3D Printing for Sand Casting Revolutionizing Manufacturing
The manufacturing industry has seen significant transformations over the past few decades, with advancements in technology leading to the development of more efficient processes. One such innovation is the integration of 3D printing into the sand casting process, which has changed the game for manufacturers, engineers, and designers alike. The synergy of these two technologies combines the strengths of traditional casting methods with the versatility and precision of 3D printing, thus paving the way for new possibilities in metal casting.
Understanding Sand Casting
Sand casting is one of the oldest casting methods used for metal production. It involves creating a mold from a mixture of sand, clay, and water, into which molten metal is poured to create a desired shape. This method has long been favored for its ability to produce complex geometries and large parts. However, traditional sand casting has several limitations, including lengthy production times and high metal waste.
The Role of 3D Printing
3D printing, also known as additive manufacturing, offers a myriad of benefits, including rapid prototyping, design flexibility, and reduced waste. When applied to sand casting, 3D printing can be used to create molds and core components with incredible precision. This eliminates the need for traditional mold-making techniques, which can be time-consuming and labor-intensive.
One of the key advantages of using 3D printing for sand casting is its ability to quickly produce prototypes and complex designs that would be challenging or impossible to achieve with conventional methods. For example, intricate cooling channels and complex geometries can be easily integrated into the mold design, optimizing the casting process for better performance.
Enhanced Efficiency
3d printing for sand casting
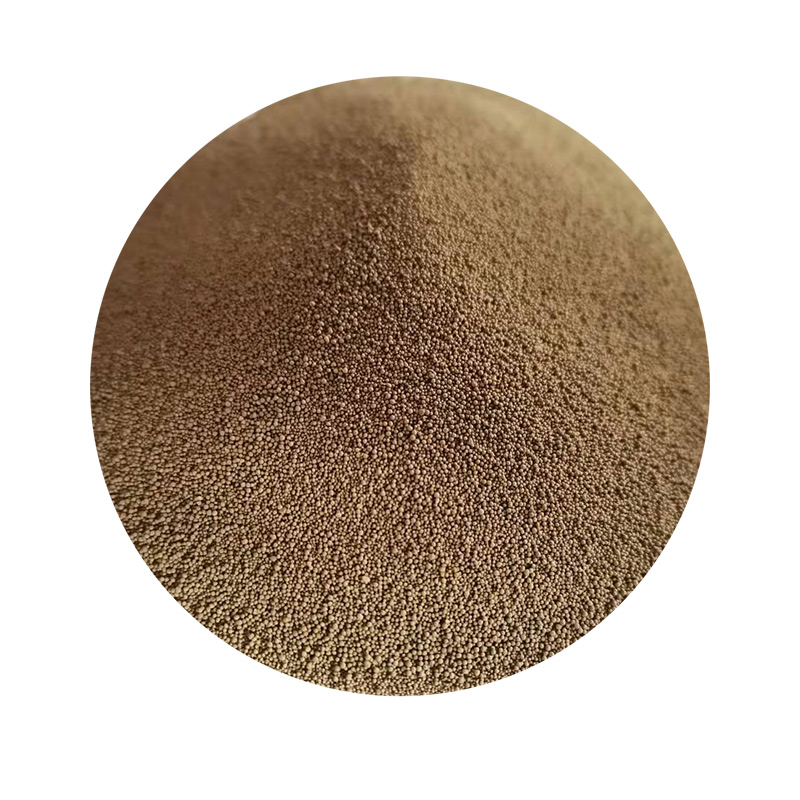
The combination of 3D printing and sand casting significantly improves overall efficiency. By reducing the lead time associated with mold creation, manufacturers can respond faster to market demands. This is particularly beneficial in industries where customization and quick turnaround are vital, such as aerospace, automotive, and even consumer goods.
Additionally, 3D printing allows for the use of new materials that may not be suitable for traditional sand casting. This opens the door for innovation in the types of products that can be produced, from lightweight components to heat-resistant parts. Manufacturers can experiment with different materials and designs without the fear of excessive waste or the high costs typically associated with traditional mold production.
Cost-Effectiveness
While the initial investment in 3D printing technology can be significant, the long-term savings it offers make it a worthwhile consideration for manufacturing operations. Traditional sand casting can involve high costs for tooling and mold production, especially for low-volume runs. In contrast, 3D printing reduces these costs through its ability to create molds on demand, thus decreasing both material waste and the need for extensive storage facilities for multiple molds.
Furthermore, the ability to reuse the sand for multiple casts through 3D printing processes can further enhance cost-efficiency. This sustainable approach not only reduces expenses but also aligns with global trends aimed at minimizing environmental impact.
Conclusion
The integration of 3D printing into sand casting represents a significant leap forward in manufacturing capabilities. It combines the strengths of two powerful technologies, offering enhanced precision, efficiency, and cost-effectiveness. As industries continue to evolve, the adoption of 3D printing for sand casting will likely become more prevalent, enabling manufacturers to produce complex components at a fraction of the time and cost.
In summary, 3D printing for sand casting is not merely a trend but a transformative approach that reinvents the way we think about manufacturing processes. By embracing this innovative combination, companies can vastly improve their production capabilities, ultimately leading to better products and satisfied customers. The future of manufacturing is undoubtedly bright, propelled by the incredible potential of 3D printing technology.
Post time:డిసెం . 15, 2024 16:03
Next:Exploring the Benefits of Sand and Resin Compositions in Modern Applications