Steps in Sand Casting A Comprehensive Guide
Sand casting is a versatile and widely-used manufacturing process that allows for the production of complex parts and components across various industries, including automotive, aerospace, and machinery. This article outlines the key steps involved in the sand casting process, providing a clear understanding of its procedure and significance.
1. Pattern Making
The first step in the sand casting process is the creation of a pattern. A pattern is a replica of the final product, typically made from materials such as wood, metal, or plastic. Patterns are designed with slight allowances for shrinkage since metals contract as they cool. Depending on the complexity of the part, patterns can be either single-piece or multi-piece to facilitate easy removal from the sand mold.
2. Mold Making
Once the pattern is ready, the next step is mold making. The mold is constructed by packing sand around the pattern to create a cavity in the shape of the object. The sand mixture used is usually a combination of silica sand, clay, and moisture, which gives the mold its strength and shape. Once the sand is compacted around the pattern, the mold halves are separated, and the pattern is carefully removed, leaving a precise cavity for pouring the molten metal.
3. Core Making (if necessary)
For parts with internal cavities, a core must be created. Cores are made of a similar sand mixture and are inserted into the mold cavity before pouring the metal. This step is essential for producing complex geometries that cannot be achieved through the mold alone. Cores must be designed to withstand high temperatures and should fit precisely within the mold.
4
. Melting the MetalNext, the metal intended for casting is melted in a furnace. The type of furnace used may vary, but common types include electric arc furnaces, induction furnaces, and cupola furnaces. The choice of the melting furnace depends on the metal being used, whether it is aluminum, steel, or cast iron. The molten metal must be heated to a temperature that allows it to flow easily into the mold cavity.
steps in sand casting
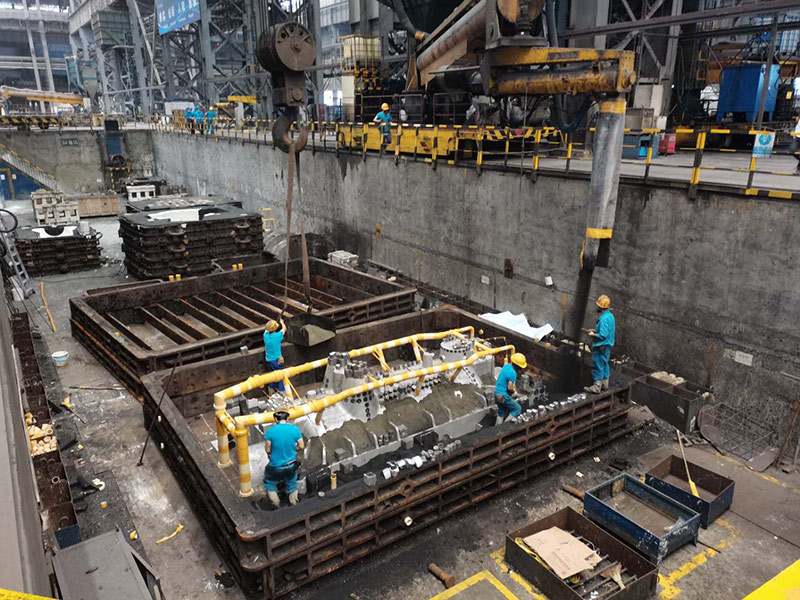
5. Pouring
Once the metal is melted, it is poured into the mold cavity through a pouring basin and down into the mold via a sprue. Controlled pouring is crucial to avoid defects such as turbulence or air entrapment, which can weaken the final casting. Proper techniques and equipment are employed to ensure that the metal fills the mold evenly and completely.
6. Cooling
After pouring, the molten metal needs time to cool and solidify within the mold. The cooling rate can significantly affect the properties of the final product; for instance, rapid cooling can lead to hard, brittle metals, while slow cooling generates ductile and tough casts. This step can take anywhere from a few minutes to several hours, depending on the size and thickness of the casting.
7. Mold Removal
Once the metal has cooled sufficiently, the mold is broken apart to reveal the cast part. This is often done by hand, using tools to carefully remove any sand or other materials that remain attached to the casting. In some cases, mechanical vibrators may be used to expedite this process.
8. Finishing Processes
After the casting is removed from the mold, further finishing processes may be necessary to achieve the desired surface finish and dimensional accuracy. This can include processes such as grinding, sandblasting, machining, and painting. These finishing touches help ensure that the final part meets both aesthetic and functional requirements.
Conclusion
Sand casting is a remarkably adaptable and effective manufacturing technique that has stood the test of time due to its ability to create intricate metal parts with relative efficiency. By understanding the detailed steps involved in the sand casting process, manufacturers can optimize each phase and produce high-quality components suited for a wide array of applications. As technology continues to evolve, innovations in sand casting processes promise to enhance capabilities and efficiency, making it an enduringly important technique in manufacturing industries.
Post time:டிசம்பர் . 16, 2024 05:50
Next:Understanding the Benefits and Process of Lost Foam Casting in Modern Manufacturing