The Types of Sand Used in Sand Casting
Sand casting is one of the oldest and most widely used metal casting processes, primarily because of its versatility and economical nature. In this process, sand is the primary material used to create molds into which molten metal is poured. The quality of the sand directly affects the final product's quality, which makes understanding the different types of sand essential for anyone involved in metal casting. In this article, we will explore the types of sand used in sand casting, with a focus on their properties and suitability for different applications.
1. Silica Sand
Silica sand, which consists of a high percentage of silicon dioxide (SiO2), is the most common type of sand used in sand casting. Its abundance, excellent thermal stability, and grain size make it suitable for casting processes. Silica sand can withstand high temperatures without undergoing significant deformation, ensuring that the mold retains its shape during casting. It is also relatively inexpensive, making it an ideal choice for large-scale production.
However, silica sand has some limitations. Its fine particles can lead to the formation of defects in the castings, such as thin sections or surface irregularities. Additionally, exposure to silica dust can pose health risks to workers, which has led to increased regulatory scrutiny in recent years.
2. Zircon Sand
Zircon sand, derived from the mineral zircon (ZrSiO4), is another option used in the sand casting process. It has a high melting point and excellent thermal stability, making it suitable for high-temperature applications. Zircon sand also exhibits low expansion, which helps maintain mold accuracy and dimensional stability.
Due to its high cost, zircon sand is typically used in more specialized applications, such as in the casting of high-precision components or in industries where quality and performance are critical
. Its resistance to chemical wear and ability to produce finer surface finishes make it a valuable asset in foundries.3. Chromite Sand
Chromite sand, composed primarily of chromium oxide (FeCr2O4), is used for casting ferrous alloys and non-ferrous alloys alike. One of its most significant advantages is its ability to withstand high temperatures without breaking down, making it an excellent choice for creating molds that need to endure the aggressive thermal and chemical environments often encountered in metal casting.
what type of sand is used for sand casting
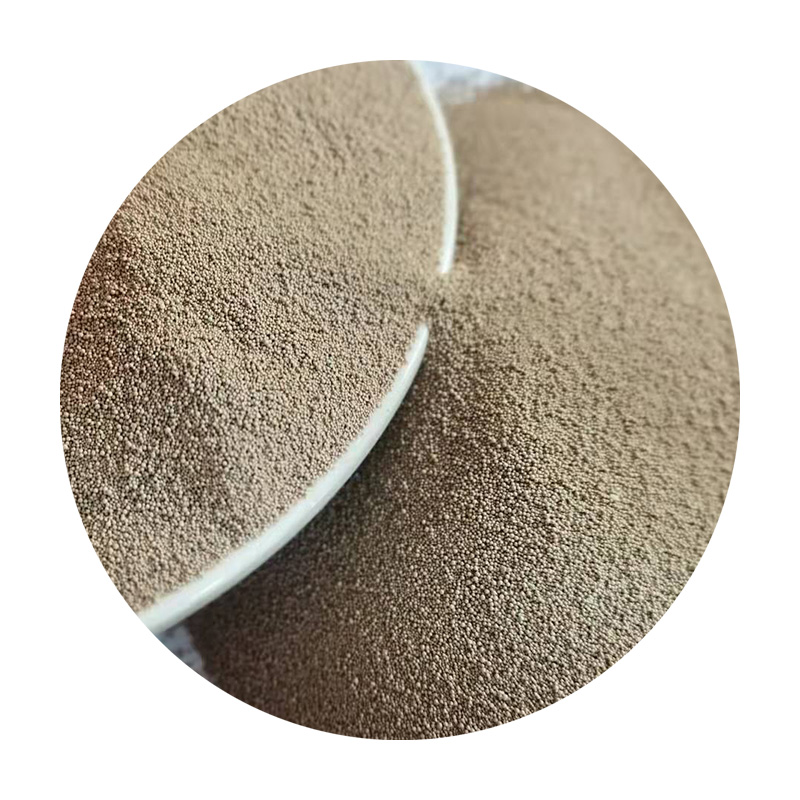
Additionally, chromite sand offers good resistance to metal penetration and casting defects, providing a smooth surface finish. However, like zircon sand, chromite sand tends to be more expensive than conventional silica sand, which limits its use mainly to specific high-performance applications.
4. Olivine Sand
Olivine sand, derived from the mineral forsterite, is another alternative in sand casting. Its composition includes magnesium iron silicate, giving it unique properties that make it a suitable choice for certain casting applications. Olivine sand has low thermal expansion, which contributes to high dimensional accuracy in the final product.
Its resistance to thermal shock and ability to handle high temperatures without breaking down make it ideal for heavy metal casting applications, including steel and alloy castings. Although olivine sand is less common than silica sand, it is gaining popularity in applications where dimensional control and surface quality are crucial.
5. Resin-Coated Sand
In addition to traditional sands, resin-coated sand has gained popularity in the casting industry. This material consists of natural sand grains that are coated with a phenolic resin. The resin bonds the sand particles, creating a strong and stable mold with excellent surface finish qualities.
Resin-coated sand is commonly used in applications that require high precision and intricate designs. It provides excellent performance in controlling dimensional tolerances and reducing imperfections in the final castings.
Conclusion
In summary, the type of sand used in sand casting plays a crucial role in determining the quality and performance of the final product. While silica sand remains the most prevalent choice due to its cost-effectiveness and availability, options such as zircon sand, chromite sand, olivine sand, and resin-coated sand cater to specific requirements based on performance, temperature resistance, and surface finish. Understanding these options allows foundries and manufacturers to choose the most suitable sand for their casting needs, ultimately affecting the efficiency and quality of the casting process.
Post time:டிசம்பர் . 12, 2024 18:31
Next:sand and polish resin