Understanding the Different Types of Sand Used in Sand Casting
Sand casting is one of the oldest and most versatile metal casting processes, widely utilized across various industries to produce complex metal parts. The choice of sand is pivotal in achieving successful casting results, as it plays a significant role in mold making and overall casting quality. This article will delve into the different types of sands used in sand casting and their respective properties and applications.
1. Silica Sand
Silica sand is the most common and widely used type of sand in sand casting. Composed primarily of silicon dioxide (SiO2), it possesses excellent thermal stability and high strength, making it suitable for molding. Silica sand grains are typically angular and have a high melting point, which helps in withstanding the thermal shock encountered during the casting process. Additionally, its availability and cost-effectiveness have made it the go-to choice for many foundries. However, it should be noted that silica dust can be hazardous when inhaled, necessitating appropriate safety measures during handling.
2. Green Sand
Green sand is a mixture of silica sand, clay, water, and other additives. It is called green not due to its color but because it is used in a moist state. The presence of clay provides the plasticity and strength necessary for forming molds. Green sand molds can be reused multiple times, making this method both economical and efficient. This type of sand is particularly popular in iron and aluminum casting, as it produces smooth surface finishes and can accurately reproduce intricate details of patterns.
3. Resin Sand
sand casting sand types
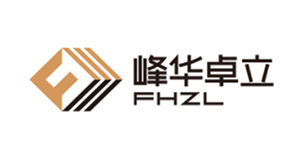
Resin sand is a mixture of silica sand and a resin adhesive. Unlike green sand, resin sand does not require moisture to bind particles, as the resin provides necessary cohesion. This type of sand is particularly valued for creating complex and high-precision castings due to its superior strength and low thermal expansion. Additionally, resin sand molds can withstand higher temperatures, making them suitable for casting materials with low melting points. Although it can be more expensive than green sand, the quality of the final products often justifies the cost, especially in industries where precision is paramount.
4. No-Bake Sand
No-bake sand is another variant that utilizes a chemical binder instead of a resin to bond the sand particles. This type of sand does not require moisture and is mixed with a catalyst, which hardens the sand when it is poured into a mold. The advantages of no-bake sand include its ability to create high-strength molds with excellent surface finishes. It is particularly useful for producing complex shapes and can tolerate higher temperatures compared to traditional sands. However, it can be more labor-intensive to work with and may require specialized equipment.
5. Shell Molding Sand
Shell molding sand consists of fine silica sand coated with a thermosetting resin. This process involves heating a pattern to create a shell of hardened sand around it, forming a highly accurate mold. Shell molding offers excellent dimensional accuracy and surface finish, making it suitable for intricate components requiring tight tolerances. The modularity of this method allows for rapid production cycles, making it a favored choice in industries with high demand for precision castings, such as automotive and aerospace.
Conclusion
The selection of sand for sand casting significantly influences the quality, efficiency, and cost-effectiveness of the casting process. Each type of sand has its unique properties, advantages, and limitations, making it crucial for manufacturers to understand their specific needs and choose accordingly. Whether utilizing silica sand for its affordability, green sand for its reusability, or resin sand for precision, the right choice can enhance the practicality and performance of casting operations. As technology advances, new compositions and processes may arise, further expanding the possibilities within the realm of sand casting.
Post time:நவ் . 07, 2024 18:41
Next:How to Create Sand Castings for Metal Fabrication Projects