The Art and Process of Sanding Glazed Ceramics
Sanding glazed ceramics is an intricate and essential process that plays an integral role in the creation and finishing of ceramic works. The term ‘sanding’ often conjures images of woodwork or metal fabrication; however, when applied to ceramics, it reflects a unique blend of art and craftsmanship that can enhance both the aesthetic and functional qualities of the piece. This article delves into the importance of sanding glazed ceramics, the techniques involved, and the materials used.
Importance of Sanding Glazed Ceramics
Sanding glazed ceramics serves multiple purposes. One of the primary functions is to smooth out imperfections that may have occurred during the firing process or due to handling. Irregularities such as bumps, drips, or rough edges can detract from the beauty of a beautifully glazed piece. Sanding these areas not only improves the tactile experience but also elevates the visual appeal of the ceramics, making them more attractive to potential buyers or customers.
Additionally, sanding prepares the surface for further treatments. For instance, if an artist wishes to apply a new layer of glaze or paint, a smooth and well-prepared surface is crucial for proper adhesion. Sanding also allows for the customization of pieces; artists can create textures and patterns that can enhance the overall design and uniqueness of their work.
Techniques of Sanding Glazed Ceramics
Achieving a smooth finish on glazed ceramics requires specific techniques and an understanding of different sanding methods. The first step is selecting the appropriate grit sandpaper. Fine-grit sandpaper, usually ranging from 400 to 800 grits, is ideal for sanding glazed surfaces. This finer grit minimizes the risk of scratching the glaze, allowing for a smoother finish without removing too much material.
sanding glazed ceramics
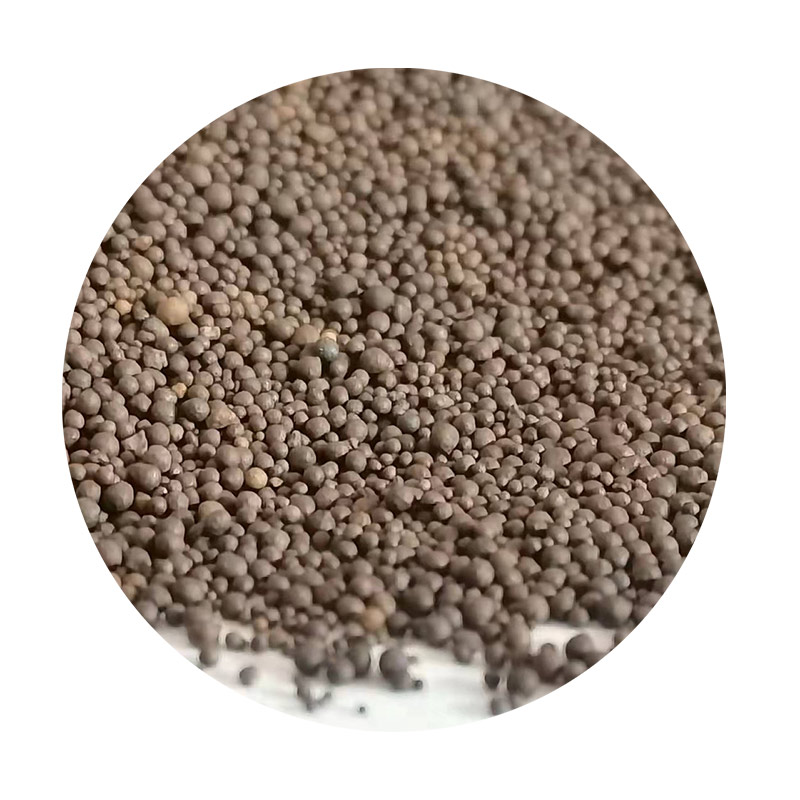
When sanding, it is essential to use a light hand. Excessive pressure can lead to the removal of glaze, which not only alters the piece's design but also exposes unglazed clay, resulting in an unattractive appearance. Working in circular motions can help distribute pressure evenly and create a smoother surface without visible scratches. It is also advisable to keep the surface wet during sanding. This technique, known as wet sanding, reduces dust and allows for easier cleanup. Moreover, the water acts as a lubricant, which helps to minimize scratches and improves the overall finish.
Materials Used in Sanding
Apart from sandpaper, various materials aid the sanding process. Sanding blocks or pads provide additional support and ensure an even application of pressure while sanding. For intricate designs or hard-to-reach areas, artists may use sanding sponges or small hand tools designed specifically for ceramics.
Dust collection systems or masks are also highly recommended during sanding to ensure a safe working environment. Ceramic dust can be harmful when inhaled, making proper ventilation and safety precautions vital.
Conclusion
Sanding glazed ceramics is not merely a finishing touch but a vital component of the ceramic art-making process. It offers artists the ability to refine their works, elevate their aesthetic appeal, and ensure functional durability. By understanding the importance of sanding, employing the right techniques, and utilizing appropriate materials, ceramicists can enhance their creations significantly. Ultimately, the act of sanding symbolizes the dedication and craftsmanship imbued in every ceramic piece, reflecting the artist's commitment to excellence and artistic vision. Whether a seasoned ceramicist or a novice, mastering the art of sanding can lead to improved quality and a deeper appreciation of the ceramic arts.
Post time:டிசம்பர் . 26, 2024 06:33
Next:precision sand casting