3D Sand Casting Revolutionizing the Foundry Industry
In recent years, the manufacturing landscape has witnessed a seismic shift thanks to advancements in technology. One of the most groundbreaking innovations is 3D sand casting, a technique that leverages additive manufacturing to enhance the efficiency and precision of traditional foundry processes. As industries demand higher-quality components with reduced lead times and costs, 3D sand casting stands out as a pivotal solution.
What is 3D Sand Casting?
3D sand casting is a process that uses 3D printing technology to create molds produced from sand. Unlike traditional sand casting, which relies on wooden or metal patterns to form the mold, 3D sand printing uses a digital approach. This enables foundries to produce complex geometries that would be impossible or extremely costly to create using conventional methods. By constructing molds layer by layer, manufacturers can achieve intricate designs, reduce material waste, and streamline the production cycle.
The Process
The fundamental process of 3D sand casting begins with creating a digital model of the component. This model is generated using computer-aided design (CAD) software, allowing for precise control over the dimensions and features of the part. Once the design is finalized, it is sliced into layers, which are then printed using a sand binder jetting technique or another 3D printing method. The printer deposits a thin layer of sand, which is then reinforced with a binding agent. This process is repeated until the mold is complete.
After the mold is printed, it is ready for the metal pouring phase. The melted metal is poured into the cavity created by the sand mold, where it solidifies into the desired shape. Once cool, the sand mold is broken away, revealing the final cast product.
Benefits of 3D Sand Casting
The advantages of 3D sand casting over traditional casting methods are numerous and impactful. Firstly, it significantly reduces lead times. The time required to produce molds often dictates the pace of manufacturing. With 3D sand casting, molds can be printed in hours rather than days or weeks, allowing for quicker turnarounds on projects. This agility is especially vital in industries where time-to-market can influence competitive advantage.
3d sand casting
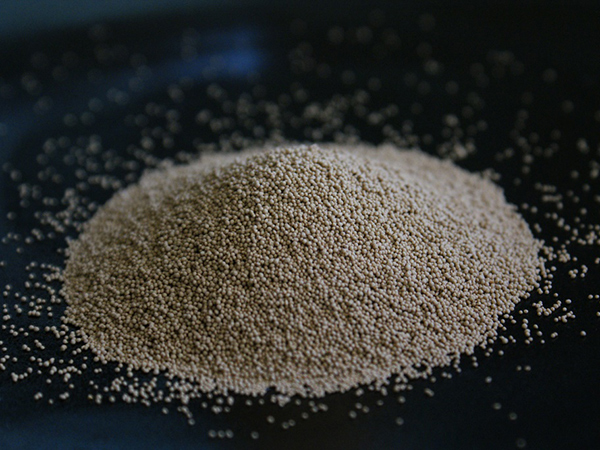
Secondly, there is a notable reduction in material waste. Traditional casting typically involves the creation of patterns, which are discarded after use, leading to wasted materials and labor. In contrast, 3D sand printing minimizes excess material, producing only what is necessary for the mold.
Another considerable advantage is design freedom. 3D sand casting accommodates complicated geometries that traditional casting methods struggle to achieve. This enables engineers and designers to push the boundaries of innovation, letting their creativity dictate design rather than manufacturing limitations.
Applications Across Industries
The implications of 3D sand casting extend across a variety of sectors, including automotive, aerospace, and artistic fields. In the automotive industry, for instance, manufacturers can quickly prototype and produce lightweight components that enhance vehicle efficiency. Similarly, aerospace applications benefit from the ability to produce intricate parts that contribute to fuel efficiency and overall performance.
Moreover, the artistic community is increasingly embracing 3D sand casting for custom sculptures and artistic creations, where unique shapes and designs are paramount. This fusion of art and technology not only showcases the versatility of 3D sand casting but also highlights its potential for cross-disciplinary innovation.
Challenges and Future Prospects
Despite its numerous benefits, 3D sand casting is not without challenges. The initial investment in technology can be substantial, and some foundries may struggle to adapt to the integration of digital manufacturing processes. Additionally, training personnel to operate advanced 3D printing equipment warrants time and resources.
Nevertheless, as technology continues to evolve and costs decrease, 3D sand casting is poised for widespread adoption. The future holds immense potential for further advancements in materials, printing speed, and process efficiency, leading to even greater innovations in the foundry industry.
In conclusion, 3D sand casting signifies a paradigm shift in manufacturing, offering enhanced efficiencies, design freedoms, and reduced waste. As industries increasingly recognize these advantages, the technique is set to redefine the standards of precision and innovation in metal casting processes. The journey of integrating this technology into mainstream manufacturing has just begun, and the possibilities are as limitless as the designs it can produce.
Post time:డిసెం . 12, 2024 14:09
Next:Best Sanding Methods for Resin Projects and Finishing Techniques