Sand Printing Casting Revolutionizing the Manufacturing Process
In recent years, advancements in manufacturing technologies have sparked innovation across various industries. One of the most groundbreaking methods is sand printing casting, which combines traditional sand casting with modern 3D printing techniques. This innovative process offers numerous advantages, including greater design flexibility, reduced lead times, and significant cost savings.
Sand casting has been a staple in the manufacturing of metal parts for centuries. It involves creating a mold from sand, which is then filled with molten metal to produce complex shapes. However, traditional mold-making can be time-consuming and costly, especially for intricate designs or low-volume production runs. This is where the integration of 3D printing comes into play. By leveraging 3D printing technology, manufacturers can rapidly produce sand molds directly from digital files, streamlining the production process.
One of the primary benefits of sand printing casting is its unparalleled design freedom. Traditional methods often require the creation of complex tooling, which can be a limiting factor in design. With sand printing, the only constraint is the imagination of the designer. This allows engineers and designers to explore innovative geometries and optimize parts for performance while reducing material waste. The ability to easily modify designs also makes it simpler to iterate and refine products, leading to enhanced innovation.
sand printing casting
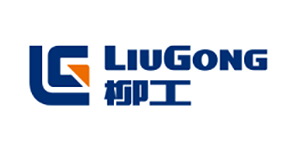
Another significant advantage of sand printing casting is the reduction of lead times. In conventional sand casting, producing molds can take several weeks, especially for complex shapes. In contrast, 3D printing allows for the rapid creation of molds, reducing the time required to go from concept to finished product. This expedited process not only speeds up project timelines but also enables manufacturers to respond quickly to market demands and customer needs.
Cost efficiency is also a critical factor where sand printing casting shines. Traditional tooling for sand casting can be expensive and require substantial upfront investment. By using 3D printing to create sand molds, manufacturers can significantly cut down on these costs, particularly for short production runs or custom parts. Additionally, the reduction in material waste and shorter lead times contributes to overall cost savings.
Furthermore, sand printing casting is more environmentally friendly compared to traditional casting methods. The ability to recycle sand and reduce excess material usage aligns with sustainability goals that many manufacturers are striving to achieve. By minimizing the environmental impact, companies not only enhance their brand image but also contribute positively to the planet.
In conclusion, sand printing casting is transforming the landscape of manufacturing by merging the time-tested techniques of sand casting with cutting-edge 3D printing technology. With its array of benefits—design flexibility, reduced lead times, cost efficiency, and sustainable practices—this innovative process is set to shape the future of production across various industries, making it a game-changer in the manufacturing world. As technology continues to evolve, the potential applications and advantages of sand printing casting will undoubtedly expand, paving the way for even more revolutionary developments in manufacturing.
Post time:நவ் . 20, 2024 03:57
Next:resin with sand