The Role of Sand in Metal Casting A Comprehensive Overview
Metal casting is a critical manufacturing process that transforms molten metal into solid objects with desired shapes and properties. Among the various materials used in casting, sand plays a pivotal role, particularly in the sand casting process. This article delves into the importance of sand in metal casting, its properties, types, advantages, and the overall impact it has on casting quality.
Understanding Sand Casting
Sand casting is one of the oldest and most versatile metal casting methods employed in the manufacturing industry. The process involves creating a mold from sand, into which molten metal is poured, allowing it to solidify and take the shape of the mold. The sand used in this process is typically mixed with a binding agent to enhance its cohesiveness and strength.
Properties of Casting Sand
The effectiveness of sand in metal casting is attributed to several key properties
1. Grain Size and Shape The size and shape of sand grains influence the mold's permeability and surface finish. Fine sand can produce smooth surfaces, while coarser grains offer better strength. 2. Thermal Stability Sand must withstand the high temperatures of molten metal without deforming or losing its structure. Silica sand, for instance, has a high melting point, making it ideal for this purpose.
3. Permeability This refers to the ability of the sand mold to allow gases to escape during the casting process. Adequate permeability is crucial to prevent defects such as gas inclusions in the final cast product.
4. Cohesion and Plasticity Binding agents added to sand improve its capacity to hold shape while allowing it to be easily removed from the casting after solidification.
Types of Sand Used in Metal Casting
There are several types of sand utilized in metal casting, each with unique characteristics suited for different applications
1. Silica Sand The most commonly used sand, silica sand, is abundant and cost-effective. It provides good thermal properties and is suitable for a wide range of metals.
sand for metal casting
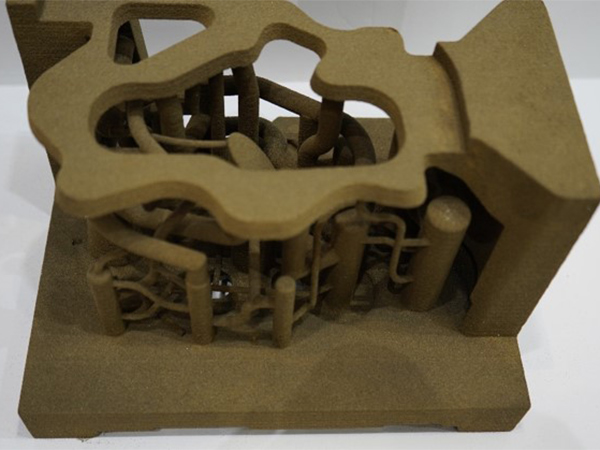
2. Green Sand This is a mixture of silica sand, clay, and water. Green sand molds are moist and possess natural cohesive properties, making them easy to shape and form.
3. Resin-Bonded Sand In this type, chemical binders such as phenolic resin are used to enhance the mold's strength and thermal stability. It is known for producing high-quality castings with excellent surface finishes.
4. Core Sand Used specifically to make cores that create internal cavities in castings. Core sand is typically harder and more rigid than mold sand.
Advantages of Using Sand in Metal Casting
The sand casting process offers several advantages over other metal casting techniques, making it a popular choice among manufacturers
1. Cost-Effectiveness Sand is abundant and inexpensive, reducing overall production costs. The ease of molding and reusability of sand decreases waste materials.
2. Versatility Sand casting can accommodate a wide range of metals, including ferrous (iron and steel) and non-ferrous (aluminum and brass). It is also suitable for producing large or intricate parts that may be challenging with other methods.
3. Capability for Large Parts Sand molds can be easily scaled to produce large castings, which is beneficial for industries that require substantial components, such as automotive and aerospace.
4. Improved Surface Finish With advancements in sand preparation and molding techniques, the surface finish of cast products can be significantly improved, reducing the need for extensive machining.
Conclusion
In conclusion, sand is an indispensable material in the metal casting process. It combines desirable properties that enhance the casting quality, contribute to cost-effectiveness, and support the production of a diverse array of metal parts. As technology continues to evolve, the methods of using sand in metal casting are likely to advance, further refining its application and performance. Understanding the role of sand in this manufacturing process is crucial for industries aiming to optimize their production techniques and ensure the high quality of their casted products. The future of metal casting will undeniably remain intertwined with the enduring significance of sand.
Post time:நவ் . 25, 2024 10:25
Next:Benefits of Using Sand Casting Techniques in Manufacturing Processes