives
The applications of 3D sand printing casting technology are broad and varied. In the automotive industry, for instance, manufacturers are using this technology to produce engine blocks, transmission housings, and other complex components. The aerospace sector also benefits, with companies leveraging 3D sand printing to create lightweight parts that meet stringent regulatory standards. Furthermore, artists and designers are exploring this technology for creating unique sculptures and intricate art pieces.
As the technology continues to evolve, we can expect even greater advancements, such as improved binder materials and faster printing processes. Additionally, with the increasing focus on sustainability and efficient resource usage, 3D sand printing is likely to gain traction as a key player in the quest for greener manufacturing practices.
Conclusion
3D sand printing casting represents one of the most promising advancements in manufacturing technology. By combining speed, efficiency, and design flexibility, it is paving the way for a new era in metal casting. As more industries adopt this innovative approach, the potential for enhanced product development and cost-effective manufacturing solutions will undoubtedly reshape the manufacturing landscape for years to come. Embracing this technology not only drives innovation but also positions businesses to meet the challenges of the future with confidence and agility.
Post time:అక్టో . 12, 2024 04:54
Next:Techniques for Smoothing Resin 3D Prints for a Flawless Finish