Understanding Sand Casting Manufacturers The Backbone of Foundry Production
Sand casting is one of the most traditional and widely used methods for metal casting. This process involves creating a mold from sand to obtain a desired shape and, subsequently, pouring molten metal into the mold. Sand casting manufacturers play a crucial role in various industries, including automotive, aerospace, and machinery, as they provide both the expertise and the infrastructure necessary to produce high-quality cast components.
One of the primary advantages of sand casting is its versatility. Manufacturers can create complex shapes and sizes, making it suitable for a wide range of applications. From small parts to large components, the sand casting process can accommodate the needs of different sectors. This flexibility is one reason why sand casting remains a popular choice despite the rise of advanced manufacturing processes.
Sand casting manufacturers utilize various types of sand, most commonly silica sand, which offers excellent thermal properties and a fine texture. Other materials such as clay, water, and additives are combined with the sand to enhance its binding properties and improve mold strength. The preparation of the sand mixture is a critical step, as it affects the quality and accuracy of the final product. Manufacturers invest in state-of-the-art equipment and technologies to ensure that their sand preparation meets the required specifications.
sand casting manufacturers
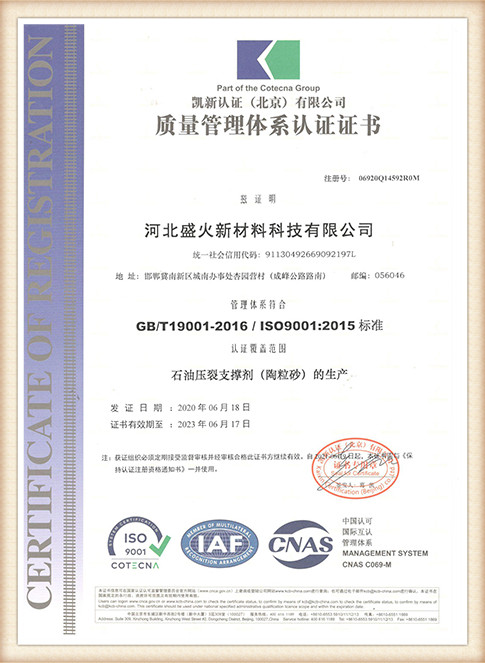
The process of sand casting begins with creating a pattern, which serves as a replica of the desired final product. This pattern is often made from metal, plastic, or wood and is used to form the mold. Once the pattern is in place, the sand mixture is packed around it, and the mold is created. After removing the pattern, the mold is ready for pouring molten metal. This phase requires precision and careful handling, as the correct pouring temperature and timing directly influence the integrity and properties of the cast component.
After the pouring process, the cast component must be cooled before it can be removed from the mold. This cooling period allows the metal to solidify and take on the shape of the mold. Once it is removed, the part may undergo further finishing operations, such as sandblasting, machining, or surface treatment, to achieve the desired surface finish and tolerances.
Quality control is a fundamental aspect of the operations at sand casting manufacturers. They conduct thorough inspections throughout the entire process to ensure that every cast component meets stringent industry standards. Advanced testing methods, such as X-ray inspection, are often employed to detect any internal defects that may compromise the integrity of the final product.
In conclusion, sand casting manufacturers are vital to the production of metal components across various industries. Their expertise in manipulating the sand casting process—coupled with advanced technologies—enables them to produce high-quality, durable parts. As the demand for customized and complex castings continues to grow, the role of sand casting manufacturers will remain indispensable in the manufacturing landscape. Whether it is for large-scale industrial applications or specialized components, sand casting remains a cornerstone of metalworking, thanks to the dedicated manufacturers behind it.
Post time:செப் . 22, 2024 02:01
Next:how sand casting works